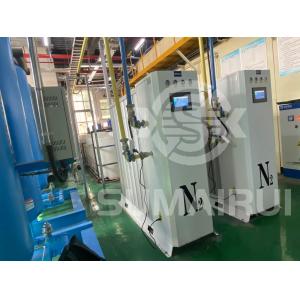

Add to Cart
OSL Series modular nitrogen generator for electronic industry with
40 cfm 99.99%-99.999% 120 psi packing machine
What Is a PSA Nitrogen Generator?
Pressure Swing Adsorption is a technology used for separating gas
species from a mix of various gases under pressure, depending on
the affinity for an adsorbent material and the species’ molecular
characteristics. This technology differs significantly from
cryogenic-distillation gas separation techniques. Specific
adsorptive materials, such as activated carbon or molecular sieves,
are used as a trap, adsorbing the target gas species at a high
pressure. Operating at near-ambient temperatures, the process
swings to low pressure, desorbing the adsorbed material.
How Do Industrial PSA Nitrogen Generators Work?
For this process, pressure swing adsorption relies on the principle
that under high pressure, gas tends to be attracted to solid
surfaces. Higher pressures result in more gas being adsorbed. When
pressure is reduced, adsorbed gas is then released (desorbed).
Pressure Swing Adsorption processes are often used to separate
gases from mixtures because different gases are attracted to
different solid surfaces more/less strongly. For example, if air
(gas mixture) passes under pressure through a particular vessel
containing an adsorbent bed of CMS (which attracts O2 more strongly
than it does N2), some or all of the oxygen will remain in the bed,
and gas exiting the vessel will then be enriched in N2. When the
bed reaches its capacity’s end to adsorb oxygen, it can regenerate
by reducing pressure, consequently releasing adsorbed oxygen. It
can then begin the cycle again and produce more high purity N2 gas.
Using two (2) adsorbent vessels allows for near-continuous
production of target gas. This technique also permits pressure
equalization, which is where gas leaving a depressurized vessel is
used to partially pressurize a second vessel. This common
industrial practice leads to significant energy savings.
Typical System Configuration (PFD)
System Specification
Sumairui Gas offers completely turn-key system designs, including
all components, elements, and design drawings. Our engineering
teams will work directly with you to design and install systems to
your exact specifications. Our full-service team is ready to answer
any questions you may have 24/7.
Technology
How Does a Pressure Swing Adsorption System Work?
Nitrogen PSA Generator Systems send air over a bed of adsorbent
material, which bonds with O2 and leaves a rich stream of nitrogen
gas to exit.
Adsorption separation is achieved by the following steps:
FEED AIR COMPRESSION & CONDITIONING
The ambient inlet air is compressed, dried by an air dryer,
filtered, all before entering the process vessels.
PRESSURIZATION & ADSORPTION
The pre-treated filtered air is then directed into a CMS-filled
vessel, where oxygen is adsorbed preferentially into the CMS pores.
This permits concentrated nitrogen, with adjustable purity as low
as 50 ppm O2, to stay in the gas stream until it flows out of the
vessel. The separation process interrupts the inlet flow (before
the full adsorption capacity of the CMS is reached) and finally
switches over to the other adsorber vessel.
DESORPTION
The O2-Saturated CMS is then regenerated by means of pressure
reduction, below the previous adsorption step. It achieves this by
using a pressure release system where exhaust/waste gas stream is
carefully vented from the vessel, typically through a
diffuser/silencer, then back into the safe surrounding atmosphere.
Regenerated CMS is now refreshed and can be used again for
generating nitrogen.
ALTERNATING VESSELS/SWING
Desorption and Adsorption should take place at equal time
intervals, alternately. This way, the constant generation of
nitrogen is be achieved by using two (2) adsorbers. As one is
adsorbing, the second is in regeneration mode. Constant switching
back and forth results in a controlled and continuous flow of
nitrogen.
NITROGEN RECEIVER
Continuous nitrogen product flow & purity is maintained by a
connected product buffer vessel which stores the N2 output. This is
designed for a pressure up to 150 psig (10 bar) and Nitrogen purity
up to 99.9995%.
NITROGEN PRODUCT
The resulting product is a constant stream of high purity, on-site
produced Nitrogen, and costs significantly below the standard price
of liquid/bottled gases.
The Benefits of an Onsite Nitrogen Generating System
Cost Savings
Factors like market cost and delivery location will impact what you
spend if you have nitrogen delivered to your facility. When you
shift to onside nitrogen generation, you can significantly reduce
these costs no matter where you are located. In fact, you can see a
return on investment in a little as nine to 24 months.
Increase Safety for Employees
Since your primary concern is your employee safety, onsite nitrogen
generation significantly reduces the risk of worker injury.
Handling nitrogen cylinders, tank leaks and exposure to liquid
nitrogen through delivery and unloading is 100% eliminated, thus
creating a safe and reliable system.
Reduce Impact on Environment
By having your own nitrogen generating system you reduce your
environmental impact as you no longer need to use heavy transport
trucks to deliver and replenish your tanks. You also increase
efficiency and improve your reputation in the industry as a company
that is environmentally conscious.
Efficient Time Savings
Industrial users who set up onsite nitrogen generation save time on
critical operations that use nitrogen. One of the biggest losses
for industrial users each year is operational downtime caused by
logistical issues with transporting nitrogen from vendor locations.
With an onsite nitrogen generating system, you have a 24-hour
supply of high-purity gas to run your processes.
Nitrogen Generator Applications
Food Packaging
Modified Atmosphere Packaging (MAP) with nitrogen and nitrogen-CO2
gas mixes are often used in the food packaging industry to preserve
perishable items by preventing spoilage, ensuring freshness,
maintaining flavour, and extending the product shelf life. Onsite
nitrogen generation is highly beneficial in the food packaging
industry to maintain a quality product. Food packagers can save
hundreds of thousands of dollars by having an onsite system
installed.
Beverage Storage, Transport, and Dispensing
Like the food industry, the beverage industry can also improve from
having onsite nitrogen generating systems. These systems make it
more efficient to transport beverages to end users such as juice
packagers, vintners, breweries, and other manufacturers of beverage
dispensing systems.
Onsite nitrogen generators are extremely efficient and
cost-effective for various industrial applications. By installing
an onsite system, all you need to focus on is maintenance, while
your investment pays for itself over time. We offer the following
nitrogen generator services
Maintenance Services
For help with installation, our team offers around-the-clock
service support. If you require maintenance for your existing
system, we will ensure that your nitrogen generator is running in
great condition, so you can get back to your operations.
For nearly three decades we have been helping our clients
significantly reduce their industrial nitrogen and oxygen costs by
utilizing leading-edge technologies such as onsite nitrogen and
oxygen generating systems. We displace the requirement of having to
purchase the gas. Instead, we sell our business clients the
technology and equipment they need to make their own gas on site.