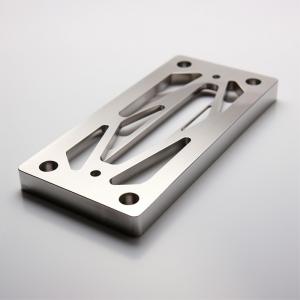

Add to Cart
CNC machining, short for computer numerical control machining, is a subtractive manufacturing
technique that utilizes computerized controls and machinery to selectively remove material layers
from a solid block. Precise cuts in the material are orchestrated through programmed instructions,
allowing automated machinery to execute the machining tasks with accuracy and efficiency.
Product Details
Common Metal Materials for CNC Machining | |
Metal Material | Properties |
Aluminum | 2024: Good fatigue resistance and strength; excellent toughness at moderate to high strength levels; improved fracture toughness |
6061: Excellent machinability, low cost, and versatility | |
7075: High strength, hardness, low weight, and heat tolerance | |
Stainless steel | Excellent machinability and outstanding uniformity; good workability and weldability, high ductility and formability |
Steel Alloy | Mix of chromium, molybdenum, and manganese yields toughness, good torsional and fatigue strength |
Brass | Versatile and highly attractive copper/zinc alloy with warm yellow color accommodates severe forming/drawing |
Copper | High ductility and high electrical and thermal conductivity; develops attractive blue-green surface patina over time |
Titanium | Excellent strength to weight ratio, used in aerospace, automotive, and medical industries |
Steel Mild Low Carbon | High machinability and weldability, high stiffness; good mechanical properties, machinability, and weldability at low cost |
Surface Finishes | ||
Name | Applicable to | Machining marks |
As machined | Metals, Plastics | Visible, light surface scratches |
Smooth machining | ||
Fine machining | Metals | Slightly visible |
Polishing | Metals | Removed on primary surfaces |
Bead blasting | Metals | Removed for non-cosmetic, removed on primary surfaces for cosmetic |
Brushing | Metals | |
Anodizing Type II | Aluminum | |
Anodizing Type III | Aluminum | Visible under anodizing |
Black oxide | Copper, Stainless steel, Alloy steel, Tool steel, Mild steel | Visible |
Powder coating | Metals | Removed |
Brushed + electropolishing | Stainless steel | Removed on Primary surfaces |
CNC Machining Applications
CNC machining is widely used throughout the aerospace, medical,
automotive industries for its ability
to rapidly manufacture precise parts in production-grade materials.
Typical CNC parts, include:
1. Housings and enclosures
2. Brackets
3. Fixtures for manufacturing
4. Gears and bearings
5. Internal mechanical components
6. Medical instrumentation
Company Profile
FAQ's
1. How does our pricing compare to other suppliers?
When it comes to pricing, we offer a competitive advantage.
Typically, our prices for plastic injection mold tools and CNC machined/turned parts are 25-45%
lower than those of suppliers in North America and Europe.
In contrast to Chinese suppliers, we do not compete solely on price. Instead, we prioritize
delivering the utmost quality, rapid responsiveness, and professional results to our clients.
2. How soon can I receive my parts?
We can produce quality parts in as little as two weeks if you
provide us with complete 2D and 3D
CAD models. However, more complex parts with special features may have longer lead times.
Request a quote to receive more precise lead times based on your specific project.
Regarding shipping, our primary method is air freight, which
typically takes a few days for delivery
from China to Europe or North America.
3. How does you ensure part quality?
Our commitment to ensuring the quality of your parts includes a comprehensive approach:
1. Design for Manufacturing (DFM) Review: After your order is confirmed, we conduct a thorough
DFM review to identify and address any potential issues that could impact part quality.
2. Incoming Material Inspection: All incoming materials undergo rigorous inspection and
verification using advanced testing equipment to ensure they meet our quality standards.
3. Final Inspection Reports: Before shipment, each part undergoes a final inspection.
We provide detailed inspection reports, giving you complete visibility into the quality of your parts.
4. Real-time Inspection Data: We have the capability to share inspection data with you in real-time.
This collaborative approach allows us to address any quality concerns during the production process,
ensuring that your specifications and expectations are met.
Our commitment to quality control is integral to delivering parts that meet your exacting standards.