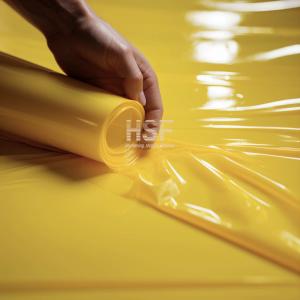

Add to Cart
50 μm yellow polyethylene volatile corrosion inhibitor (VCI) film is a specialized packaging material designed to protect metal components and products from corrosion. The yellow color indicates the presence of VCI compounds that release corrosion-inhibiting vapors. Here are some application scenarios where 50 μm yellow polyethylene VCI film can be used:
Metal Packaging: The VCI film is commonly used for packaging metal components, parts, and finished products. It is particularly beneficial for long-term storage and transportation, where metal items are vulnerable to corrosion. The film creates a protective environment by releasing VCI vapors that form a molecular layer on metal surfaces, inhibiting the corrosive process.
Automotive Industry: The VCI film is extensively utilized in the automotive industry to protect various metal components and parts, such as engine parts, brake components, and electrical connections. It helps prevent corrosion during manufacturing, shipping, and long-term storage, ensuring the quality and performance of automotive parts.
Machinery and Equipment: 50 μm yellow polyethylene VCI film is suitable for protecting machinery and equipment during storage or shipping. It can be used to wrap sensitive metal surfaces, such as gears, bearings, and tools, providing a protective barrier against moisture and corrosion-inducing elements.
Metal Fabrication and Processing: During metal fabrication and processing operations, metal surfaces are exposed to moisture, contaminants, and atmospheric conditions that promote corrosion. The VCI film can be employed as a temporary or permanent protective cover for metal sheets, coils, and finished products, guarding them against corrosion until further processing or use.
Electrical and Electronic Equipment: The VCI film finds application in the electrical and electronic industries to protect metal components, connectors, and sensitive electronic circuitry from corrosion. It can be used as a wrapping material for electrical panels, control cabinets, connectors, and other metal parts susceptible to corrosion during storage or shipping.
Marine and Offshore Applications: In marine and offshore environments, metal components, equipment, and structures are exposed to harsh saltwater and corrosive conditions. The VCI film can be utilized to protect metal parts, piping, and equipment during storage or transportation, minimizing the risk of corrosion and extending their service life.
Aerospace Industry: The aerospace industry requires stringent corrosion protection measures for critical components and parts. The VCI film can be used to protect metal aircraft parts, engines, avionics, and ground support equipment from corrosion during storage and transportation, ensuring their reliability and performance.
It's important to follow manufacturer guidelines and recommended
practices when using 50 μm yellow polyethylene VCI film to achieve
effective corrosion protection. Proper sealing and storage
conditions should be maintained to maximize the film's
corrosion-inhibiting properties.
VCI (volatile corrosion inhibitor) film is made of a combination of
plastic polymers and corrosion inhibitors. The plastic polymers
used in the film can be low-density polyethylene (LDPE), linear
low-density polyethylene (LLDPE), or high-density polyethylene
(HDPE), among others. These polymers provide strength, flexibility,
and durability to the film.
The corrosion inhibitors used in the VCI film are a blend of
different chemicals that release vapors or molecules that react
with the metal surface and form a protective layer. The type and
concentration of the corrosion inhibitors used in the film may vary
depending on the specific application and the type of metal being
protected.
Some common corrosion inhibitors used in VCI films include:
1. Amines:
These are organic molecules that release vapor or molecules that
react with the metal surface and form a protective layer.
2. Nitrites:
These are chemical compounds that release a combination of nitrogen
and oxygen ions that neutralize corrosive elements.
3. Phosphates:
These are compounds that react with metal surfaces to form a
protective layer, which inhibits corrosion.
4. Benzotriazoles:
These are organic molecules that form a thin protective layer on
metal surfaces, inhibiting corrosive ions from interacting with the
metal.
The production of VCI films involves several steps. Here's a brief
overview of the process:
1. Mixing of Plastic Resins:
The production process usually starts by mixing different plastic
resins, such as LDPE, LLDPE, or HDPE, in a large mixing vat. The
specific blend of plastic resins used will depend on the desired
properties of the finished VCI film.
2. Addition of Corrosion Inhibitors:
Once the plastic resins are mixed, a specific blend of corrosion
inhibitors is added to the mixture. The specific blend and
concentration of corrosion inhibitors used will depend on the type
of metal being protected and the desired level of corrosion
protection.
3. Extrusion:
After adding the corrosion inhibitors, the plastic resin mixture is
extruded through a die, which forms the VCI film into a continuous
sheet or roll. The extrusion process involves heating and melting
the plastic resins and corrosion inhibitors to form a homogenous
mixture.
4. Cooling:
The extruded VCI film is then cooled, either by air or water
cooling, to solidify the plastic resins and corrosion inhibitors
into a stable film.
5. Slitting and Winding:
Once the VCI film is cooled and solidified, it is then slit and
wound onto rolls of various widths and lengths, depending on the
customer's requirements.
The production process of VCI films may involve additional steps or
modifications, depending on the specific manufacturer and the
desired properties of the finished film. However, the basic steps
outlined above are common across most VCI film production
processes.
Property | Test method | Unit | Data | |||
Thickness | ASTM D6988 | μm | 50 | 100 | 150 | |
Tensile modulus | MD | ASTM D882 | N/m | 1582 | 3103 | 3200 |
TD | 1604 | 3117 | 3112 | |||
Tensile strength @ break | MD | ASTM D882-02 | Kpa | 32.5 | 29.8 | 21.08 |
TD | 31.8 | 30.1 | 21 | |||
Elongation @ break | MD | ASTM D882-02 | % | 599 | 752 | 740 |
TD | 654 | 813 | 810 | |||
Flexural strength | MD | ASTM D882-02 | Kpa | 14.03 | 8.1 | 5217 |
TD | 9.6 | 10.5 | 8915 | |||
Tear strength | MD | ASTM D1922-06a | mN | 3700 | 11092 | 14696 |
TD | 7661 | 15017 | 19941 | |||
Dart impact resistance | ASTM D1709-04; A | grams | 321 | 743 | 748 |