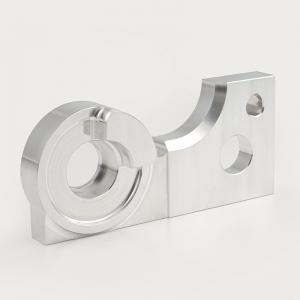

Add to Cart
Custom CNC Machining Milling Aluminum CNC Parts Anodizing Service Turning
Parts CNC Machining Aluminum Parts
Aluminum is an excellent material for CNC machining due to its high machinability, ductility,
and favorable strength-to-weight ratio.
It offers outstanding thermal and electrical conductivity, low density, and inherent resistance to
corrosion. Aluminum can also be anodized for additional surface protection and aesthetic finishes.
Product Details
Properties of Aluminum
1. Excellent corrosion and chemical resistance
2. High strength-to-weight ratio
3. Good heat and electrical conductivity
4. Easily machined
5. Reflects heat and light
Common Aluminum Materials | |
No. | Properties |
Aluminum 6061-T6 | Aluminum 6061 (CNC) is the most popular aluminum alloy. It has good strength-to-weight ratio, excellent machinability and natural corrosion resistance. |
Aluminum 7075-T6 | Aluminum 7075-T6 (CNC) is an aerospace-grade material with excellent strength-to-weight ratio and strength and hardness comparable to steels. |
Aluminum 6060 | Alloy 6060 offers good strength, relatively good corrosion resistance and is suitable for decorative anodizing. |
Aluminum 6082 | Aluminum 6082 (CNC) has very similar composition and properties to 6061, with slightly higher tensile strength. Compliant with British Standards. |
Aluminum 5083 | Aluminum 5083 (CNC) is a strain hardening aluminum alloy with excellent corrosion resistance. Suitable for marine applications. Can be welded. |
Aluminum 6063 | Aluminum 6063 has good mechanical properties and can be heat treated. Suitable for aerospace applications. Can be welded. |
Aluminum 5052 | Aluminum 5052 is a strain hardening aluminum alloy with excellent corrosion resistance. Suitable for marine applications. Can be welded. |
Aluminum 2024 | Aluminum 2024 is a high-strength alloy with excellent fatigue resistance. Suitable for aerospace applications. |
Aluminum 7050 | Aluminum 7050 has excellent mechanical properties with good ductility, high strength, toughness and good resistance to fatigue. Suitable for aerospace applications. |
Aluminum Finishing and Post-Processing
Aluminum can also be anodized for additional surface protection and aesthetic finishes.
Name | Machining Marks |
Anodizing Type II | Reduced for non-cosmetic, removed on primary surfaces for cosmetic |
Anodizing Type III | Visible under anodizing |
Chromate conversion coating | Visible |
Electroless nickel plating | Reduced but visible |
As machined | Visible, light surface scratches |
Smooth machining | Visible, light surface scratches |
Fine machining | Slightly visible |
Polishing | Removed on primary surfaces |
Bead blasting | Removed for non-cosmetic, removed on primary surfaces for cosmetic |
Brushing | Reduced for non-cosmetic, removed on primary surfaces for cosmetic |
Powder coating | Removed |
Applications of CNC Aluminum Parts
Our aluminum parts are precisely tailored to match the specific needs of various applications,
such as automotive precision components, precision motor parts, medical instrument components,
power tool parts, machine components, high-end electronic devices, home appliance parts,
and more.
Company Profile
FAQ's
1. Why choose CNC machining?
CNC machining is a rapid, precise, and adaptable manufacturing process.
It stands out as a manufacturing solution that can deliver end-use parts efficiently, regardless of
the production volume, without the necessity of investing in costly hard tooling or elaborate setups.
2. What's the general surface texture of CNC milled and turned parts?
In the realm of CNC machining, as-machined milled parts typically exhibit a surface roughness of
approximately 3.2μm (or 1.6μm in the case of relatively new machines).
On the other hand, when it comes to turned parts, we can achieve a smoother surface with a
roughness of 0.8μm. This means that machining speed adjustments are not necessary to attain
this level of surface finish.
3. How long does delivery time and quotation take?
Delivery time is determined based on the complexity of the parts. For low-complexity parts,
the lead time is typically 2-3 days. As the complexity of the parts increases, the lead time can range
from 2-5 days. High-complexity parts may require a lead time of 5-15 days.
Similarly, the quotation process varies depending on the complexity
of your design.
Quotes can be provided in as little as 1 business day, or it may take 3 or more business days for
more intricate designs.
If you have a design that you would like our team to assess and
provide a quote for, please don't
hesitate to contact us.
4. What are you shipping terms?
Our standard shipping terms are Ex Works (EXW) for both rapid prototyping and regular production
orders.
Under EXW terms, the customer is responsible for all aspects of shipping, customs clearance,
and associated fees once the goods have been dispatched from our facility.
For express shipments, we utilize Delivered Duty Unpaid (DDU) terms. This means that the client
is responsible for settling any import duties upon the goods' arrival at their designated destination.