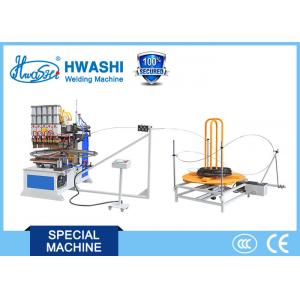

Add to Cart
Industrial Fan Guard Welding Machine for Spiral Wire Fan Guards
This machine is special for automatic coil winding, welding and rotating of spiral fan guard. The machine is equipped with 3 sets of welding heads, automatic rotating system, and automatic wire feeding and winding system. Operator only needs to put the wire into horizontal fixture, the coil winding system will operate automatically. Then the welding electrode will be operated separately to weld the spiral wire fan guard.
This machine can achieve automatic rotation, mobile, and welding so as to increase product quality and efficiency and lower the production cost. It helps to solve the defects of unstable quality and low efficiency.
Main design :
Main Body: The main body is made of reinforced good quality steel plate. According to the product, it is designed as three groups of up and down electrode, and two groups of left and right electrode. Only need to adjust the electrode moving distance can meet the requirement of welding different diameter of product. Reasonable vertical structure. Ensure the main body has enough rigidity and stability to support the machine when conducting high speed welding. The machine is equipped with slideway. The main body could offer stress supporting point and working platform for other actions.
Power Supply System: Adopt one set of medium frequency inverter
100KVA special resistance welding transformer as the welding power
source. Duty cycle rate is 50%. The three-phase power supply,
through rectified by a special inverter, is converted into 1000Hz
AC voltage and then is transmitted to a medium frequency
transformer. The current is rectified in order to supply DC welding
current. This power source is different from the general type ac
pulse power source because it can adjust rapidly and precisely.
Small impact to the power grid and the requirement to the power
grid capacity is much lower than the single-phase welder with the
capacity.
Advantage: three-phase input; small impact to the power grid;
medium frequency DC output; no impedance loss to the circuit; high
thermal utilization factor; the precision setting of welding time
is high which can reach 1/1000sec; large instantaneous current;
prevent deformation and color change on the product.
Welding Control System: Adopt the self-developed HSMF1-400
intelligent microcomputer quick response touch controller,
all-digital control, simple and clear operational interface.
Automatic testing and compensation which could guarantee the
situation that the machine will be at work only when the current
value is in the preset data so as to ensure the stability of
welding effect and effective prevention of undesirable phenomena
like loose welding and cold joint. The features of quick response
and high precision of control may help you obtain high quality of
welding spots.
Pressurized Mechanism: Adopt cylinder as the pressurized source
which is control by good quality of imported electromagnetic valve
and coordinated with precision-machined linear slide to pressure
the electrode tip. The pressure of each welding head could be
adjusted independently to ensure the stability of welding machine.
Adopt the working manner that the bottom bears the stress from the
top to guarantee the good contact, unimpeded, constant resistance
value of secondary circuit and stable transmission of output
current of welding transformer. Guarantee to obtain high efficient
and good quality of welding spots.
Main Engine Control System: Adopt the touch screen of Japan
Panasonic as the human-machine interface, English input. The PLC,
as the control hub as the whole machine, is in charge of reading,
transmitting and controlling all kinds of signal processing and
coordinating with various external instructing transmission signal
mechanism in order to ensure the validity of all orders of
execution of the machine. The self-detection of all automatic
testing stations effectively eradicates the occurrence of
malfunction and other accidents. When the pressure, current, air
pressure, hydraulic pressure, temperature or other testing signals
are in abnormal situation, the machine will give an alarm to
prevent any insecure accidents.
Automatic Coil Winding System: Design as X, Y, L three axle linkage
mode. Conduct automatic equidistance moving, automatic rotating,
automatic pressing and stepping to track mould with sliding block.
Automatic Rotating System: Servo motor and 600mm rotary table
consist of rotation system. Easy adjustment, quick response and
high control precision. It can achieve cycle working.
Work process:
Put the wire skeleton onto the fixture manually——Then the wire will fixed by wire winding mechanism——press start button——Automatic winding institutions cooperate with rotary motor will send the wire into the mould in turns.——winding completed——cut the wire and fixed the wire at the end——start welding——Welding mechanism conduct welding automatically according to the setup program——rotary motor rotate mold automatically, which can make work piece conduct welding in turns——welding completed——the work piece will be taken out of the mold automatically by unloading cylinder——work piece unloading——the equipment work circularly.
Technical Specifications:
No. | Item | WL-SQ-MF100K |
1 | Input Power | 100KVA |
2 | Input Voltage | 380V Three-Phase |
3 | Input Current | 150A |
4 | Duty Cycle Rate | 50% |
5 | Max Short Circuit Current | 28000A |
6 | Welding Models | 101 types |
7 | Max Secondary No Load Voltage | DC11.6V |
8 | Continuous Working Current | 20KA |
9 | Welding Transformer Insulation Grade | F |
10 | Pressing Curve | 2 types |
11 | Welding Electrode | 4+2 |
12 | Max Welding Width | 150mm |
13 | Automatic Coil Winding Rotating Speed | 300-500mm/sec |
14 | Welding Electrode Stroke | 80mm |