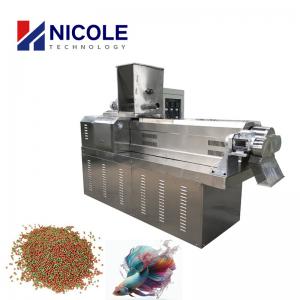

Add to Cart
Popular CE Certified Multifunctional Automatic Fish Floating Feed
Machine From Chinese Factory
Product Description:
The Popular CE Certified Multifunctional Automatic Fish Floating
Feed Machine From Chinese Factory uses grains with high puffing
degree, such as powdered corn flour etc., as the basic raw
materials, supplemented by various nutritional elements such as
bone meal, meat meal, protein, vitamins, fibers, etc. Instantaneous
puffing to produce fish feed granules with different shapes, high
puffing degree and high floating performance. After drying, the
surface of fish feed is sprayed with seasoning to enhance the
taste, and then cool and package the fish feed. That is a complete
set of automatic fish feed production line.
The production equipment can adjust the raw materials, temperature,
moisture and other process parameters, so that the product has the
characteristics of novel shape, unique taste, rich nutrition and
delicate organization, which is suitable for the taste of different
pets. This production line is widely used in the production of dog,
cat, fish and shrimp, fox, bird and various pet feeds.
Flow Chart:
Mixer: Mix raw materials together.
Screw Conveyor: Convey the mixed raw materials to the feeder of
extruder.
Twin Screw Extruder: Puff and extrude the raw materials into target
shapes by double screws and moulds.
Air Conveyor: Blow the products to the multi-layer dryer, and
dehumity during conveying.
Dryer: The multi-layer dryer can dry the products to target
moisture contents with energy source: electric, gas or steam.
Hoister: Convey the dried products to the flavoring part.
Oil Sprayer: Spray the oil on the surface of the dried products, so
that the products can be flavored well.
Flavoring Roller: Flavoring the products with yummy seasonings.
Cooling Machine: Cool the final products and convey the products to
the packing workshop.
Main Systems of Extruder:
1. Feeding system
Installed on the body box, feeding by screw. The feeding amount is
adjustable. The system is composed of speed-regulating motor,
screw, silo, stirring fin, rack and so on. The function of the
stirring fin is to prevent the material from being "overhead" in
the barrel, and the feeding speed should be such that there is no
material accumulation at the inlet of the barrel.
2. Extrusion system
This system adopts the "low temperature curing" process that makes
the material mature at a lower temperature through kneading,
mixing, shearing and extrusion for a certain period of time. There
are strict temperature controls on the barrel and screw of the
equipment, so that the product can be produced stably. The ratio of
raw materials is adjusted according to the shape of the selected
product, so that it is easy to discharge and easy to form without
sticking to the knife.
3. Rotary cutting device
The rotary cutting device is composed of a motor, a knife holder, a
cutter, a transmission part, etc. The knife holder is fixed on the
mold, and the motor drives the knife holder to rotate and cut off
the material through the belt. The rotational speed of the rotary
cutter should be based on the type of product (length, shape )
depends.
4. Heating system
The heating system is divided into three zones, and the heating
temperature of each zone can be adjusted independently.
5. Transmission system
The power starts from the main motor, and is transmitted to the
screw through the V-belt pulley and the reducer. The speed control
system of this machine adopts frequency conversion speed control
technology, which is reliable in adjustment, wide in adjustment
range and stable in operation.
6. Control system
The control system can centrally control all the components of the
main engine, which is easy to operate and reliable in control, and
is equipped with various automatic protection devices and status
indicating instruments.
Machine Details:
Various Final Products:
Technical Parameter:
Model | NT - 65 | NT - 70 | NT - 85 |
Installed Power | 76kw | 95kw | 178kw |
Power Consumption | 54kw | 66kw | 125kw |
Production Capacity | 150kg/h | 250kg/h | 500kg/h |
Dimension (LxWxH) | 17x2x2.5m | 22x2x2.5m | 26x2x3.5m |
Company Information:
Our main products are puffed snacks production line, pet food
production line, fried pellets production line, pasta macaroni
production line, and various industrial drying equipments. These
products are designed to meet the demands of modern food processing
plants, delivering consistent and reliable production results.
Our commitment to quality and customer satisfaction has enabled us
to establish long-term partnerships with numerous clients across
the world. We strive to provide the best solutions for our clients,
from product design and manufacturing to installation, training,
and after-sales service.
Certifications:
Service:
Pre-sales: Free consulting services; factory layout and craft
suggestions;
During-sales: Reports for production, inspection, loading etc.
After-sales: Online guidance for installation, training,
maintenance and personal operation or overseas service.
Packing & Shipping:
Inner with plastic film, outside with wooden case or pellet or
according to customsers' requirements.
FAQ:
1. Can you supply OEM or ODM?
Answer: Yes, we do. We can manufacture the machines according to
your exact requirements.
2. How will you pack and delivery the machine to me?
Answer: Inner with plastic film, outside with wooden case or pellet
or according to customsers' requirements.
3. What is your delivery time?
Answer: Generally the delivery time is 7 - 15 days after down
payment receiving. But the exact delivery time will depend on your
quantity and your ordering time.
4. Can you also supply me related machines together?
Answer: Yes, we can. We have been in this field for many years and
we can supply connect machines, feeding machines, packing machines
etc. If you purchase other goods, you can also send your other
goods to our factory for loading together.
Any interests, contact me for more details directly, please!