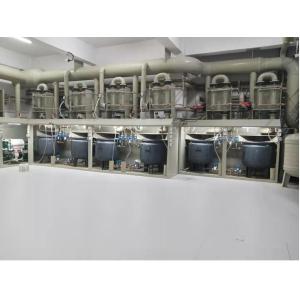

Add to Cart
extracting machine to get platinum, palladium and rhodium from automobile exhaust catalyst
It has a group of experienced senior management talents, efficient technical team and highly skilled installation team, which can provide the owner with the whole process technical services of design, non-standard equipment production, installation and commissioning and operation training. The company has successfully completed the construction project of gold and silver refining workshop for hundreds of enterprises in the industry, serving hundreds of large state-owned enterprises and listed companies. Among the 36 gold smelting enterprises that have obtained the qualification of "providing standard gold ingots" from Shanghai gold exchange, 20 adopt our technology and equipment, reflecting the high technical level and good service quality of the company
Introduction of platinum, palladium and rhodium recovery and
extracting production machine from automobile exhaust catalyst
Due to the lack of domestic platinum group mineral resources and
the imbalance between supply and demand, in order to meet domestic
demand, most of China's platinum group metals come from the
recovery of platinum group metal containing wastes, such as
platinum palladium catalyst in petrochemical industry, automobile
exhaust catalyst, etc. Different raw materials require different
treatment processes. The company designs processes and equipment
according to different raw materials to meet production needs.
In September 2021, the project of clean and efficient separation
and refining technology and equipment of short process platinum,
palladium and rhodium jointly developed by the company in Northeast
University was recognized by academicians and recognized as the
international advanced level by China Nonferrous Metals Industry
Association.
Features of platinum, palladium and rhodium recovery and refining
production line:
The company's platinum, palladium and rhodium recovery and refining
production line can be designed according to the owner's raw
materials and operation habits. It can refine and separate
platinum, palladium and rhodium materials with a content of more
than 5%, and the content of each finished product can reach more
than 99.95%.
High recovery of platinum, palladium and rhodium
In the recovery process of platinum palladium rhodium waste
catalyst, there are some processes to oxidize a small number of
palladium to form palladium oxide which is difficult to dissolve in
acid and alkali. The dissolution rate is very low by direct use of
aqua regia or chlorination. In addition, the stability and
extremely difficult solubility of rhodium, iridium and ruthenium
also cause the low recovery rate of rhodium, iridium and ruthenium.
We design a pretreatment process for this material, which can
effectively improve its dissolution rate and then improve the
recovery of precious metals.
Continuous operation of production line
The company's platinum, palladium and rhodium recovery production
line has the following advantages: first, design glass high-level
tanks, reduce staff handling and increase production capacity. The
traditional PP high-level tank is not suitable for cleaning, which
is easy to be dirty and inconvenient to observe the liquid level,
resulting in unqualified product quality and large production
occupation; The designed glass high-level storage tank well meets
the production requirements. The glass material is transparent and
easy to clean. 2, In order to facilitate the use and operation of
the supporting glass high-level tank, the design of the traditional
suction filter bottle is improved and changed to a horizontal
filter. After the filtration of the horizontal filter is completed,
the liquid guide pipe is connected below and directly enters the
glass high-level tank. The horizontal filter has a slight 3O
inclination angle to facilitate the vacuum extraction of a small
amount of solution. This makes the production process more coherent
and smooth and doubles the production capacity.
Reasonable exhaust design
The traditional refining of platinum, palladium and rhodium is
carried out in the air cabinet. The exhaust pipe of the air cabinet
is normally open. The overall design air volume design requirements
are large. Excessive air pressure leads to the volatilization of
precious metals with steam, and the loss rate of precious metals is
high. The complete set of platinum, palladium and rhodium refining
air cabinet is sealed at the mouth of the reaction vessel, and a
gas-liquid separation and condensation device is added in the non
temperature reaction vessel to condense water vapor, so that the
waste gas can directly enter the corresponding treatment pipeline.
For example, in the aqua regia dissolution process, the flue gas
hood seals the reaction vessel. After the reaction waste gas is
condensed and separated by gas-liquid, the condensate containing
precious metals returns to the reaction vessel. The nitrogen oxide
waste gas directly enters the jet tower for treatment, so as to
reduce the diffusion of waste gas and maintain a good workshop
environment.
In the production and refining process, from aqua regia to finished
products, all precious metal filters and storage tanks are made of
glass, transparent and visible. A spray washing system is attached
to reduce the occupation of precious metals in the equipment.
Mature waste gas treatment process
The company is equipped with mature precious metal refining waste
gas treatment process and multi-stage jet jet high concentration
NOx waste gas treatment device, including gas-liquid separator, no
oxidation tank, jet jet jet tower, etc. after the treatment of high
concentration NOx flue gas (~ 30000 mg / m3) produced by platinum,
palladium and rhodium dissolution, the emission concentration is
less than 100 mg / m3 and the minimum can be less than 20 mg / m3.