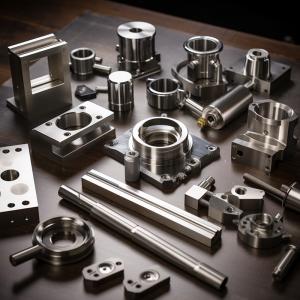

Add to Cart
Our custom CNC machining service operates within the realm of the prevalent subtractive
manufacturing technology, CNC machining. This method stands out as the go-to solution for
crafting tailor-made metal and plastic parts essential for prototyping and production applications.
Employing CAD modeling software and G-code, CNC milling and CNC turning machines meticulously
remove material from solid workpieces with a combination of precision and speed.
The outcome is the production of robust components featuring precise tolerances and a wide
spectrum of material properties, encompassing both mechanical and chemical attributes.
Designed to excel in one-off projects and low-to-medium volume production, our service benefits
from the efficiencies brought about by automation and high repeatability.
Product Details
Common Materials | |
Name | Description |
Aluminum | High machinability and ductility, good strength-to-weight ratio. |
Stainless steel | High tensile strength, corrosion and temperature resistant. |
Mild steel | High machinability and weldability, high stiffness. |
Brass | Low friction, excellent electrical conductivity, golden appearance. |
Copper | Excellent thermal and electrical conductivity. |
Titanium | Excellent strength to weight ratio, used in aerospace, automotive and medical industries. |
ABS | Common thermoplastic, impact resistant, easy to machine. |
Nylon | Excellent mechanical properties, thermal, chemical and abrasion resistant. |
PVC | Excellent chemical and weather resistance and good toughness. |
Surface Finishes | ||
Name | Applicable to | Machining marks |
As machined | Metals, Plastics | Visible, light surface scratches |
Smooth machining | ||
Fine machining | Metals | Slightly visible |
Polishing | Metals | Removed on primary surfaces |
Bead blasting | Metals | Removed for non-cosmetic, removed on primary surfaces for cosmetic |
Brushing | Metals | |
Anodizing Type II | Aluminum | |
Anodizing Type III | Aluminum | Visible under anodizing |
Black oxide | Copper, Stainless steel, Alloy steel, Tool steel, Mild steel | Visible |
Powder coating | Metals | Removed |
Brushed + electropolishing | Stainless steel | Removed on Primary surfaces |
Specialist Industries
Our extensive production experience, spanning millions of components for diverse applications,
showcases a particular focus and proficiency in the following specialized industries:
1. Aerospace & Aviation: With precision at the forefront, our
components meet the rigorous criteria
of the aerospace and aviation sectors, delivering reliability and performance in crucial applications.
2. Automotive: From essential engine components to intricate
systems, our proven expertise in
manufacturing high-quality parts significantly contributes to the efficiency and safety of automotive
technologies.
3. Industrial Machinery: Our capabilities extend to the production
of components powering industrial
machinery, ensuring durability and precision to meet the multifaceted demands of manufacturing
processes.
4. Consumer Electronics: We excel in crafting components for
consumer electronics, actively
contributing to the advancement and functionality of state-of-the-art electronic devices.
5. Robotics & Automation: In the ever-evolving landscape of
robotics and automation, our
precision components play a pivotal role, enhancing the seamless operation and efficiency of robotic
systems.
6. Medical: Precision takes precedence in the medical industry, and
our purpose-designed components
meet the exacting standards of medical applications, fostering continuous progress in healthcare
technology.
Our unwavering dedication to excellence and specialized knowledge
within these industries positions
us as a trusted partner, ensuring that our components consistently meet the unique requirements
and standards of each sector.
Company Profile
FAQ's
1. What cosmetic standards do you guarantee?
Our commitment to quality includes standard deburring and edge-breaking procedures for all CNC
machined parts. Any critical edges requiring a sharp finish must be explicitly indicated in technical
drawings. Surfaces are guaranteed to be free of defects such as scratches, dents, stains, blemishes,
hanging marks, and minor imperfections.
Critical surfaces (primary (a) side, as specified in technical drawings) will be void of mill steps and
other marks. For the secondary (b) side, minor hanging marks and up to 2 minor defects are deemed
acceptable.
To enhance surface roughness, visual properties, and wear resistance, various post-processing and
finishing methods can be applied to CNC machined parts.
2. How much does CNC machining cost?
The cost of CNC machining is influenced by factors such as complexity, quantity, and lead time.
To obtain an accurate quote, we encourage you to submit a 3D CAD model, allowing us to provide
an interactive quote with design for manufacturability (DFM) feedback.
Leveraging proprietary software and automated fixturing processes, we eliminate upfront
non-recurring engineering (NRE) costs. This makes CNC machining cost-effective for quantities as low
as 1 to 200 parts.
While prices may compare similarly or slightly higher than 3D printing, CNC machining offers superior
material properties and surface finishes.
3. A quick guide to CNC machining parameters
Most machining parameters are established by the machine operator
during the generation of G-code.
Build Size of CNC Machines:
CNC machines offer a notably large build area, especially when
compared to 3D printers.
CNC milling systems can handle parts with dimensions up to 2,000 x
800 x 100 mm (78” x 32” x 40”).
CNC turning systems can machine parts with a diameter of up to Ø
500 mm (Ø 20’’).
Accuracy and Tolerances:
CNC machining enables the production of parts with high accuracy
and tight tolerances.
Tolerances achievable with CNC machines can be less than half the
diameter of an average human hair,
reaching ± 0.025 mm or .001’’.
If tolerance is not specified in the technical drawing, the
operator typically machines the part with an
accuracy of 0.125 mm (.005’’).
Key Takeaways:
CNC machines excel in both build size and precision, making them suitable for a wide range of
applications.Operators have the flexibility to set machining parameters based on the specific
requirements of the project.
Understanding the build size and achievable tolerances is crucial
for designing parts that meet
precision and accuracy standards.