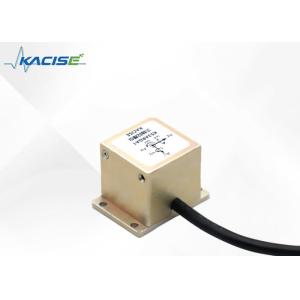

Add to Cart
The KS3ARGA1 Series Three-Axis Universal Angular Rate Gyro is a state-of-the-art sensor engineered by Kacise. This innovative device is meticulously crafted to measure the angular rate across three axes. It utilizes the advanced MEMS (Micro-Electro-Mechanical Systems) technology for each axis, which guarantees exceptional performance, economic efficiency, high dependability, and superior structural integrity. Additionally, the gyro is outfitted with a robust Self-Test feature, enhancing its functionality and user trust.
The operation of the KS3ARGA1 series is grounded in the fundamental
physics of the resonator gyro. This sensor incorporates dual
polysilicon sensitive structures, each fashioned with a
high-frequency vibrating frame. The frames, charged through
electrostatic forces, exhibit resonant behavior, which is pivotal
for gauging velocity.
At each end of the vibrating frame, you will find a
capacitive-sensitive structure adept at responding to Coriolis
forces that occur with angular movement. Such interactions lead to
the generation of an electrical charge. These signals, once
created, progress through both amplification and modulation
circuits, culminating in an electrical output that bears a direct
correlation to the angular rate being measured.
● low power consumption
● wide operating temperature range
● wide bandwidth
● small size
● DC input DC output
● fast start
● high performance, low cost
Dimensions
Parameter | KS3ARGA1 |
Power supply parameter | |
Input voltage | 6-15V(Vdc) |
Incoming currentmA | <30 mA |
Offset voltage | 2.5±0.05(V) |
Output voltage | 0.5-4.5(V) |
Product performance | |
Range | ±250(°/s) |
Scaling factor | 8±0.5(mv/°/s) |
Nonlinearity | ≤0.05(%FR) |
Resolution/Threshold | ≤0.1(°/s) |
Cross coupling | ≤2(%) |
Output noise | <0.02(°/s√Hz) |
run-up time | ≤20(ms) |
Bandwidth can customize | 80(Hz) |
G-value sensitivity | <0.02(°/s/g) |
Mean time between failures | 100000hour(MTBF) |
Size | 34×25×24(mm) |
Weight | ≤40(g) |
Environment | |
Operating temperature range | -45~+80(°C) |
Storage temperature | -65~+125(°C) |
Tolerated acceleration | 20000(0.1ms)(g) |
In the realm of technology, particularly in the transportation and
imaging sectors, certain key systems stand out for their
contribution to safety, accuracy, and functionality. These systems
are integral components in a variety of devices and vehicles and
are essential for modern operations.
Automotive Electronics: This term encompasses a vast array of electronic systems used in
motor vehicles. These include everything from engine management
systems to infotainment. Automotive electronics enhance the driving
experience by providing better control, safety features, and
convenience.
Aircraft Guidance and Control: This complex system is pivotal in navigating and managing the
flight of an aircraft. It ensures that the plane follows the
intended path and adjusts for various flight conditions,
contributing to the safety and efficiency of air travel.
Attitude Reference System: Also referred to as an Attitude Indicator, this system provides
pilots with essential information about the orientation of the
aircraft relative to Earth's horizon. It is crucial for maintaining
the correct aircraft attitude during flight.
Platform Stabilization: Whether it's for a ship, airborne camera, or any other platform
that requires a stable base, platform stabilization systems are
employed to maintain a steady position irrespective of the motion
due to external forces, contributing to operational stability and
precision.
Robot and Antenna Stabilization: Precision and steadiness are also vital in robotic operations and
communication systems. Stabilization technologies help in
maintaining the proper orientation for robots and antennas,
ensuring accurate performance and signal transmission.
Camera and Digital Camera Gyros: Image clarity is paramount in photography and videography.
Gyroscopic stabilizers in cameras and digital cameras compensate
for movement and shaking, resulting in clear, stable images even
when captured in motion or challenging conditions.
Our Electronic Gyroscope Sensor is designed with precision to
provide reliable performance for your applications. Our support
includes detailed product documentation, an extensive online
knowledge base, and troubleshooting guides to help you resolve any
issues you may encounter.
We are committed to the satisfaction of our customers and strive to
provide exceptional after-sales support. Should you have any
feedback or suggestions, we welcome your input as it helps us to
continuously improve our products and services.
Packing and Shipping:
The Electronic Gyroscope Sensor is housed in a robust, anti-static
packaging to ensure the device remains secure and undamaged during
transit. The interior of the packaging is lined with a cushioning
material that absorbs shocks and vibrations, providing additional
protection for the sensitive components of the sensor.
Prior to shipment, each package is sealed and subjected to a
thorough inspection to guarantee that the sensor is securely
enclosed. The exterior of the packaging is clearly labeled with
handling instructions and the package contents to facilitate
careful handling and to inform the recipient about the enclosed
device.
For shipping, the packaged Electronic Gyroscope Sensor is placed in
a larger, durable cardboard box designed to withstand the rigors of
transport. This box is further secured with packing tape and, if
necessary, additional cushioning materials are added to prevent
movement within the box during shipment.
Each shipment includes a detailed packing slip with product
information and a unique serial number for inventory tracking and
quality control purposes. The package is then dispatched through a
reliable courier service with options for tracking and insurance to
ensure the Electronic Gyroscope Sensor arrives at its destination
promptly and in pristine condition.