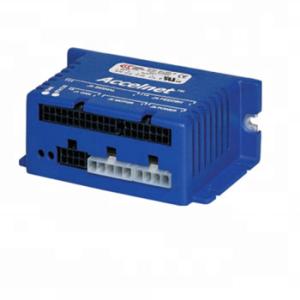

Add to Cart
Indexing Mode PLC Powered Accelnet Servo Motor Drive For Distributed Control Network
Description
COPLEY DRIVE
The drive provides a rich absolute value encoder interface that
supports Endat,Biss,SSI and Absolute A Protocols such as. Provide
the CMO or CML source code that can be called directly can be
developed under Windows and ROST,It can call directly related
motion function, that controls the motor according to the specified
position speed and time(PNT)curve Perform the motion.
Accelnet Micro Panel is a compact, DC powered servo drive
for position, velocity, and torque control of AC brushless and
DC brush motors. It can operate on a distributed control
network, as a stand-alone indexing drive, or with external
motion controllers. Two versions are available to support digital
quadrature, or analog sin/cos encoders.
Indexing mode enables simplified operation with PLC’s which
use outputs to select and launch indexes and inputs to read
back drive status. Additionally,PLC can send ASCII data
that can change motion profiles so that one index can perform
various motions as machine requirements change. DeviceNet
capability enables multiple Accelnet drives to be controlled
from PLC’s that use this communication protocol.
The CANopen distributed control architecture is also supported.
As a CAN node operating under the CANopen protocol, it
supports Profile Position, Profile Velocity, Profile Torque,
Interpolated Position, and Homing.Up to 127 drives can
operate on a single CAN bus and groups of drives can be linked
via the CAN so that they execute motion profiles together.
Operation with external motion controllers is possible
in torque (current), velocity, and position modes. Input
command signals can be ±10V (torque, velocity, position),
PWM/Polarity (torque, velocity), or stepper format (CU/CD or
Step/Direction).
MODEL | AC3-055-09 | ACJ-055-18 | ACJ-090-03 | ACJ-090-09 | AJ-90-12 | ||||
OUTPUT POWER | |||||||||
Peak Current | 9(636) | 18(12.73) | 3(212) | 9(636) | 12(8.5) | Adc(Arms, sinusoidal,±5% | |||
peak time | 1 | 1 | 1 | 1 | 1 | Sec | |||
continuous current | 3(2.12) | 6(4.24) | 1(0.71) | 3(2.12) | 6(4.24) | Adc(Arms,sinuscidal),±5% | |||
Peak Output Power | 490 | 970 | 270 | 800 | 1600 | w | |||
continuous" " | 163 | 323 | 89 | 267 | 533 | w | |||
Output resistance | 0.075 | 0.075 | 0.075 | 0.036 | 0.075 | Rlout(Ω) | |||
Maximum output votage | vout≌HV0.97*Rou*tlout | ||||||||
INPUT POWER | |||||||||
Hv.to Hv. | 20-55 | 20-55 | 20-90 | 20-90 | 20-90 | +vdc,lransfo mer-iolaed | |||
lpeak | 9 | 18 | 3 | 9 | 12 | Adc(1 sec) peak | |||
Icont | 3 | 6 | 1 | 3 | 6 | Adc continuous | |||
Aux HV | 20-HVmax +Vdc @ 500 mAdc maximum | ||||||||
PWM OUTPUTROLS | 3-phase MOSFET inverter ,15 kHz center-weighted PWM, space-vector
modulation 3o kHz | ||||||||
Type pwm ripple frequency | |||||||||
DIGITAL CONTROL | |||||||||
Digital Control Loops | current,veocity,postion. 100% digital loop control Dual loop position cortrol using secondary encoder input Current loop:15 kHz(66.7 us)Velocity, position loops: 3kHz(333 us) sinusoidal field-oriented control or trapezoidal from Halls for brushliess motors certer-weighted PWH with space-vector modulation current loop:2.5 kHz typical, bandwidth will vary with tuning & load inductance changes in bus voltage do not affect bandwidth 200 uH line-line | ||||||||
samping rate (time) | |||||||||
commutation | |||||||||
Modulation | |||||||||
Bandwidths | |||||||||
HV Compensation | |||||||||
Minimum load inductance | |||||||||
COMMAND INPUTS | |||||||||
CANopen | Profile Position,Interpolated Position, Profile Velocity,Profile Torque,Homing | ||||||||
Digital position | Step/Direction,CW/CCW stepper commands (2 MHz maximum rate) | ||||||||
Quad A/B Encoder | 20 Mcount/sec (after quadrature),5Mline/ sec | ||||||||
Digital torque & velocity | pWM,Polarity | PWM ≌ 0~100%,polarity=1/0 | |||||||
PWM | PWM≌50% ±50%,no polarity signal required | ||||||||
PWM frequency rangr | 1kHz minimum,100kHz maximum | ||||||||
Pw minimum pulse width | 220 ns | ||||||||
Analog torque/velocity/positon | ±10 vdc,5kΩ dirferential input impedance | ||||||||
DIGITAL INPUTS | |||||||||
Number type | 9,non-isolated.[IN1]dedicated to Drive Enable
function,[IN2]~[IN9]are programmable 74HC14 Schmitt trigger operating from +5 Vdc with RC filter on input 10 kΩ to +5 Vdc or ground for all except [IN5](see below) Vin-Lo 1.35 Vdc,vin-HI >3.65 vdc All inputs have group selectable connection of input pull-up/ down reslstor to +5 Vdc,or gound 1 Dedicated input with 330 us RC filter for drive enable,0 to +24 Vdc max 3 General Purpose irputs with 330 us RC filter,0 to+24 vdc max 1 Mediun-Speed input for motor temperature switch,33 us RC filtet 4.99 kΩ pullup/pulldown,0 to +24 vdc max 4 High-Speed inputs irputs with 100 ns RC filter,0 to +5 Vdc max | ||||||||
All inputs | |||||||||
Logic levels | |||||||||
Pull-up,pull-down control | |||||||||
Enable[IN1] | |||||||||
GP[IN2,3,4] | |||||||||
MS [IN5] | |||||||||
HS[IN6,7,8,9] | |||||||||
DIGITAL OUTPUTS (NOTE 1) | |||||||||
Numbet type | 4,non-isolated,programmable current-sinking MDSFETwith 1 kΩ pullup to +5 Vdc through diode 300 mAdc max,+30 ve max.Functions programmable External fyback diode requred if driving inductive loads | ||||||||
[OUT1~4] | |||||||||
current rating | |||||||||
current rating |
driver application market