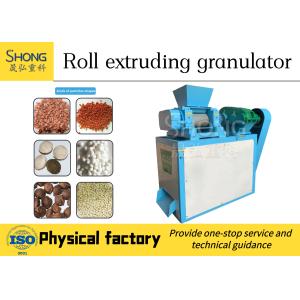

Add to Cart
Ammonium Sulphate Fertilizer Granulator Production Line
Introduction of ammonium sulphate fertilizer granulator production
line
Ammonium sulphate fertilizer granulator production line is widely
used in producing chemical fertilizer, NPK fertilizer and the
capacity ranges from 5,000-200,000 tons/year. It is mainly used for
producing spherical particles with a diameter ranging from 1mm to
5mm.This equipment can specially used for processing compound
fertilizers with different concentrations and types, such as
organic fertilizer, inorganic fertilizer and biological fertilizer,
etc.
Advantages of ammonium sulphate fertilizer granulator production
line
1.Widely suitable for compound fertilizer, chemical, fodder and so
on.
2.Adopts advanced granulator, granulating ratio is up to 90%, with
high intensity.
3.The inner cylinder body adopts high quality rubber plate lining
structure which prevents the raw material from sticking on the
plate.
4.Stable performance, anti-corrosion, abrasion proof, low energy
consumption, long service lifespan, easy maintenance and
operation,etc.
Working Process of ammonium sulphate fertilizer granulator
production line
Ammonium sulphate fertilizer granulator production line includes
crusher, mixer, granulator, dryer, cooler, screening machine,
packing machine,belt conveyor and other accessories,etc.
1.Vertical Chain Crusher
Put different raw materials into the vertical chain crusher. The
raw materials will be crushed into small particles, so that they
can meet the needs of the granulating process.
2.Disc Mixer
After crushing, they will be sent into the disc mixer, in which the
raw materials will be uniformly blended. The lining of the pan is
made of polypropylene or stainless steel sheet, which helps improve
the working efficiency as well as the production quality.
3.Granulator
The granulating process is the most important part of the whole
production line. Compound fertilizer production line mainly uses
double roller granulator and rotary drum granulator. You can tell
us your raw materials, our technicians will suggest you the best
granulator accordingly.
4.Rotary Drum Dryer
During the drying process, the water contents of granulated
particles will be dried, so that the particles will be harder and
easier to store. The whole body is sealed, in which the materials
will be contacted with the hot air with the continuous rotation of
the drum.
5.Rotary Drum Cooler
After the drying process, the temperature of the particles is a
little high, so they need to be cooled before the packing process.
The cooler adopts the most advanced cooling technology in the world
and makes the temperature of the particles is higher than the room
temperature for 3 to 5 degrees Celsius.
6.Rotary Drum Screening Machine
After entering the rotary drum screening machine, the qualified
particles will be sent into the coating machine, while the
unqualified particles will be selected and then sent into the
vertical chain crusher to be granulated again.
7.Rotary Fertilizer Coating Machine
The qualified particles will be coated by fertilizer coating
machine, which will beautify the particles and strengthen their
hardness at the same time. The fertilizer coating machine can
prevent the caking of the fertilizer particles effectively.
8.Fertilizer Packaging Machine
After the particles are coated, they will be packed by the packing
machine. The fertilizer packing machine is highly automatic, which
makes the packing process more efficient and accurate.
In addition to compound fertilizer production line, we also have
organic fertilizer production line.
Services of ammonium sulphate fertilizer granulator production line
Pre-sale Service
1.Offering overall technology and business consultation services;
2.Proposing the most suitable scheme and equipment for our
customer;
3.Designing and producting machine according to the special demands
of clients;
After-sales Service
1.Carefully checking machine in every working procedure, quality
comes first;
2.Assisting our clients for foundation construction of equipments;
3.Dispatching engineers to install and debug equipments,training
the first-line operators on site;
4.Regularly visit clients to solve production problems and
providing our technology support.