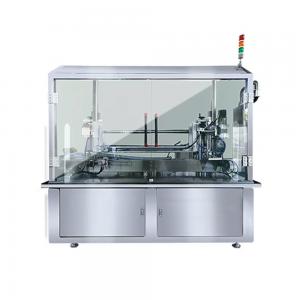

Add to Cart
Automatic High Speed Inverting Bottle Air Or Wet Rinsing Machine
Bottle Rinsing Machines, which invert bottles for cleaning, utilize air, water, or other solutions to remove debris before filling. These machines employ soft pad bottle grippers to prevent damage to containers, accommodating various materials like glass and plastic.
Inverting Wet Bottle Rinsing Machine:
Automatic machines use 2 to 16 rinse heads to wash contaminants
prior to filling, preventing debris from affecting the final
product. Bottles are indexed into the rinse area using gates or
starwheels, with each cycle processing as many bottles as there are
rinse heads. Soft pads grip bottles as the rinsing carriage inverts
them over a rinse basin, spraying water or cleaning solution to
remove dust and contaminants. Bottles then return to the conveyor
for filling.
Inverting Air Bottle Rinsing Machine:
Similar to wet rinsers, these machines blast bottles with air to
remove dust and debris. Before rinsing, an ionized air curtain
eliminates static charge, ensuring thorough cleaning. Air rinsers
can handle various bottle materials and can be combined with bottle
vacuums for unique containers. Dual-action nozzles blast containers
with air and vacuum out debris while they remain on the conveyor
belt.
Customized equipment can also be designed for specific containers or production environments.
parameter
Power | 220V 1Phase, 1KW |
Applied Container | Plastic Bottles, Glass Bottles, Jars |
Speed | 25-30 bottles/min (Related to the number of rinsing heads) |
Rinsing Heads | 6 heads(Can be customized 2-16 heads) |
Air Pressure | 0.6MPA(Customized according to production) |
NPACK manufactures a popular rinsing machine known as the inverting bottle rinsing machine. This machine lifts containers from the conveyor and inverts them over a rinse basin, where they are blasted with air, water, or other rinse media to remove dust and debris that could contaminate products.
The inverting bottle rinsing machine is an automatic packaging system equipped with an indexing system to rinse multiple bottles simultaneously. Upon entering the rinsing area, bottles are secured with a clamp and inverted over the rinse basin, with one nozzle allocated for each bottle in the cycle. These nozzles rinse the bottles' interiors using air, water, or other cleaning agents, allowing debris to flow into the rinse basin. Once rinsing is complete, bottles are returned to the conveyor, the clamp opens, and clean containers proceed to the filling machine. This machine can handle glass and plastic containers of various shapes and sizes.
Operators manage the rinsing machine via a user-friendly touchscreen interface, enabling adjustment of indexing and rinse times and other settings communicated to the machine via PLC signals. Additionally, a recipe can be saved for each bottle rinsed, facilitating quick changeover with minimal physical adjustments for bottle widths and heights.