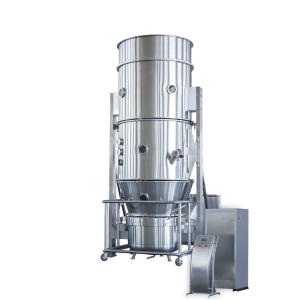

Add to Cart
Direct Selling Choline Chloride High-Efficiency Vertical Fluidized Bed Dryer
This machines is suitable for drying for powder and granules. The
principle of action is based on: Put the raw material into the
fluid bed. The cold air is drawn into the fluid bed through the pre
filters and passes through the heating chamber behind the main
machine, heated to the desired temperature by the heater. The
material is fluidized in the fluid bed regularly . The evaporating
moisture is drawn out by the fan.
Features
The machine is mainly used for the operations of mixing,
granulating, drying and coating of granule “Top Spraying”, etc of
powder material in pharmaceutical industry, foodstuff industry,
chemical industry, etc. Such as granule of tablet, granule for
quick resolving drinking, condiment.
Mixing-granulating-drying in one-step.
Adopting double chamber filtering bags system, removing dust
completely.
Adopting multi-fluid nozzle, it guarantees that the formed granule
is uniform and the content of powder is very low.
Can choose 2 bar explosion-proof design.
Designed, manufactured and laid out by GMP.
Specifications
Model | 60 |
Volume (L) | 220 |
Amount to be treated (kg/per time) | 90 |
Power of fan(kw) | 11 |
Consume of steam 0.4MPa(kg/h) | 141 |
Consume of compressed air (m3/min) | 1.0 |
Noise,dB(A) | (fan is installed separately) ≤75 |
Application
Fluid-bed processing is mainly used for the mixing of powder
material, drying and granulating (coating) in pharmaceutical, food,
chemical, agricultural and sideline product processing industries,
such as tablet, instant powder and condiment granules. The process
of feeding and discharging material for this equipment should be
finished in the airtight space to avoid the powder spreading to the
working environment. It‘s controlled by PLC. For wet type
granulating machine, it adopts negative pressure or air blast to
make the finished granules enter the fluid bed for drying in
airtight way.
Brief introduction for top spray system
It consists of a cone-shaped material trough and diffusion
(spraying) chamber. The processing airflow passes through the
airflow distribution board and screen net from the trough bottom to
enter this equipment. When the flow rate of inlet air overcomes its
gravitational force, the material in trough can form eddy flow to
move (fluid bed).
1.The inlet airflow from the bottom up will push the material in
the trough to move upward. As with a certain angle of the trough,
the aggregative fluidization of the material in it is very intense.
2.The material pushed by the airflow, enters into the diffusion
chamber. As the space of diffusion chamber is larger than that of
trough, the air flow velocity in chamber will be lower than in
trough and the speed of material granules in chamber will decrease.
When the gravity force of granule itself overcomes the pushing
force of inlet airflow from the bottom up, it will fall down and
return to the edge area of trough. In the whole process, the
granules will move back and forth between diffusion chamber and
trough to form irregular fluidization.
3.The aim of granulating machine is using fine powder to produce
dust-free and flexible granules. Coating refers to coat for those
finished fine and uniform granules.
When granulating and coating with top spray device of fluid bed,
the powder or granules rise from the trough bottom in fluidized
state; the adhesive or coating liquid is sprayed to the fluid bed
by the nozzle of spray gun installed in the diffusion (spraying)
chamber to granulate or coat the material. Via the thermal current
entering from bottom and heated airflow distribution board to do
heat exchange, the material will be dried.
In the phase of material being blown by air, the surface of each
granule will be fully showed in the airflow so that it can achieve
the best atomizing spray medium and drying result.
The top spray technique is suitable for drying process. Dismount
the spray gun in diffusion (spraying) chamber, the top spray device
turns to be a fluid bed drier.