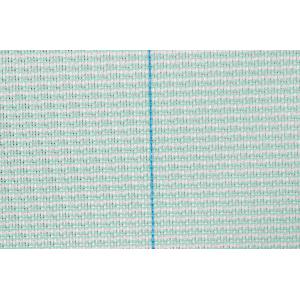

Add to Cart
Polyester Forming Wire / Paper Machine Cloth / SSB Paper Making Wire / Dryer Screen For Paper Making Industry
What is Forming wire?
The forming wire of paper machine clothing (PMC) are playing a crucial role to dewater the pulp and form the paper sheet, support the sheet as it formed and carry to the next pressing section during the paper production. It’s composed of one or two endless fabric loops. |
A properly designed constructed and maintained forming wire will help the former produce a sheet that meets end-products specification at an acceptable production rate. In addition to excellent fiber support, efficient dewatering property, make the smooth surface of the sheet, the forming wire also has good running stability and abrasion-resistant capacity. |
Forming Wire Category
Forming wire for the paper machine are made by weaving together yarns oriented in the machine direction (MD) and cross-machine direction (CD). There are many different weave patterns but they can be grouped into four general categories or styles based on the number of CD yarn layers.
Single-layer, one set of CD yarns woven together with one set of MD yarns. |
Double-layers, two sets of CD yarns stacked on top of each other woven together with one set of MD yarns, to enhance the abrasion resistance property and fiber support. |
Two and a half layers – The double-layer forming fabrics has a flaw of the poor balance of the dehydration efficiency and fiber support, so two-layer and half come out. Additional CD yarns typically smaller in diameter added to the top layer of a double layer fabric to provide better fiber support, also expands the space and enhances the dehydration ability and service life. |
Triple-layer forming wire has congenital insufficiency. First, the upper layer and the bottom layer are easily dislocated due to the force or damage of the connecting line or even “divided” and scrapped. Second, the bonding line has a negative effect on both forming and dehydration. In order to overcome these shortcomings, we have the self-supported binder (SSB) forming wire. The SSB structure utilizes the upper weft yarn to combine the bottom layer directly, without the additional binding yarns, which comprehensively maintains the advantages while overcoming the deficiencies of the three-layer wire. |
Forming Wire Monofilament Yarn Material
To avoid the blemish on the paper sheet, the most important
requirement of monofilament is uniformity diameter over the entire
length of the yarn.
High tenacity polyester (PET) monofilament yarns are used in the
warp (MD) to provide the required high tension of the forming
fabrics, and the diameter of MD yarn usually between 0.12 to 0.30
mm.
The monofilament yarn in the weft (CD) of the paper side is usually
100% polyester in high density to get better fiber support, while
the mechanical (bottom) layer is composed of 50% polyester and 50%
nylon in thicker diameter to ensure better wear resistance
property. Nylon monofilament provides good abrasion resistance, but
it’s not stable in hydrolyzed as PET under humidity conditions, so
it will not exceed 50% typically. The diameter of the weft (CD)
yarn is usually between 0.11 and 0.45 mm.
Main Property of Forming Wire
A properly designed constructed and maintained forming fabrics will help the former produce a sheet that meets end-products specifications at an acceptable production rate. The variables design and construction of paper machine forming fabrics influence overall sheet quality. |
The main property of Forming fabrics is as follows:
1). Dehydrate property, expressed parameter by air permeability and Drainage Index (DI). The pulp concentration is roughly 0.4%~1%, that is, more than 99% of the pulp is water, and about 96% of the water is dewatered in the forming section. The forming fabric has to dehydrate a huge volume of water in a short span of time.
2). Fiber support capacity: expressed by the Coefficient of Fiber
Support(FSI). Good forming fabrics not only need to drain the water
rapidly but also have to support the fibers on the surface to form
a sheet. Good fiber support of the forming fabric improves the
sheet characteristics such as flatness, smoothness, printability
and strength properties, also avoids fiber embedding or clogging of
the forming fabric, reduce the loss of fine fibers and fillers.
3). Mechanical property: The mechanical property of a forming
fabric includes:
a) The transmission ability to transfer the sheet to the press
section on the paper machine, and the ability to guide and drive
the forming fabric itself.
b) Stability in lateral to ensure good sheet flatness of the side
part, and stability in longitudinal to enhance efficiency and
running property.
c) Good stiffness which will increase the transfer capacity of the
paper machine and efficiency.
d) Excellent wear resistance make the forming fabric to be long
service life.
Features of Huading's Paper Machine Wire
The running property of the forming wire and the quality of the
formed sheet depend on the retention rate and forming of the fiber.
Huading's Forming wire has the features of below:
1). Good and properly designed woven structure, excellent drainage
efficiency and fiber support, easy clean and maintain.
2). Made out by the top quality of raw material, which has even
yarn diameter, good strength and wear resistance property and
longer service lifetime.
3). Woven by Texo looms to achieve a highly precise and smooth
surface.
4). Max. width 13.5M.
5). Huading have a complete portfolio of the paper machine
clothing, the single to triple layer of forming fabrics.
6). Endless seam by automatic seaming machine, no-marking and has
nearly the same property as the fabric surface.
7). Heat setting by Juergens oil roller heat setting machine to
anti-deforming and better dimensional stability, low elongation,
smooth running performance.
8). The formed sheet has a non-marking surface, high acceptable
rate.