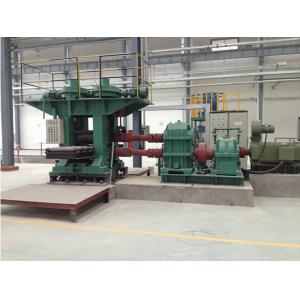

Add to Cart
Steel Rod Hot-rolling Mill Proposal
120 Square Billet to Roll Φ 10 ∽Φ 36 steel rod
150,000tons/year
1.Steel Rolling Process
Hang qualified raw material to the feeding roller bed by crane,
convey to the heating furnace tail, push to the heating furnace to
heat by steel pusher. When material is heated to 1100-1200℃, it
will be pushed out by discharge machine to rolling mill to be
consecutively rolled 9 to 19 times. In order to prevent the rolling
accident caused by irregular parts and low temperature parts, set
rotary cutting flying shears between rough
rolling(φ450×3+Φ450×2×2)and middle rolling(φ320×2×3), middle
rolling and finishing I rolling(φ280×2×2). In order to minimize the
processing time of rolling accident, set tensile shears and cutting
shears before the hot material entering the mill entrance and
finishing II rolling(φ280×2×3). Of course, the two rotary cutting
flying shears also have the function, in order to ensure products
quality and easy adjustment, set side movable sleeve and vertical
movable sleeve between middle rolling and finishing I rolling,
finishing I rolling and finishing II rolling.
Products rolled by the mill are sent by the pinch roll to rotary
double-rule flying shear to be cutted into double-rule, then enter
into upper steel pusher cooling bed to be cooled through clip tail
roller after reducing the speed. When the products on the cooling
bed surface step by step, in the meanwhile, the evener on the bed
surface evens the products’ front, gather the products into
collection agencies by dynamic tooth. When the products have been
collected a certain quantity, collection agencies will translate
them to under the table to be cut into scale, passing by the
products inspection gathered in the products collection device,
then packing, weighing, signing and piling in the storage.
2.Heating furnace
3.Electric
4.Production water supply, water draining and water treatment
5.Ventilation
6.Instrument
7.Construction
8.Environmental Protection, Security, Industrial Hygiene and Fire protection
9.Equipment List
No. | Equipment Name | Qty | Weight(t) | Remarks | |
1 | Charging roller | 2groups | 7 | ||
2 | Steel pusher | 1pc | 3 | Don’t include the hydraulic station | |
3 | Heating furnace | 1set | |||
4 | Discharge machine | 1pc | 5 | ||
5 | Furnace delivery table | 1group | 8 | ||
6 | Tensile shear | 1pc | 1 | ||
7 | Φ450×3 continuous rough rolling mill | 1group | 80 | ||
8 | φ450×2 continuous rough rolling mill | 2groups | 60×2 | ||
9 | φ320×2 middle rolling mill | 3groups | 40×3 | ||
10 | φ280×2 continuous finishing rolling mill | 3groups | 20×3 | ||
11 | 1# head cutting flying shear | 1pc | |||
12 | 2# head cutting flying shear | 1pc | |||
13 | Movable sleeve device | 2pcs | 4 | ||
14 | Pinch roll | 2pcs | 2 | ||
15 | Double-rule flying shear | 1pc | |||
16 | Upper steel pusher | 1set | 10 | ||
17 | Cooling bed | 1pc | 100 | ||
18 | Uniform equipment | 1set | 2 | ||
19 | Lower steel pusher | 1set | 5 | ||
20 | Lower roller | 10groups | 15 | ||
21 | Constant sheer | 1pc | 10 | ||
22 | Fixed size baffle | 2pcs | 2 | ||
23 | Finished product cross test bench | 1pc | 10 | ||
24 | Collection device | 1set | 3 | ||
25 | Electric equipment | 9pcs | Main motor DC700KW:1pc DC400KW:8pcs | ||
26 |
| Rectifier transformer | 3pcs | ||
27 | Power transformer | 1pc | |||
28 | Electric control equipment | 1set | |||
29 | Process guide | 1set | |||
30 | On-site installation main and auxiliary materials | Hydraulic station | 1set | ||
31 | Dilute oil lubricating station | 2sets | |||
32 | Water supply and drainage equipment | 2sets | |||
33 | Cross trolley | 2pcs |