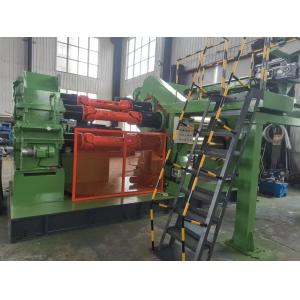

Add to Cart
PLC Control System Rubber roller calendering machinery for Efficient and Precise Processing
The rubber calender is a machine used in the production of various rubber products. Its main function is uniform thickness control of rubber materials. Here are some of the main features of the rubber calender:
Several rollers rotate to apply pressure to the rubber material, making it stretch and thin, which creates a uniform thickness. The type of roller configuration depends on the model of the rubber calender.
Rollers are the most crucial component of the rubber calender. They are typically made of high-quality steel, ensuring high hardness, strength, and good thermal conductivity, with high surface accuracy to guarantee excellent calendered products. The transmission system controls the speed of the rollers, providing different calendering speeds and speed ratios. Additionally, there is a reliable spacing device to adjust the calendering spacing of rubber materials of varying thicknesses.
The rubber calender can accurately control the thickness, width, and other dimensional parameters of rubber sheets or profiles, with the tolerance of thickness controlled within a small range of about ±0.02mm.
The majority of rubber calenders have roller heating or cooling functions. The temperature control system keeps the roller at a suitable working temperature, generally between 50℃ and 150℃, contributing to the plasticization and molding of rubber.
The rubber calender has high production efficiency and can operate continuously, calendering a large amount of rubber raw materials into required specifications. The output of the machine varies based on the model and process - small ones could be several tons per hour, while large industrial ones can go as high as tens of tons. Rubber calender is widely used in the production of various rubber products, such as tires, conveyor belts, rubber sheets, seals, and many more.
With the rubber calender, you can be sure of quality and efficient production. It is a reliable machine with a broad range of application in the rubber processing industry.
Item | XY-2I()320 | XY-2I()620 | XY-2I()1120A | XY-2I()1500 | XY-2I()1830 | XY-2I()1730 | XY-2I()2430 |
---|---|---|---|---|---|---|---|
Roll diameter (mm) | 160 | 250 | 360 | 450 | 550 | 610 | 810 |
Roll working length (mm) | 320 | 620 | 1120 | 1500 | 1830 | 1730 | 2430 |
Roll ratio | 1:1 | 1:1 | 1:1 | 1:1 | 1:1.08 | 1:1 | 1:1 |
Roll linear speed (r/min) | 7.79 | 14.8 | 3-20.2 | 2.5-24.8 | 2-18.7 | 4-36 | 2-20 |
Adjusting nip range | 0-4.5 | 0-5.5 | 0-10 | 0-10 | 0-12 | 0-15 | 0.5-25 |
Min.calendering product thickness (mm) | 0.2 | 0.2 | 0.2 | 0.2 | 0.2 | 0.2 | 0.5 |
Calendering product width (mm) | 250 | 580 | 920 | 1250 | 1600 | 1500 | 2150 |
Motor power (kW) | 5.5 | 15 | 37 | 45 | 75 | 90 | 160 |
Overall dimensions L x W x H (mm) | 2200 x 530 x 1470 | 3100 x 770 x 1590 | 5400 x 1542 x 1681 | 7113 x 1595 x 2446 | 7420 x 1760 x 2760 | 5987 x 1860 x 2988 | 8690 x 3139 x 4270 |
Weight (t) | ~1.2 | ~3 | ~14.5 | ~22 | ~24 | ~30 | ~62 |
The operation process of rubber calender is an important step in rubber production. Proper preparation and operation can improve production efficiency and ensure product quality. Below is the step-by-step process:
Before starting the calender, several preparations are needed. First, equipment inspection should be done. Check all components of the machine, including rollers, transmission systems, spacing devices, temperature control systems, etc. to ensure all components are firmly connected and without any looseness or damage. Check for smooth and clean surfaces of the rollers. Clean and repair rollers if necessary. Second, prepare the rubber raw materials to be calendered. Ensure the accuracy of the formula and that the mixing is uniform. Third, set the control system parameters, such as the roller speed, roller spacing, and working temperature.
After completion of the preparation stage, the machine can be started. First, start the transmission system to slowly rotate the roller. Observe for any abnormalities, such as abnormal sounds or vibrations and troubleshoot if necessary. Next, preheat the roller to the appropriate processing temperature range, generally between 50℃ - 150℃, depending on the type of rubber and process.
During the calendering process, the rubber raw materials are fed into the machine slowly and evenly through the feed port. The speed should be moderate to avoid accumulation on the rollers or affect production efficiency. If adjustments to the thickness or width are needed, the spacing device can be used. Pay close attention to the flow of rubber between the rollers and monitor for smoothness and flatness. Continuously check the product quality, including appearance and dimensional accuracy. Take corrective measures if there are any quality problems.
The shutdown operation includes several processes. First, stop feeding the rollers. Allow the machine to calender any remaining rubber between the rollers until all rollers are cleared. Second, cool down the roller gradually by turning off the heating function and turning on the cooling function if necessary. Third, stop the transmission system. Finally, clean the machine thoroughly.
Beishun is pleased to offer customizable options for our rubber calender machine. Our machines are available in three different models: 4-roller, 3-roller, and 4-roller. All of our machines are manufactured in our factory located in QINGDAO, CHINA and come with CE, ISO, and SGS certifications. The minimum order quantity for our machines is 1pcs, and the price ranges from 10000usd-150000usd.
Our delivery time for these machines is 45 days, and we accept payment via L/C or T/T. We are capable of supplying up to 50 sets per year, and our machines can be customized to have roller widths ranging from 500mm to 2000mm and roller diameters ranging from 200mm to 400mm. The control system of our machines is PLC, and they run on electric power.
Our rubber calender machines are perfect for producing inner tube calenders and are a key piece of continuous rubber calendering machine for any rubber production line equipment.
Product Packaging:
Shipping:
Q1: What is the brand name of the calender machine?
A1: The brand name of the calender machine is Beishun.
Q2: What is the model number of the calender machine?
A2: The calender machine is available in 4-roller, 3-roller, and 4-roller models.
Q3: Where is the calender machine made?
A3: The calender machine is made in QINGDAO, CHINA.
Q4: What certifications does the calender machine have?
A4: The calender machine has the following certifications: CE, ISO, SGS.
Q5: What are the payment terms for purchasing the calender machine?
A5: The payment terms for purchasing the calender machine are L/C and T/T.