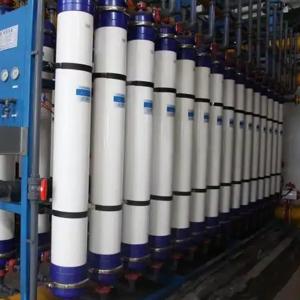

Add to Cart
The core principle of the ultrafiltration device is to use asymmetric microporous structure and semipermeable membrane media, and use the pressure difference on both sides of the membrane as a driving force to perform cross-flow filtration, so that solvents and small molecules pass through the membrane pores, while large molecules are retained.
Definition and Principle:
Ultrafiltration (UF) equipment is a membrane separation device
driven by pressure difference. Its core is the ultrafiltration
membrane, which has an asymmetric microporous structure and can
intercept substances with a large relative molecular mass. In the
ultrafiltration process, when a solution containing impurities
passes through the ultrafiltration membrane under a certain
pressure, the membrane allows water and small molecular solutes
(such as inorganic salts, small molecular organic matter, etc.) to
pass through, while retaining large molecular substances (such as
proteins, colloids, bacteria, viruses, etc.) on one side of the
membrane, thereby achieving the purification, separation and
concentration of the solution.
For example, in water treatment, when raw water passes through the ultrafiltration membrane, suspended matter, large molecular organic matter, etc. in the water are retained on the membrane surface, while small molecular substances such as water molecules and dissolved salts pass through the membrane to achieve the purpose of purifying water quality. The separation principle of ultrafiltration is mainly based on screening, that is, the pore size of the membrane determines the substances that can pass through. However, in addition to the screening effect, the interaction between the membrane surface and the solute (such as adsorption, charge repulsion, etc.) also has a certain influence on the separation effect.
Main components:
Ultrafiltration membrane assembly:
Hollow fiber membrane assembly:
This is the most common form. It consists of a large number of
hollow fiber membrane filaments, the outer diameter of which is
generally between 0.5 and 2.0 mm, and the inner diameter is between
0.2 and 1.0 mm. Water enters from the outside of the membrane
filament. Under pressure, small molecules pass through the membrane
wall and enter the inside of the membrane filament, while large
molecules are retained on the outside of the membrane filament.
This assembly has a high membrane packing density and can provide a
large membrane area per unit volume, thereby improving the
filtration efficiency.
Rolled membrane assembly:
The ultrafiltration membrane, guide net and central tube are wound
together. During operation, the incoming water flows along one side
of the membrane under pressure, and the liquid that passes through
the membrane is collected in the central tube through the guide
net, and the retained substances remain on the other side of the
membrane. The advantage of the rolled membrane assembly is that it
has a compact structure and is suitable for treating some
relatively clean liquids.
Casing and support structure:
It is used to protect the ultrafiltration membrane assembly and
provide it with necessary support. The shell is usually made of
materials such as stainless steel, fiberglass or engineering
plastics, which have good corrosion resistance and mechanical
strength and can withstand a certain amount of pressure. The design
of the shell should take into account the uniform distribution of
inlet and outlet water to ensure that all parts of the membrane
assembly can fully function.
Pump system:
Feed pump:
transports the raw water to be treated to the ultrafiltration
equipment. The feed pump needs to select the appropriate type and
specification according to the properties of the raw water (such as
viscosity, solid content, etc.) and the treatment scale. Generally
speaking, the feed pump should be able to provide sufficient
pressure to overcome the resistance of the ultrafiltration membrane
so that the raw water can pass through the membrane assembly
smoothly.
Circulation pump (some equipment has):
In some ultrafiltration systems, in order to improve the filtration
efficiency and the service life of the membrane, a circulation pump
will be set. The circulation pump returns part of the concentrated
water that has not passed through the membrane to the feed port,
mixes it with the newly entered raw water, and then ultrafilters it
again, which can increase the flow rate on the membrane surface and
reduce the occurrence of membrane pollution.
Valve and piping system:
Used to control the flow direction, flow rate and pressure of the
liquid. Valves include water inlet valves, water outlet valves,
concentrated water discharge valves, etc. By reasonably adjusting
the opening of the valves, the operating parameters of the
ultrafiltration process can be controlled. The pipeline system must
ensure the smooth transportation of liquid inside the equipment,
and suitable pipes must be selected to prevent corrosion and
leakage. Pipes are usually made of stainless steel pipes, UPVC
pipes (rigid polyvinyl chloride pipes) or PE pipes (polyethylene
pipes).
Cleaning system:
Since the ultrafiltration membrane will inevitably be contaminated
during use, a cleaning system is essential. The cleaning system
includes chemical cleaning devices and physical cleaning devices.
Chemical cleaning is to remove dirt (such as organic matter,
inorganic matter, microorganisms, etc.) on the membrane surface by
injecting specific chemical cleaning agents (such as acids,
alkalis, oxidants, surfactants, etc.) into the membrane assembly.
Physical cleaning includes water washing, backwashing and sponge
ball scrubbing to remove loose dirt on the membrane surface.
Workflow:
Pretreatment:
Before ultrafiltration, raw water usually needs to be pretreated,
such as filtration, sedimentation, etc., to remove larger
particulate impurities and suspended solids to prevent these
substances from clogging the ultrafiltration membrane. The
pretreated water enters the feed port of the ultrafiltration
equipment.
Ultrafiltration process:
The feed pump delivers the pretreated water to the ultrafiltration
membrane assembly. Under pressure, water passes through the
ultrafiltration membrane, and small molecules (such as dissolved
salts, small molecular organic matter, etc.) and water pass through
the membrane together to form a permeate (also called produced
water), while large molecules (such as proteins, colloids,
bacteria, etc.) are retained on one side of the membrane to form
concentrated water. The permeate can be output as product water
after being collected through the pipeline, and the concentrated
water is discharged or further processed according to the specific
situation.
Cleaning and maintenance:
As the ultrafiltration process proceeds, the flux of the
ultrafiltration membrane will gradually decrease, which is due to
the contamination of the membrane surface. When the membrane flux
drops to a certain extent, the ultrafiltration membrane needs to be
cleaned. The cleaning process includes first rinsing with clean
water to remove loose dirt on the membrane surface, and then
selecting a suitable chemical cleaning agent for chemical cleaning
according to the type of pollution. After cleaning, the
ultrafiltration equipment can restore good filtration performance.
Performance characteristics:
High separation accuracy:
It can effectively intercept substances with a relative molecular
mass greater than the membrane cut-off molecular weight, and the
molecular weight cut-off range is generally between 1000-1000000Da.
For example, for proteins with a relative molecular mass greater
than 100000Da, the ultrafiltration equipment can intercept most of
them on one side of the membrane, thereby achieving the separation
of macromolecular substances in the solution.
Large filtration flux:
Under appropriate pressure and temperature conditions, the
filtration flux of ultrafiltration equipment is relatively high.
The flux is generally between 30-300L/(m²・h), which means that more
liquid can be processed per unit time. However, the flux will be
affected by many factors, such as the material of the membrane, the
quality of the inlet water, the operating pressure and temperature,
etc.
Strong anti-pollution ability:
Compared with some other membrane separation equipment, the
anti-pollution ability of ultrafiltration equipment is relatively
good. This is because the surface of the ultrafiltration membrane
is relatively smooth, and some ultrafiltration membranes also have
anti-pollution coatings or modified structures, which can reduce
the adhesion of dirt on the membrane surface. At the same time,
through reasonable operation (such as controlling the quality of
the inlet water, appropriate flow rate, etc.) and regular cleaning,
the anti-pollution ability of the equipment can be further
improved.
Simple equipment and easy operation:
The structure of the ultrafiltration equipment is relatively
simple, mainly composed of membrane components, pumps, valves and
pipes. The equipment has a high degree of automation, and the
control of the feeding, filtration, cleaning and other processes
can be achieved through the automatic control system. The operator
only needs to perform simple parameter settings and monitoring to
ensure the normal operation of the equipment.
Wide range of applications:
It can be used in water treatment, food processing,
pharmaceuticals, chemicals and other fields. In the field of water
treatment, it is used for the purification of drinking water,
pretreatment of industrial wastewater, etc.; in food processing, it
is used for the clarification and sterilization of juice, milk,
etc.; in the pharmaceutical industry, it is used for the refining
and sterilization of drug extracts, etc.
Application field:
Water treatment field:
Drinking water purification:
As a means of deep treatment of drinking water, it can effectively
remove impurities such as bacteria, viruses, colloids, and
macromolecular organic matter in water, and improve the quality and
safety of drinking water. For example, in some small water supply
systems in rural areas, ultrafiltration equipment can treat
groundwater or surface water, remove pollutants, and make the water
quality meet the drinking water standard.
Industrial wastewater pretreatment:
For industrial wastewater containing macromolecular organic matter, colloids, suspended solids, etc., ultrafiltration equipment can be used as a pretreatment unit to remove these impurities and reduce the load of subsequent treatment units (such as reverse osmosis, biochemical treatment, etc.). For example, in the treatment of printing and dyeing wastewater, ultrafiltration equipment can remove dye macromolecules and fiber impurities in wastewater, creating good conditions for subsequent biological treatment or deep treatment.
Food industry:
Juice clarification and sterilization:
During the juice processing process, ultrafiltration equipment can
remove impurities such as pectin, protein, bacteria, etc. in the
juice, making the juice clear and transparent, while extending the
shelf life of the juice. For example, in apple juice processing,
after ultrafiltration treatment, the turbidity of the juice can be
significantly reduced, and the flavor and nutrients of the juice
can be retained.
Milk sterilization and concentration:
used for sterilization and partial concentration of milk.
Ultrafiltration can remove bacteria, somatic cells and other
impurities in milk, while retaining nutrients such as protein and
lactose in milk. When producing dairy products such as cheese,
ultrafiltration equipment can also be used for pre-concentration of
milk to improve production efficiency.
Pharmaceutical industry:
Drug extract refining:
During the drug extraction process, ultrafiltration equipment can
remove macromolecular impurities (such as polysaccharides,
proteins, etc.) in the extract to improve the purity of the drug.
For example, in the refining process of Chinese medicine extracts,
ultrafiltration can effectively separate the active ingredients of
the drug from impurities and improve the quality of Chinese
medicine preparations.
Injection sterilization filtration:
As a sterilization filtration link in the production process of injections, ultrafiltration equipment can effectively remove pathogens such as bacteria and viruses to ensure the sterility of injections. Compared with traditional sterilization filtration methods, ultrafiltration has higher safety and reliability.