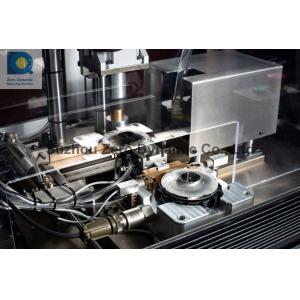

Add to Cart
1. Equipment Description
Zero Dynamic's BLDC Motor Assembly Automatic Balancing machine
Vacuum Cleaner Motor, Sweeper Motor Scissor Correction Balancer is applicable for unbalance detection and automatic correction of
various DC, AC, BLDC motor assembly such as vacuum cleaner motor,
sweeper motor and ventilator motor.
Zero Dynamic's BLDC Motor Assembly Automatic Balancing machine Vacuum Cleaner
Motor, Sweeper Motor Scissor Correction Balancer adopts soft bearing dynamic balance test stand which has impler
structure and more stable performance. The balancing machine adopts
acceleration sensors, no lateral sensitivity, lower limit
requirements, making the operation requirements easy and fast. The
structure is compact, firm and reliable. Its mechanical model is
reasonable, so that the actual unbalance of the rotor can be truly
reflected by the support frame and the sensor.
Zero Dynamic's BLDC Motor Assembly Automatic Balancing machine Vacuum Cleaner
Motor, Sweeper Motor Scissor Correction Balancer is compatible with balance measurement & automatic correction
of motors with different sizes (different motor need to be
customized with corresponding fixture). The same product can be
produced continuously without the need to re-calibrate.
The changeover is easy, and the operator can change the fixture and
re-calibrate the machine independently after quick training.
Serial No. | Item Details | Parameter Range |
1 | Maximum diameter for rotor | Φ30-80mm (dimension of motor fixation part) |
2 | Allowable detection diameter range for impeller | Φ30~Φ90mm |
3 | Single plane high speed dynamic balance correction | In conformity with ISO1940 Standard, balance grade G1 |
4 | Minimum attainable residual unbalance | < 0.03g.mm |
5 | Unbalance reduction ratio URR | ≥90% |
6 | Production cycle time | ≤30S |
7 | Dynamic balance function | Single plane dynamic balance |
8 | Drive method | Self-drive |
9 | Power supply (V AC/HZ) | 220V/50HZ |
10 | Safety protection | Enlosed |
11 | Equipment external dimension | 800*650*1700mm |
3. Equipment Photo:
4. Main Features:
4.1 Under the production condition, the equipment works
continuously, the whole machine runs smoothly, the cycle time meets
the requirements and there's no tripping and jamming. The whole
equipment control is safe and reliable and the performance meets
the requirements.
4.2 Ultra-high accuracy, meeting with G1 accuracy requirement.
4.3 Laser detector is adopted to automatically record the revolving
speed. Manual streaking is not required and this saves time and
labor.
4.4 Automatic iron fillings collection system (working
synchronously with the equipment).
4.5 Simple design of work fixture, easy for changeover,
time-saving. Applicable for mass production.
4.6 It adopts Windows system which is easy to learn and can be
operated skillfully without much skills.
4.7 Automatic loading and unloading position can be reserved to
facilitate the automation renovation of production line (Optional).
4.8 It supports MES data uploading.
4.9 Monitoring of the cutter life.
4.10 Measurement accuracy: ≤0.03g.mm
4.11 The balance display interface is intuitive, and the
measurement value and angle are directly displayed digitally on the
balancing machine.
4.12 Automatic removing material, automatic retest.
4.13 Maximum revolving speed: ≤45000 rpm (7 blades)
Suzhou Zero Dynamic Co., Ltd is a top Chinese manufacturer engaging
in full automatic balancing equipment and related vibration
measurement since 2003.
Over the past 20 years, Zero Dynamic has developed 100+ kinds of
equipments. We mainly deals with all kinds of advanced dynamic
balancing equipment, field dynamic balancing instrument, vibrometer
and motor performance testing machine. High revolving speed and
high precision are the key features of our products. We have served
3000+ clients in China and abroad, including many world-famous
companies such as LG, Black&Decker, Nidec, Huawei, Foxconn,
Midea, Ecovas, Daikin, Lexy.
Now (2024) Zero Dynamic has a factory of 10,000sqm and more than
120 staff including a professional R&D team of 30+ engineers
and 20+ debugging and after-sales team.