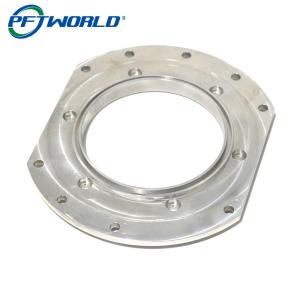

Add to Cart
High precision CNC aluminum parts, machined disc stainless steel
parts
Quick Details:
1. Keywords: CNC steel
2. Process: CNC processing
3. Color: according to your requirements
4. Origin: Guangdong, China
5. Use: automobile parts, metal tubes
6. Drawing format: 2D/(PDF/CAD) 3D (IGES/STEP)
7. Equipment: CNC machining center
8. Delivery period: 1-2 weeks
The Principle of Thread Machining in CNC Lathe
There is a big difference between CNC thread turning and ordinary
lathe thread turning. The ordinary lathe is linked with the lead
screw through mechanical transmission of gears and then turns. That
is, every time the spindle rotates, the tool carrier moves a lead
of the thread. During the whole thread processing process, this
drive chain cannot be disconnected, or it will be disorderly
screwed.
For NC turning, the encoder installed on the spindle sends pulse
signals to enter the NC system. There is a NC system for
calculation control. The command is sent to control the servo motor
to control the tool movement through the ball screw to achieve
thread turning. In order to prevent thread turning from being
disorderly in multiple tool paths, the pulse signal is detected to
control the initial processing position of the thread. When the
program processing starts, the spindle rotates, After the tool
waits for the spindle encoder to send a synchronization signal
(zero position signal), it will perform turning. When turning the
second tool thread, the tool will return to the starting point of
the last turning, or wait for receiving the synchronization signal
(zero position signal), and then turn again. In this way, the
turning thread is always on the same helix, so there will be no
random thread.
Problems in Tool Setting for Thread Turning
1) First turning clamping tool
When the screw tool is clamped for the first time, the unequal
height between the tip of the screw tool and the rotation center of
the workpiece will occur, which is commonly seen in the welding
tool. Due to rough manufacturing and inaccurate cutter bar size,
the center height needs to be adjusted with shims. The height of
the center affects the actual geometric angle of the tool after
turning. When installing the cutter, the cutter tip angle is
biased, which is easy to cause the error of thread profile angle
and the skew of tooth profile. If the thread cutter extends too
long, it will vibrate the cutter during processing, which will
affect the surface roughness of the thread.
2) Rough and fine turning tool setting
In the process of machining high-precision thread and trapezoidal
thread, it is necessary to use two thread cutters for rough and
fine turning to separate them, and the large offset (especially in
Z direction) of the two cutters for tool setting will make the
pitch diameter of the thread larger and cause scrapping.
3) Repair workpiece tool setting
Tool setting of repair work-piece As the work-piece is clamped for
the second time, the repaired spiral line and the encoder's first
rotation signal have changed, which will lead to disorderly thread
during repair processing again.
Specification:
Material | Steel |
Application | Auto Part, Metal Pipe |
Color | As your requirement |
Package | Carton Box |
Surface treatment | As your requirement |
Drawing format | 2D/(PDF/CAD),3D(IGES/STEP) |
Certificates | ISO9001:2015/ISO13485:2016 |
Lead time | 1-2 weeks |
FAQ:
1. Where is your factory?
We are a 3000 square meter factory located in Shenzhen, China.
2. Can you invite on site?
We welcome our new and old friends to visit here.
3. How can I get the best quality at the best price?
Our prices are very competitive. Generally, the price depends on
the quantity, design and size. If you order more, the price and
freight will be cheaper.
4. Can I get a quotation without drawings?
Of course, we are glad to receive your samples, pictures or drafts
with detailed dimensions for accurate quotation.
5. If you benefit, will my drawings be disclosed?
No, we pay great attention to protecting the privacy of customers'
drawings. If necessary, we can also sign NDA.