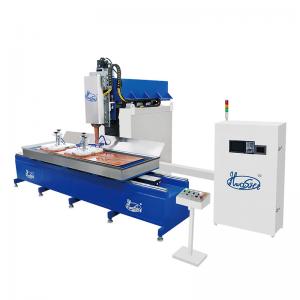

Add to Cart
CNC 3 Axis Control Stainless Steel Kitchen Sink Seam Welding
Machine
Product Description
CNC 3 Axis Control Stainless Steel Kitchen Sink Seam Welding
Machine is a method that uses a pair of roller electrodes instead
of the cylindrical electrodes of spot welding, and the welded
workpiece moves between the rollers to produce a sealed weld with a
molten core overlapping each other to weld the workpiece together.
Adopt medium frequency inverter power source of welding and large
flat platform of locating method. Use the servo motor to drive X
axis (locating mould) and Y axis (welding electrode) to operate
under the preset procedure of PLC data. According to the stored
position of welding spot, the welding product will be located
inside the mould and moves horizontally along the X direction. The
welding electrode will be designed to move vertically along the Y
direction. The welding electrode is able to conduct 360° of
rotation under the control of servo motor so it is suitable for
welding different angles of products.
Suitable for welding the sink within the range of 1600x700x300mm.
(customized)
Japan Mitsubishi CNC Control System Adopts three sets of Japan Mitsubishi servo motor to control axis X (movement of sink mould), axis Y (vertical movement of welding wheel), and axis A (360° rotation of welding wheel). | Auto Moving Welding Table Specially designed electrode large table, more stable conductivity, to ensure the effectiveness of welding. |
Big Copper Flat Table Electrode and Fixture We will design the fixture according to the design of your sink bowl. Different sizes may require different fixtures. Be able to do welding of single bowl, double-bowl, or three-bowl product | Welding electrode Synchronized operation of welding electrodes and Moving Welding Table, Automatic welding of sink, Uniform and beautiful welding seam. |
Special Design Grinding Belt | Auto Moving Table and Fixture Structure |
Brown belt (fine abrasive belt) DEERFOS RA631 150# Blue belt (coarse abrasive belt) 577F P80Y The movement and control system will be the same as the sink seam welding machine | For sink bowl within 1500mm, we can choose to use fixed table with adjustable fixture. For sink bowl over the limit, we can design the automatic moving feeder to achieve full automatic grinding and polishing. |
CNC Sink Seam Welding Machine | Model | WL-AMF-160K |
Input Power (V/φ) | 380V 3φ | |
Rated Power (KVA) | 160/250KVA (as per material thickness) | |
Applicable Material | Stainless Steel 304/201 | |
Material Thickness | 0.8~1.5mm (customized) | |
Effective Welding Length | 1600-3000mm (customized) | |
Effective Welding Width | 600-800mm (customized) | |
Sink Bowl Shape | Square/Rectangular/Round | |
Welding Efficiency | about 40-60sec/bowl (depend on the size of bowl) | |
CNC Sink Edge Grinding and Polishing Machine | Max. Moving Speed | 500mm/sec |
Belt Rotation Speed | 1200R/min | |
Min. Radius | R40 | |
Rated Air Pressure | 0.6MPa | |
Grinding Efficiency | about 60-80sec/bowl (depend on the size of bowl) |
This CNC sink grinding special machine utilizes abrasive belt
polishing principle. The abrasive belt is driven by electric motor
to conduct polishing on the edge of the welded sink. There are two
processes for polishing. Firstly, use the coarse abrasive belt to
grind the redundant cutting edge and the projection welding spots.
Then use the fine abrasive belt to conduct polishing treatment.
After these two processes can meet the requirement of sink grinding
and polishing treatment. It is designed to use Mitsubishi
professional automatic control system. You only need to input the
coordinate data of the product and start the machine, the abrasive
belt of the machine will conduct grinding and polishing
automatically within the track of preset program. The worker only
needs to put and take out the sink.
The product will be fixed on the locating mould. The servo motor
will drive the X and Y axle to run within the preset data of
program. The machine could store 15 types of grinding models. The
grinding wheel will move along with X direction and the max moving
range is 1220mm while the max moving range of Y direction is 620mm.
The Z axle can conduct moving up and down within the range of max
250mm while the A axle can conduct 360ºrotating under the control
of servo motor. This machine is suitable for different directions
of product.