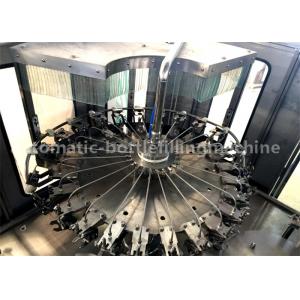

Add to Cart
Simply description:
This water filling machine is with bottle rinsing, filling and capping monobloc for drinking water (non-carbonated) filling.PET bottles infeed by combination of infeed grippers, equipped with bottle jam protection device, the machine applies unique overturning bottle clamp, which is an innovation of our Zhangjiagang Jiayuan machinery company .
Machine frame
The machine frame is a welded structure of high quality carbon
steel with the surface anti-rust treated and coated, the machine
frame is wrapped with stainless stell SUS304.
Driving system of the 3-in-1 unit is positioned under the machine
talbe. One main motor provides driving porwer via gear
transmission.
The gear transmission system is an interleaved arrangement of stell
gears and nylon gears.
The output shaft of the main motor is equipped overload protection
to secure machine safety.
PLC electrical control system controls the fully automatic
operation of the monobloc.
Technical parameter:
Model | CGF16-12-6 | CGF18-18-6 | CGF24-24-8 | CGF32-32-10 |
Production capacity(500ml)(b/h) | 2000-4000 | 4000-6000 | 8000-10000 | 12000-15000(0.5L) |
Filling precision | ≤±5MM(Liquid Level) | |||
Polyester bottle standard(mm) | Bottle diameter40-80; | |||
Height | Height:130-280 | (Height):150-320 | ||
Suitable cap shape | Plastic Screw Cap | |||
Water pressure of Washing bottle(MPa) | 0.18 | |||
Water consumption for Water bottle (kg/h) | 800 | 1600 | 2500 | 3500 |
Spraying position | 5 | 5 | 6 | 12 |
Dripping bottle position | 3 | 3 | 3.5 | 7 |
Gas source pressure(Mpa) | normal pressure | |||
Gas consumption(m3/mm) | 0.3 | 0.3 | 0.4 | 0.5 |
Total power | 4.23 | 5.03 | 6.57 | 8.63 |
Total weight | 2000 | 3500 | 5500 | 8000 |
Dimension(L*W*H) | 2100×1500×2200 | 2450×1800×2200 | 2750×2180×2200 | 3500×2200×2250 |
Filling part
Rotary wheel fully made of stainless steel SUS 304
Gravity filling method
Filling valves aer reasonably structured with accurate filling.
Bottle go up and down in the function of cam through elevator to process filling with contact to bottle-mouth.
Level of cylinder is controlled with float-ball
Filler is driven through gears inside the machine frame.
Link-wheels in rinser, filler and capper are transported in ringed
support of bottle-neck.
Capping part
Capper should have highest precision, influence very much with stability and realiable of the filling monoboc. Our capper
features as follows:
Cap distributing chute is equipped with reverse cap stop and
reverse cap pick-out mechanism.
Cap distributing chute is equipped with a photocell switch to stop
the capper when there is no cap inside the chute.
The capper is equipped with inlet bottle detection switch.
Centrifugal way of cap arranging is adopted to reduce damage of
caps.
A cap inspection system is applied to control on-off of elevator.