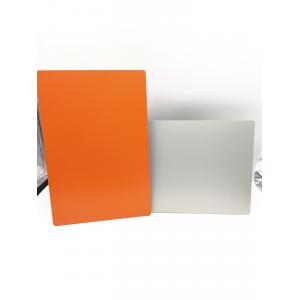

Add to Cart
PE Aluminum Composite Panel with 0.2mm Aluminum - Regular Color for Sea Vehicles
Aluminum plastic panel is a kind of flat panel consisting of a non-aluminum core sandwiched between two aluminum sheets. To improve its properties, it is usually coated with two types of paint, PVDF and PE, allowing a wide range of colors and finishes.
Aluminum plastic panel is versatile and widely used for many different occasions. In terms of its architectural uses, it can be seen everywhere from advertising signs to shop facades to interior decorations. It is highly valued for its durability, low weight, and tractability.
Besides, aluminum plastic panel is also a material with a promising future due to its energy efficiency and recyclability, which fits perfectly with the ongoing requirement of sustainable materials for modern constructions.
Lightweight: aluminum composite panels have a very high strength-to-weight ratio. With the same stiffness, they are about only 60% of the weight of aluminum plates, and 30% of steel plates.
Strong Adhesion: aluminum composite panels have high 180° peeling strength and are reliable for long-term use. There will not be any spontaneous peeling off of the aluminum plate and plastic core material.
Weather Resistance: when used outdoors, the color and gloss remain virtually unchanged, and the coating does not seem to wear off. Aluminum composite panels could even last more than 20 years.
Corrosion Resistance: the surface coating of the panels is very adherent and resistant to corrosion from various components, such as acid, alkali and salt mist. In particular, the PVDF fluorocarbon resin coating is especially solid.
Wind Pressure Resistance: the performance of aluminum composite panels has reached the national A level, which means they meet the requirements for high-rise exterior wall decoration in terms of wind pressure resistance.
Flame Resistance: The core layer of aluminum composite panels is non-toxic polyethylene, and the two sides are made of non-combustible aluminum thin plates. Any part of the panel would more than pass the national-standard flame retardant test.
Building exteriors: Used for cladding on high rise buildings, bungalows, corporate offices, and commercial towers.
Building interiors: Used for interior decoration in homes, offices, and commercial spaces including wall paneling, ceiling designs, and room partitions.
Signage: Used for billboards, shopfront signage, direction signs, digital print signage, and display platforms.
Transportation: Used in the manufacturing of body parts of buses, trains, metros, airplanes, and marine vehicles.
Furniture: Used in the creation of furniture designs, wardrobes, kitchen cabinet surfaces, and other interior fixtures.
Industrial Uses: Applied in manufacturing units as casing materials for machinery, protective covering for equipment, and cleanroom applications.
Retail design: Used in the creation of retail store setups, kiosk designs, and interior display units.
Hospitality sector: Used for interior decorations, signage, and external cladding in hotels, resorts, and restaurants.
Healthcare sector: Used for cladding in hospitals, clinics, and health centers due to its easy-to-clean and durable surface.
Education sector: Used in schools, colleges, and universities for signboards, furniture, and internal partitions.
Sports and Recreation: Used in stadiums, gyms, and sports complexes for cladding, internal decorations, and signage.
Infrastructure: Used for cladding and signage in airports, railway stations, bus terminals, and ports.
The aluminum composite panels produced by our company can be processed and shaped using common woodworking and metalworking tools, including cutting, sawing, milling, punching, pressing, folding, and bending. This allows for accurate completion of various forms required by architectural decoration design, especially for shapes such as arcs, counter-arcs, small-radius corners, and internal and external corners. This level of versatility is unparalleled by other decoration materials.
1. Cutting: Cutting tool, electric saw, hand saw, ring saw, etc.
2. Slot Milling: After processing with an electric and portable
slot milling machine, the product can be manually bent into various
kinds of polyhedrons.
3. Corner Removing: After processing with a puncher and corner
removing machine, it can be combined in a trunk.
4. Welding: The product can be welded with plastic welding rods and
hot wind welders.
5. Corner Bending: After processing with a slot milling machine,
the product can be bent into various corners.
6. Bending: The product can be bent using 3-point or 3-rolling
machines.
7. Printing: The product can be printed with screen printing
plates.
8. Assembling: Rivet, nail, self-tapping screw, etc.
9. Punching: The product can be punched with an open puncher.