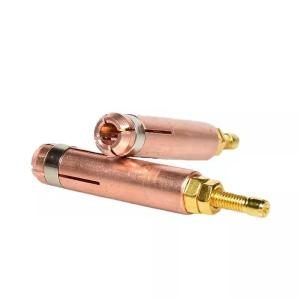

Add to Cart
1 . Stud Welding Applications: What Can Stud Welding Be Used For? Stud welding is a highly versatile process for attaching fastenings to metal sheets. Using weld studs, operators can au tomatically or manually form welds of superior strength. As a result, there are many stud welding applications available.
Stud welding is a technique similar to flash welding where a fastener or specially formed nut is welded onto another metal part, typically a base metal or substrate. The fastener can take different forms, but typically fall under threaded, unthreaded, or tapped. The bolts may be automatically fed into the stud welder. Weld nuts generally have a flange with small nubs that melt to form the weld. Weld studs are used in stud welding systems. Manufacturers create weld studs for the two main forms of stud welding: capacitor discharge stud welding and drawn arc stud welding
2 . Capacitor discharge stud welding
Capacitor discharge stud welding differs from drawn arc stud
welding, in that capacitor discharge welding does not require flux.
The weld time is shorter, enabling the weld to bond with little
oxidation and no need for heat concentration. It also allows for
small-diameter studs to be welded to thin, lightweight materials.
This process uses a direct-current arc from a capacitor. The weld
time in this process is between 1 and 6 milliseconds. Capacitor
discharge stud welding with the latest equipment can create a weld
without burn-through showing on the opposite side of very thin
metals. CD stud welding is often used for smaller diameter studs
and pins, as well as on non-standard materials and for accuracy.
Drawn arc stud welding is primarily used for structural purposes
and larger diameter weld studs.
3. Pictures