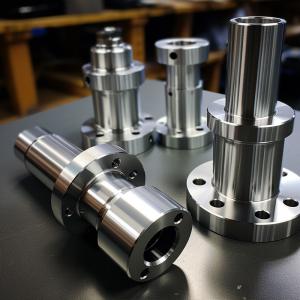

Add to Cart
In a broader sense, CNC machining generates components with precise tolerances and impressive
material properties. It is well-suited for individual tasks and low-to-medium volume production
(up to 1,000 parts) due to its high repeatability. However, it does impose more design constraints
compared to 3D printing, primarily due to its subtractive nature.
Product Details
Materials Suitable for CNC Turning
CNC turning is a versatile machining process that can effectively
work with various materials.
These materials include metals like aluminum, steel, brass, and titanium, as well as plastics
such as acrylic, nylon, and polycarbonate.
Common Materials | |
Name | Description |
Aluminum | High machinability and ductility, good strength-to-weight ratio. |
Stainless steel | High tensile strength, corrosion and temperature resistant. |
Mild steel | High machinability and weldability, high stiffness. |
Brass | Low friction, excellent electrical conductivity, golden appearance. |
Copper | Excellent thermal and electrical conductivity. |
Titanium | Excellent strength to weight ratio, used in aerospace, automotive and medical industries. |
POM | High stiffness, high accuracy, low friction, easy to machine. |
ABS | Common thermoplastic, impact resistant, easy to machine. |
Nylon | Excellent mechanical properties, thermal, chemical and abrasion resistant. |
CNC Turning Tolerances | ||
Limits for nominal size | Plastics | Metals |
0.5mm* to 3mm | ±0.1mm | ±0.05mm |
Over 3mm to 6mm | ±0.1mm | ±0.05mm |
Over 6mm to 30mm | ±0.2mm | ±0.10mm |
Over 30mm to 120mm | ±0.3mm | ±0.15mm |
Over 120mm to 400mm | ±0.5mm | ±0.20mm |
Over 400mm to 1000mm | ±0.8mm | ±0.30mm |
Over 1000mm to 2000mm | ±1.2mm | ±0.50mm |
Over 2000mm to 4000mm | ±2.0mm | |
*Please clearly indicate tolerances for nominal sizes below 0.5mm on your technical drawing. |
Typical Applications of CNC Turning
The versatility of CNC machining is evident as it permeates numerous industries, including
aerospace, automotive, consumer electronics, robotics, and agriculture, where the demand for
precision metal parts is high.
Additionally, CNC machining is a cornerstone in the production processes of medical devices,
household goods, and various consumer applications. Its reach extends further into sectors like
energy and oil and gas, establishing CNC machining as an omnipresent and fundamental
manufacturing method on a global scale.
Company Profile
FAQ's
1. What cosmetic standards do you guarantee?
Upholding stringent quality standards, our CNC machined parts undergo standard deburring and
edge-breaking procedures. Clear indications in technical drawings are required for any critical
edges that should be left sharp.
Surfaces are guaranteed to be defect-free, ensuring the absence of scratches, dents, stains,
blemishes, hanging marks, and minor imperfections. Critical surfaces (primary (a) side, as outlined
in technical drawings) will be meticulously free from mill steps and other marks.
On the secondary (b) side, minor hanging marks and up to 2 minor defects are considered within
acceptable limits. Additionally, a range of post-processing and finishing methods can be applied
to enhance surface roughness, visual aesthetics, and wear resistance for CNC machined parts.
2. The cost of CNC machining a part depends on a range of factors,
some of which are
listed below:
1. Material: Material selection introduces cost variations, with materials like aluminum being more
economical to machine compared to others like Inconel, attributed to factors such as tool wear and
cutting speeds.
2. Complexity: Parts featuring intricate designs incur higher
machining costs.
The complexity of surface shapes, for instance, significantly influences overall machining expenses.
3. Tolerances: The precision demanded by dimensional tolerances
impacts CNC machining costs.
Imposing overly tight tolerances on non-critical features can lead to unnecessary cost escalation.
4. Surface Finish: Achieving mirror finishes demands specialized
tools and machining strategies,
extending machining time and, consequently, increasing costs.
5. Quantity: Production volume is a key determinant of costs.
Low-volume production tends to be
costlier per part, as initial setup and programming costs are distributed over a smaller production run.
3. What are your tolerances for machined parts?
Our machined parts adhere to precision standards, featuring +.005”/- .005” local tolerances across
most metal geometries and +/- 0.010" for plastics. It's worth noting that tolerances may vary for
larger parts, especially with considerations for flatness post heat treatment.
An "As Milled" finish for CNC parts requires a minimum surface finish of 125.
Fabricated parts maintain a 0.010” dimensional tolerance and a 1° angular tolerance.
Tapped holes not explicitly labeled as features in the CAD model may be machined based on the
specified diameters. Crucially, surface treatments such as anodizing, bead blasting, iriditing,
powder coating, etc., will only be applied upon explicit payment and acknowledgment.