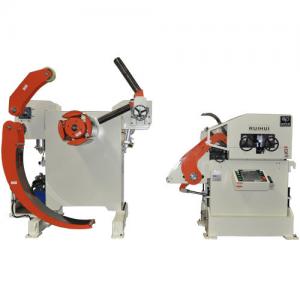

Add to Cart
Unwinding equipment, Guangzhou pre-embedded stamping feeder, Ruihui automatic feeder
Due to its advantages of simple operation, good stability, large bearing capacity, high degree of customization and long service life, the heavy-duty material frame has become the most used material for unloading and unwinding in stamping processing.
The heavy-duty material frame is famous for its high stability and service life. The main frame is made of steel, A3 steel plate and #45 steel forged bearing seat. The wall plate, hole position and main parts are all welded. It is machined by CNC machining center. The materials of bearings, gears and spare parts are all made of the highest standards in the industry.
Heavy material rack maintenance:
1. Before starting the machine, check the grounding condition of
Ruihui heavy-duty material frame to ensure good grounding and avoid
damage to the electrical equipment and personnel damage caused by
improper grounding.
2. Before starting the machine, check the support tile of the material frame up and down roll to check the wear of the surface; at the same time, check the tightening of the bolts and the sliding shaft of the expansion and contraction drum and whether the bearing seat is damaged. It is fastened or replaced.
3. Open the electric control box and check the fastening condition of each contact in the electric control box to ensure that the contact parts are not loose, so as to avoid damage to the electrical equipment or sudden failure during use.
4. After long-term use, add grease to the material frame spindle bearing once every month (or working time reaches 260 hours). Open the rear frame of the material frame every six months (or working time up to 1500 hours). To replace the oil for the reducer, the oil change amount can be added to the 1/2 between the axle and the rod.
Specification:
Model | MAC2-400 | MAC2-500 | MAC2-600 | MAC2-800 | ||
Stock Width(mm) | 50-400 | 50-500 | 50-600 | 50-800 | ||
Stock Thickness(mm) | 0.3~3.2 | 0.3-3.2 | 0.3-3.2 | -3.2 | ||
Max.Coil Weight(kg) | 3000 | 3000 | 3000 | 5000 | 5000 | 7000 |
Max.Coil O.D.(mm) | 1200 | 1200 | 1200 | |||
Coil I.D.(mm) | 8 | 8 | 508 | 508 | ||
Feed Length(mm) | ~500* | ~500* | ~500* | ~500* | ||
Max. Line Speed(m/min) | 16-24 | 16-24 | 16-24 | 16-24 | ||
Work Roll Number(pieces) | upper 6 lower 5 | upper 6 lower 5 | upper 6 lower 5 | upper 6 lower 5 | ||
Feed Roll Number(set) | 1 | 1 | 1 | 1 | ||
Main Motor(kw) | AC2.9 | AC2.9 | AC4.4 | AC4.4 | ||
Mandrel Expansion | hydraulic | hydraulic | hydraulic | hydraulic | ||
Reel Motor(kw) | 1.5 | 1.5 | 1.5 | 2.2 | 2.2 | 3.7 |
Power(V) | 3 Phase 220V/380V/50HZ | |||||
Operating Air(Mpa) | 0.49 | 0.49 | 0.49 | 0.49 |
Straigtening performance:
tock Thicknees (mm) | Stock Width (mm) | |||
0.3 | 400 | 500 | 600 | 800 |
0.4 | ||||
0.6 | ||||
0.8 | ||||
1.0 | ||||
1.2 | ||||
1.4 | ||||
1.6 | 470 | 470 | ||
1.8 | 400 | 400 | ||
2.0 | 360 | 360 | ||
2.3 | 300 | 300 | 300 | 300 |
2.5 | 230 | 230 | 230 | 230 |
2.8 | 150 | 150 | 150 | 150 |
3.2 | 110 | 110 | 110 | 110 |
*1:(Pneumatic):Option in case of pneumatic mandrel expansion is
provi