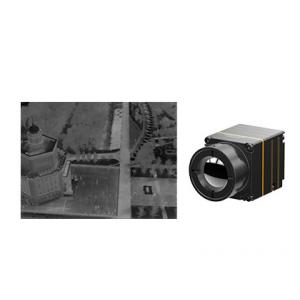

Add to Cart
The iTL612R infrared camera core integrates 640x512 / 12μm wafer
level package (WLP) infrared thermal detector. It is an uncooled
LWIR radiometric thermal imaging module for drones with spectral
range from 8 to 14μm.
iTL612 thermal camera module features in sharp and crisp image
presentation, compact size and low cost. Oriented for fully
optimized SWaP, iTL612R uncooled thermal module provides a reliable
solution for infrared system integration with limited space. Its
compact structure has reached top level of the same specification
module. It also has an optional thermographic function with
measurement range from -20℃~550 ℃ for industrial temperature
measurement.
The iTL612 thermal module is specially developed for the field of
Predictive Maintenance, Photovoltaic Inspection, Environmental
Protection, Scientific Research, Aerial Photography, Police
Investigation, Relief & Rescue, Forest Fire Prevention, Urban
Safety etc.
Compact & Lightweight Design
• Size: 21mm×22.3mm×27.3mm (with 9.1mm lens)
• Weight: 20.8g±1.5g (with 9.1mm lens)
• Low power consumption as low as 0.7W
Clear Image & Accurate Radiometry
• Brand new image process algorithm: NUC/3DNR/DNS/DRC/EE
• Support Windows/Linux/ARM SDK
• Support regional, point & isotherm temperature measurement
Various Interfaces for Easy Integration
• DVP/LVDS/USB2.0 interfaces, RAW/YUV image data output, serial
port control
Model | iTL612/R |
IR Detector Performance | |
Sensitive Material | Vanadium Oxide |
Resolution | 640×512 |
Pixel Size | 12μm |
Spectral Range | 8~14μm |
Typical NETD | ≤40mk |
Image Processing | |
Frame Rate | 30Hz |
Start-up Time | 5s |
Digital Video | RAW/YUV/BT656 |
Image Algorithm | Non-uniformity Correction (NUC) 3D Noise Reduction (3DNR) De-noise (DNS) Dynamic Range Compression (DRC) Edge Enhancement (EE) |
Image Display | Black Hot/White Hot/Pseudo Color |
PC Software | |
ICC Software | Module Control & Video Display |
Electrical Specifications | |
Standard External Interface | 30Pin_HRS: DF40C-30DP-0.4V(51), (HRS, Male) |
USB Expansion Board | Type-C |
Communication Interface | RS232-TTL/USB2.0 |
Digital Video Interface | CMOS8/USB2.0 |
Supply Voltage | 3.3V±0.1V VDC |
Typical Power Consumption | 0.7W |
Temperature Measurement | |
Operating Temperature Range | -10°C~+50°C |
Temperature Measurement Range | -20°C~+150°C, 0°C~550°C; Support Customization and Expansion |
Temperature Measurement Accuracy | Greater of ±3°C or ±3% (@23℃±3℃) |
Regional Temperature Measurement | Support Maximum, Minimum and Average Value of the Output Regional Temperature |
SDK | Support Windows/Linux/ARM; Achieve Video Stream Analysis and Conversion from Gray to Temperature |
Physical Characteristics | |
Size (mm) | 21×22.3×27.3 (With 9.1mm Lens) |
Weight | 20.8g±1.5g (With 9.1mm Lens) |
Environmental Adaptability | |
Operating Temperature | -40°C~+70°C |
Storage Temperature | -45°C~+85°C |
Humidity | 5%~95%, Non-condensing |
Vibration | 5.35grms, 3 Axis |
Shock | Half-sine Wave, 40g/11ms, 3 Axis 6 Direction |
Certificates | ROHS2.0/REACH |
Optics | |
Optional Lens | Fixed Focus Athermal: 9.1mm |
The iTL612/R thermal imaging module can be integrated into UAV
payloads and wearable devices so that is widely used in fields of Predictive Maintenance, Photovoltaic Inspection, Environmental
Protection, Scientific Research, Aerial Photography, Police
Investigation, Relief & Rescue, Forest Fire Prevention, Urban
Safety etc.
1.What is infrared thermal imaging?
Infrared thermal imaging is a method of using infrared radiation and thermal energy to gather information about objects, in order to formulate images of them, or get temperature information of the objects, even in low visibility environments.
2.How does Infrared Thermal Imaging Work?
Infrared thermal imaging system is a passive non-contact detection
and identification of infrared technology. It focuses the infrared
radiation of the scene on the focal plane array infrared detector
through the infrared optical system that can pass through infrared
radiation. The thermal detector converts the radiation signal of
different intensity into the corresponding electrical signal, and
then through amplification and video processing, forms the infrared
image that can be observed by the naked eyes.