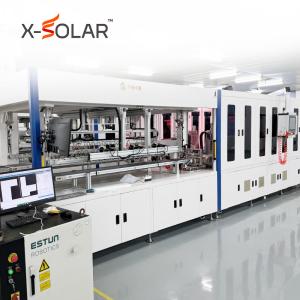

Add to Cart
Multi-Busbar PV String Welding Machine
It is an automated production equipment capable of string welding PV crystalline silicon solar cells, characterized by high production capacity, high precision, and high compatibility.
Product parameter | Data |
Capacity | 6800 half pcs/hour |
Welding Manner | Infrared Welding |
Cell Size | 166-210 mm |
No. of Main Busbars | Main Busbar Compatibility:10-20BB |
Solder Wire Specifications | Round, Irregular Shape, Flat Ribbon |
Air Consumption | ≥3200L/min |
Power | Average Power: 37W Peak Power 45 kW |
Weight | 13,500kg |
Dimensions of the Equipment | 10,800*2,400*2,650 (L*W*H) |
Beijing X-Solar Energy Co., Ltd. was found in 2020, and
headquartered in Beijing. It's a science and technology innovative
energy enterprises with the main business of future cell R&D,
flexible photovoltaic modules, building photovoltaic module
production, high-end equipment manufacturing, production line
delivery, and AI-CITY wisdom energy management services.
In July 2023, the company's first demonstration factory, Jiangsu
X-Solar Green-building Technology Co., Ltd., was established in
Jiangyin CNBM Jetion Industrial Park. Meanwhile, Jiangsu YuanTeng
FengSheng Intelligent Manufacturing Technology Co., Ltd., a
wholly-owned equipment company of the company, delivered the
world's first "three-in-one" automatic production line for Jiangyin
base. The production line can be compatible with the production of
three categories: X-Solar Light shadow series (flexible PV
modules), X-Solar Light rhyme series (building PVtile modules),
X-Solar Light Curtain series (building PV wall modules), and
customized products. X-Solar PV series products have the advantages
of integrating architectural aesthetics, complying with design
specifications and creating energy value, which have been widely
recognized and praised by customers in domestic and overseas.
In 2024, the company has added two regional centers in Shanghai and
Guangzhou of China, and set up the Hong Kong X-Solar Future Energy
Research Institute, and overseas sales companies in Australia,
Italy, Germany, Saudi Arabia and Argentina. The company has
launched a global layout to provide sustainable energy products and
services to many countries, and has contributed to the "carbon
neutrality and carbon peak".
Related to the basic principle of the equipment
1. Question: What is the working principle of the multi-busbar
photovoltaic string welder?
Answer: It mainly realizes the series connection of battery cells
by precisely positioning the photovoltaic battery cells with
multiple busbars through high-precision mechanical transmission
cooperating with the welding system, and then using appropriate
welding processes (such as infrared welding, laser welding, etc.)
to weld the busbars onto the main grid lines of the battery cells.
2. Question: What are the advantages of adopting the multi-busbar
technology compared with the traditional one?
Answer: The multi-busbar can reduce the current transmission
distance on the surface of the battery cell, decrease the
resistance loss, improve the photoelectric conversion efficiency of
the battery cell, and then increase the power output of the module.
Related to the welding process
1. Question: What are the commonly used welding methods and what
are their characteristics?
Answer: Commonly used ones include infrared welding, which features
uniform heating and relatively fast welding speed; laser welding
has high precision and good welding strength, but the equipment
cost is relatively high. Different processes are suitable for
different production requirement scenarios.
2. Question: How to ensure the stability of welding quality?
Answer: It is necessary to precisely control parameters such as
welding temperature, pressure, and welding time, regularly
calibrate the welding equipment, and at the same time ensure that
the surfaces of the battery cells and busbars are clean and flat,
and the materials are of qualified quality.
Related to the equipment operation
1. Question: What preparatory work needs to be done before starting
the equipment?
Answer: It is necessary to check whether the connections of all
parts of the equipment are normal, whether there are faults in the
electrical system, whether the transmission parts can operate
smoothly, clean the welding work area, and confirm that the welding
materials (busbars, etc.) are fully prepared.
2. Question: What should be done if a fault alarm occurs during the
operation process?
Answer: First, check the alarm prompt information, and judge
whether the problem is caused by electrical faults, mechanical
faults or abnormal welding parameters, etc. according to the
equipment operation manual. If it can be solved by yourself, handle
it according to the steps in the manual. If it cannot be solved,
contact professional maintenance personnel in time.
Related to production efficiency
1. Question: How to improve the production efficiency of the
multi-busbar photovoltaic string welder?
Answer: Optimize the welding parameters to reduce the welding time,
do a good job in the daily maintenance of the equipment to ensure
few shutdowns due to failures, arrange production batches
reasonably, and improve the proficiency of operators, all of which
will help improve the efficiency.
2. Question: What is the maximum production capacity that the
equipment can reach?
Answer: Different models and configurations of multi-busbar
photovoltaic string welders have different production capacities.
Generally, thousands of battery cells can be welded per hour. The
specific situation depends on the design specification parameters
of the equipment.
Related to maintenance
1. Question: What maintenance work needs to be done for the
equipment on a daily basis?
Answer: It is necessary to regularly clean the dust and debris on
the surface and inside of the equipment, add lubricating oil to the
transmission parts, check the wear condition of the welding heads,
calibrate the welding parameters, and check whether the connections
of electrical lines are loose.
2. Question: How often is it more appropriate to conduct a
comprehensive maintenance and overhaul?
Answer: It is recommended to conduct a comprehensive maintenance
and overhaul every 1 to 3 months according to the usage frequency
of the equipment to ensure that all aspects of the equipment's
performance are good and it can operate stably.
Related to product quality
1. Question: How to test the quality of the products after welding?
Answer: You can conduct appearance inspections to see whether the
welding joints are firm and whether there are problems such as poor
welding or detachment. Professional electrical testing equipment
can also be used to detect whether the electrical performance
indicators such as the series resistance after welding meet the
standards.
2. Question: How to handle the defective products after welding?
Answer: Analyze the causes of the defects. If it is a problem of
process parameters, adjust the parameters in time. If it is a
problem of materials, replace the qualified materials. Mark the
defective products, store them separately, and handle them
according to the relevant procedures for rework or scrapping.