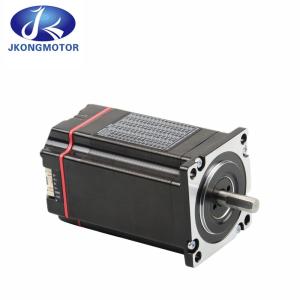

Add to Cart
Nema 17 23 Integrated Servo Stepper Motor 2N.m 3N.m 4A 5A 2-Phase Closed-Loop Stepper with CANopen/RS485 Communication
The ISM57 is a new Modbus-RTU, CANopen bus-integrated stepper motor that integrates RS-485 and CAN bus communication control technology. The stepping motor driver using standard Modbus-RTU bus protocol and CANopen bus communication protocol and DS402 control algorithm, compared with the traditional combination of stepper motor drive and stepper motor with lower cost and more convenient installation, but also can effectively avoid the problem of stepping motor lose step, and effectively restrain the motor temperature rise significantly to reduce the vibration of the motor, greatly enhance the performance of high speed motor. This integrated stepper motor integrates bus communication control technology, simple wiring, no losing step, lower heat, high speed, high torque, low cost and convenient maintenance. It is a cost-effective motion control product.
Features:
1. 57mm Hybrid Nema 23 Integrated Stepper Motor Genaral Specification:
Name | nema 23 integrated stepper motor |
Model | canopen integrated stepper motor for cnc |
Motor Type | canopen integrated stepper motor controller |
Rated Voltage | typical are 24V or 36V |
Holding Torque | 0.48N.m to 3N.m |
Body Length | nema 17 (47mm / 60mm); nema 23 (56mm / 80mm / 101mm) |
Current | 0.8A to 5A |
Shaft | D=8mm or 5mm |
Support Control | CANopen CiA402 / RS485 MODBUS |
Features | Nema 17 23 Integrated Servo Stepper Motor 2N.m 3N.m 4A 5A 2-Phase Closed-Loop Stepper with CANopen/RS485 Communication |
2,Features of integrated stepper motor controller driver:
1): A new generation of 32-bit DSP technology.
2): Support standard MODBUS-RTU protocol.
3): 4-way input function terminal, 2-way output function terminal.
4): The torque decay is reduced, and the speed can reach 3000rpm.
5): Built-in alarm output for easy monitoring and control.
6): Intelligently adjust current, reduce vibration, noise and heat, and increase efficiency by 35%.
7): Voltage range: DC24~50V.
8): 16 adjustable subdivisions, the default is 1000pulse/r.
9): Excellent high speed and rigidity, perfect integration of servo and stepper.
10): With overvoltage, undervoltage, overcurrent and other protection functions.
11): Integrated design with drive motor. Easy installation, small footprint and simple wiring.
3, Application of integrated drive stepper motor:
Printing, AOI, panel bonding, transfer equipment, etc. in PCB related equipment; camera related equipment such as camera and fingerprint; solid crystal machine, wire bonding machine, dispensing machine, beam splitter, and package tape machine in packaging.
4, General Specification of nema 23 integrated stepper motor:
Specification | ISM57-R Series | |||
Unit | Minimum | Typical | Maximum | |
Output current | A | 1.8 | - | 4 |
Input voltage | Vdc | 24 | 36 | 50 |
Rated input current | mA | 10 | 10 | 50 |
Rated input voltage | V | - | 24 | 24 |
Pulse frequency | kHz | 0 | - | 200 |
Insulation resistance | MΩ | 100 | - | - |
5,Techical Data:
Techical Data | ||||
Name | Unit | ISM57-R1x | ISM57-R2x | ISM57-R3x |
Phase | phase | 2 | 2 | 2 |
Step Angle | ° | 1.8 | 1.8 | 1.8 |
Rated Voltage | V(DC) | 24~50 | 24~50 | 24~50 |
Output Current | A | 4 | 5 | 5 |
Holding Torque | N.m | 1.2 | 2.2 | 3 |
Motor Length | mm | 56 | 80 | 101 |
Insulation Grade | - | B | B | B |
Operating Temperature | ℃ | 0~55 | 0~55 | 0~55 |
6,Terminal Description:
Terminal Description | |||
Pin | Function | Note | Interface Schematic |
PWR | Power indicator | Power on indicator | |
ALM | Alarm indicator | Alarm fishing indicator | |
X0-X3 | 4 input terminal | Input/Output terminal, signal power supply 24V, support NPN and PNP two wiring modes, support terminal function software modification | |
XCOM | Input common | ||
Y0-Y1 | 2 output terminal | ||
YCOM | Output common | ||
B- | RS485 communication interface 1 | 2 sets of RS485 communication interface, used for in and out connection, default baud rate is 115200, data format is: 8-bit data, no check digit, 1 stop bit. | |
A+ | |||
B- | RS485 communication interface 2 | ||
A+ | |||
+DC | Power input positive terminal | DC24~50V | |
GND | Power input negative terminal |
7,Input / Output terminal:
Input / Output terminal: | ||
Pin | Name | Function |
X0 | Input terminal | Input/Output terminal, signal power supply 24V, support NPN and PNP two wiring modes, support terminal function software modification |
X1 | ||
X2 | ||
X3 | ||
XCOM | Common input terminal | |
Y0 | Output terminal | Output terminal, the maximum driving current is 50mA, support terminal function software modificatio |
Y1 | ||
YCOM | Common output terminal |
8,DIP switch settings:
DIP switch settings: | ||
Pin | Sign | Function |
1 | SW1 | SW1: Terminal resistance |
2 | SW2 | SW2-5: Address setting |
3 | SW3 | |
4 | SW4 | |
5 | SW5 |
9,Power port setting:
Power port setting: | ||
Pin | Name | Function |
B- | Communication port | MODBUS Communication port |
A+ | ||
B- | ||
A+ | ||
GND | Power port | DC: 24V~ 50V |
+DC |
10,Alarm release:
Alarm release: | |||
Error code | Error information | ALM warning light | Resetting |
Err1: (0x01) | Overcurrent or phase-to-phase short circuit | Power-down reset | |
Err2: (0x02) | Power supply voltage is too high | Lock/Auto reset | |
Err3: (0x03) | Power supply voltage is too low | Lock/Auto reset | |
Err5: (0x05) | Out of torlance | Power-down reset |
11,Use environment:
Use environment: | ||
Cooling method | Heat sink cooling | |
Use environment: | Use environment | Keep away from other heating equipment as far as possible, avoid dust, oil mist, corrosive gas, strong vibration places, prohibit flammable gas and conductive dust |
Temperature | 0℃ ~ 50℃ | |
Humidity | 40 ~ 90 %RH (no condensation) | |
Shock | 10 ~ 55Hz/0.15mm | |
Storage temperature | -20℃ ~ +80℃ |
12,Product Dimensions: (Unit=mm)
13,Customized Design:
If this motor do not match with your request. Please feel free to contact with us,We can make customized shaft / winding / mounting flange / cable / connector / Encoder / Brake / Gearbox and others. We will works side-by-side with you and your team to design a motor that will fit the precise needs of your application. All Engineering and Support is done in-house.
14,Customized Shaft Types: