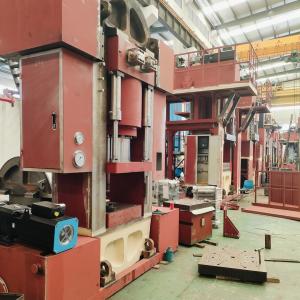

Add to Cart
A high-precision servo controlled cold and hot forging hydraulic
press with a servo electric pump is a device that uses a servo
motor to drive an oil pump and achieves cold and hot forging
processing of metal parts through a high-precision servo control
system.
Here are some detailed introductions of this type of hydraulic
press:
Composition structure:
1. Bow shaped frame: provides stable support.
2. Mobile board and mobile workbench: used for placing and fixing
metal parts.
3. Guiding column: Ensure the accuracy and stability of the
movement of moving parts.
4. Main oil cylinder: generates the pressure required for forging.
5. Hydraulic system: including servo electric pump, control valve,
etc., responsible for providing and regulating hydraulic power.
6. Servo motor: Accurately control the output flow and pressure of
the oil pump.
7. Electrical system: including controllers, frequency converters,
etc., to control motors and other electrical equipment.
8. Pressure sensors and displacement sensors (such as magnetic grid
rulers): Real time monitoring of pressure and displacement data,
feedback to the control system to achieve high-precision control.
Features and advantages:
1. High precision control: using high-precision displacement
sensors for detection, combined with servo adjustment, with high
repeatability accuracy, such as up to ± 0.03mm, and pressure error
can be controlled within ± 1%.
2. Easy to operate and flexible: pressure, speed, and position are
fully closed-loop digital displays and controls, which can be
programmed to meet the changing requirements of different processes
for speed and pressure. Each machine can be optionally equipped
with an infrared safety grating to effectively protect operators,
and can be used in conjunction with automatic production lines in
fully automatic production mode.
3. Energy saving and efficient: Compared to traditional hydraulic
presses, it can save 30% to 70% of electricity. There is no
overflow heating, and there is no flow when the slider is
stationary, so there is no hydraulic resistance heating. The heat
generated by the hydraulic system is generally 10% to 30% of that
of traditional hydraulic presses.
4. Fast response: The servo motor responds quickly and can
accelerate the speed changes during the forging process, improving
work efficiency. The working cycle can be several times faster than
traditional hydraulic presses, reaching 10/min to 15/min.
5. Low noise: During compression and return, the motor operates at
rated speed and emits lower noise than traditional hydraulic
presses. When the slider is stationary, there is basically no noise
emission.
6. High stability and durability: It reduces some complex circuits
in traditional hydraulic systems, simplifies the system structure,
and reduces the probability of failure. Meanwhile, due to the low
heat generation, the pollution of hydraulic oil is also minimal,
which is beneficial for extending the service life of the
equipment.
7. Easy maintenance: The simplification of the hydraulic system
reduces the strict requirements for hydraulic oil cleanliness,
lowering maintenance costs and difficulty.
working principle:
The main drive oil pump is driven by a servo motor, and the control
system precisely controls the speed and torque of the servo motor
based on set process parameters such as pressure, stroke, speed,
etc., thereby achieving precise adjustment of the output flow rate
and pressure of the oil pump. Pressure sensors and displacement
sensors provide real-time feedback on actual pressure and
displacement information, compare and correct it with set values,
form closed-loop control, and ensure high precision and stability
of the forging process.
In cold and hot forging processes, this hydraulic press can
flexibly adjust parameters such as pressure and speed according to
different metal materials and process requirements to achieve the
best forging effect. It is widely used in the fields of automotive
parts manufacturing, aerospace, mechanical processing, etc., and
can produce high-precision and high-quality metal parts.
High precision servo controlled cold and hot forging hydraulic
presses with servo electric pumps from different manufacturers and
models may have differences in specific parameters and performance.
When selecting, comprehensive consideration should be given to
factors such as production needs, process requirements, and budget.
At the same time, it is also necessary to pay attention to the
brand reputation and after-sales service of the equipment to ensure
its long-term stable operation and good user experience.
Partial configuration table of hydraulic power machine
project | YRK-2000SD | YRK-2500SD | YRK-3000SD | YRK-3500SD | YRK-4000SD | YRK-5000SD |
Main oil cylinder nominal force | 20000 KN | 25000 KN | 30000 KN | 35000 KN | 40000 KN | 50000 KN |
Maximum working pressure of the main oil cylinder | 80 Mpa | 80 Mpa | 80 Mpa | 80 Mpa | 80 Mpa | 80 Mpa |
Maximum travel of the activity crossbeam | 250 MM | 300 MM | 300 MM | 350 MM | 350 MM | 450 MM |
Oil pump type | single pump | single pump | single pump | dual pump | dual pump | dual pump |
Specifications:
Description | |
Small tonnage hot and cold forging steel wire winding hydraulic press | |
Purpose: This equipment is suitable for cold (warm) forging and extrusion forming processes of precision metal parts made of aluminum and copper materials. | |
Advantage: safe operation. | |
Operator: 1 person. | |
Motor Power(KW) | 12 |
Rated Voltage(V) | 380 |
Effective area of workbench (left and right * front and rear mm) | 1050*1050 |
Ifting speed of movable beam (mm/s) | Down: 240 |
Ifting speed of movable beam (mm/s) | Pressurized: 18/30 |
Ifting speed of movable beam (mm/s) | Return trip:240 |
Closed height (mm) | Max: 900 |
Closed height (mm) | Min: 550 |
order number | ts | name | quantity | place of production |
1 | SCR-160 | Tuning module | 4 block | |
2 | WRNK-130 Φ5mm | thermocouple | Four | Zhaoqing, Guangdong |
3 | AI518E3JO | Intelligent digital display power control temperature control table | One | Xiamen udian |