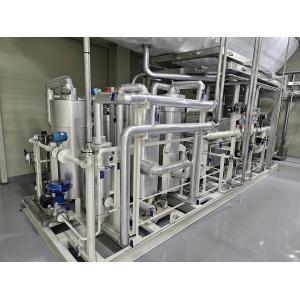

Add to Cart
Low temperature distillation process
Pre-treatment of raw gas: The gas mixture containing argon is first
preliminarily treated to remove solid impurities and moisture,
etc., so as to prevent these impurities from freezing in the
subsequent low-temperature environment, which will affect the
operation of the equipment.
Compression and cooling: the gas is compressed after pretreatment
to increase the gas pressure, and then the temperature is lowered
through the cooling system to make the preliminary liquefaction of
the gas mixture.
Low-temperature distillation: the preliminary liquefied gas mixture
is sent to the distillation tower, using the different boiling
points of argon and other gases (e.g. nitrogen, oxygen, etc.) to
carry out gas-liquid equilibrium separation for many times at
different temperatures and pressures. In the distillation tower,
the distribution of temperature and pressure is the key, through
the control of these parameters, so that the argon gas is enriched
in a specific tower plate position, and ultimately from the top or
bottom of the tower to get high purity argon gas.
Product gas treatment: The obtained high purity argon gas is
further processed, such as re-cooling, drying, etc., in order to
meet the requirements of different users on the purity and quality
of argon gas.
Adsorption process
Impurity adsorption: the mixed gas containing argon is passed into
the adsorption tower equipped with adsorbent (such as activated
carbon, molecular sieve, etc.). The adsorbent has different
adsorption capacity for different gases, and can preferentially
adsorb the water, carbon dioxide, oxygen and other impurities, so
that argon is initially purified.
Adsorbent regeneration: when the adsorbent adsorption saturation,
it is necessary to regenerate it to restore the adsorption
capacity. Usually using heating, depressurization and other
methods, so that the adsorbed impurities from the adsorbent
desorption, discharged from the system.
Depth purification: After preliminary purification of argon by
adsorption tower, it may still contain a small amount of
impurities, which can be purified by series connection of multiple
adsorption towers or by using different types of adsorbents for
depth purification to further improve the purity of argon.
Membrane separation process
Membrane filtration: Argon containing gas mixture under the
pressure difference, through the membrane module with selective
permeability. Different gas molecules due to differences in size,
shape and chemical properties, the permeation rate in the membrane
is different, thus realizing the separation of argon and other
gases. For example, some polymer membranes have higher permeability
to argon and lower permeability to other impurity gases, enabling
argon to preferentially permeate through the membrane while the
impurity gases are retained.
Multi-stage separation: in order to improve the purity and recovery
of argon, usually using multi-stage membrane separation process.
After a level of membrane separation of argon enriched gas is again
sent to the next level of membrane separation device for further
separation and purification, through multi-stage separation can
gradually improve the purity of argon.
Tail gas treatment: the gas (tail gas) which does not pass through
the membrane in the process of membrane separation usually contains
a certain amount of argon and other impurities, and the tail gas
can be further processed, such as recovering the argon therein or
discharging it according to the standard.
Function
Efficient recovery of argon gas: it can recover the argon gas
emitted in the industrial production process, avoiding the waste of
resources caused by the direct emission of argon gas into the
atmosphere, improving the utilization rate of argon gas, and
reducing the production cost of enterprises. For example, in the
semiconductor manufacturing, metal processing and other industries,
a large number of argon as a protective gas, through the recovery
and purification skid can be discharged in these processes of waste
argon gas recycling and reuse.
Deep purification of gas: can remove oxygen, nitrogen, moisture,
carbon dioxide, carbon monoxide and other impurities in argon, so
that the purity of argon gas reaches a very high level, to meet the
demand for high-purity argon gas in different industries. Such as
chemical vapor deposition in semiconductor manufacturing, crystal
growth and other processes, the need to use the purity of argon up
to 99.999999999% or more, argon recovery and purification of the
skid can be through a variety of purification techniques to achieve
this requirement.
Automatic control operation: Equipped with intelligent control
system, it can realize automatic operation and remote monitoring.
It can monitor and adjust the parameters in the recovery and
purification process in real time, such as temperature, pressure,
flow rate, etc., to ensure the stable operation of the system and
improve the production efficiency and safety. The operator can
easily set parameters, check the operation status and receive alarm
information through the control interface.
Energy-saving and environmental protection function: By recovering
argon gas and reusing it, it reduces the need for new argon gas
mining and production, which helps to save energy and resources,
and is also in line with the concept of environmental protection
and reduces the impact on the environment. In addition, some skid
blocks are designed with energy-efficient components and optimized
processes to reduce energy consumption during operation.
Adaptation to different working conditions: with flexible design
and configuration, it can be customized according to the needs of
different users and the characteristics of the production process,
adapting to a variety of complex industrial environments and gas
composition conditions. Whether it is local argon recovery for
small enterprises or large-scale argon purification in large-scale
industrial production, it can provide corresponding solutions.
Translated with DeepL.com (free version)