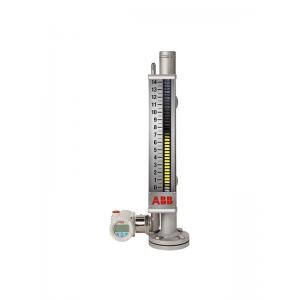

Add to Cart
High accuracy non-intrusive liquid level and interface level detection
The LMT200 is based upon the magnetostrictive principle.
1. The device electronics generates a low energy current
pulse at fixed intervals.
2. The electrical pulses create a magnetic field which
travels down a specialized wire inside the sensor tube.
3. The interaction of the magnetic field around the wire
and the magnetic float causes a torsional stress wave
to be induced in the wire. This torsion propagates
along the wire at a known velocity, from the position of
the magnetic float and toward both ends of the wire.
4. A patented sensing element placed in the transmitter
assembly converts the received mechanical torsion
into an electrical return pulse.
5. The microprocessor-based electronics measures the
elapsed time between the start and return pulses
(Time of Flight) and converts it into a position measure-
ment which is proportional to the level of the float.
Features:
Options:
Material:
Standard: 316/L Stainless Steel
Options: Alloy 20, Hastelloy® C-276, FEP-TEFLON® jacketed,
electropolished 316/316L Stainless Steel, others on request
Standard probe length: 304.8mm to 15.24 m (1 to 50 ft); 90 degree probes (SEH Option)
304.8mm to 7.62m (1 to 25 ft)
Probe length tolerance:
± 3.2mm (0.125in) up to 3.0m (10ft); +/- 6.4mm (0.25in) up to 6.0m
(20ft);
± 9.0mm (0.35in) up to 9.0m (29.5ft); +/- 25.4mm (1.0in) up to
15.24m (50ft)
Mounting: Stainless Steel Clamps for KM26 Magnetic Level Gauge Chamber
Included; Optional Vibration Isolation Mounts
Notes:
1 Measurement accuracy is recorded at factory ambient conditions
(23.88 °F +/-5.6 °C (75 °F +/-10 °F)) using a calibration magnet.
Accuracy may be further influenced by
other factors such as float hysteresis, installation, process
conditions and ambient conditions.
2 Some agency approvals may differ.
HART® is a registered trademark of the FieldComm Group