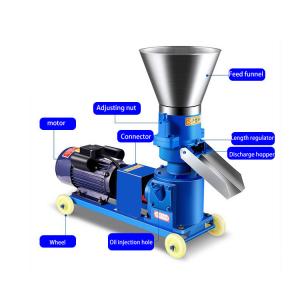

Add to Cart
Feed pellet machine, widely used in large, medium and small aquaculture, grain feed processing plants, livestock farms, poultry farms, individual farmers and small and medium-sized farms, farmers or large, medium and small feed processing plants.
Debug program editor broadcast
1. First of all, we should understand the technological process of
pellet feed production line and the function of each specific
equipment in the technological process;
2. Before debugging, check the operation of a specific equipment
one by one, and understand the crushing particle size of the
crusher that matches the die hole of the granulator used. The
particle size of raw materials should be fine, but not too fine,
preferably coarse, medium and fine.
A, particle size above 3.35mm ≤1%
B. Particle size above 2.0mm ≤5%
C, more than 1.0mm particle size about 20%≥>
D. The particle size above 0.5mm is about 30%
E. The particle size below 0.25mm shall not be less than 20%
F. The particle size above 0.25mm is about 24%
3, before debugging to wash the warehouse, remove the stones and
welding slag and other sundries left during installation;
4, before debugging, check whether the steam pipeline system used
has good decompression function and hydrophobic function, in order
to ensure the drying and saturated quenching and tempering steam
required for granulation, and to ensure that there is always
0.058-0.4mpa steam after the pressure reducing valve;
5, before start the pelletizer should adjust the distance between
the roller and ring die, generally for the rotating ring die when
the roller turn not turn (i.e., roller and ring die spacing is 0.1
~ 0.4 MM is best), don't make the ring die and a tuning roller
spacing is too small, lead to direct friction, such not only can
accelerate the ring die and roller friction losses, but also reduce
the production of the unit output;
6. When starting the pelleting equipment, the feeding amount should
not reach the maximum instantly. It should take 5-10 minutes to
reach the ideal feeding amount (i.e. the motor current value in
normal production is 85~95% of the rated current value) by adding a
little material and a little steam at the same time [1].
Prevention of undesirable phenomena
1, the particles have axial crack or radial crack phenomenon, and
the pulverization rate is high, the output is low, leading to the
reason of this phenomenon can not reach the adjustable tempering
temperature, the material curing degree is poor, should improve the
tempering temperature, increase the amount of steam when tempering;
It may also be that the cutter position is far away and blunt, so
that the particles are short or torn rather than cut;
2. The particle surface is not very smooth, and the pulverization
rate is high. It may be that the compression of the ring mode is
relatively small, so the compression hole should be increased. Ring
mode compression;
3, the particle surface is smooth, but the hardness is too high,
may be the ring modulus compression ratio is large, should reduce
the ring modulus compression ratio;
4, when the particle moisture is high, the production output is
low, and often appear blocking machine phenomenon, which may be
that the pressure reducing valve can not play the decompression
effect or the trap can not play the role of hydrophobic, should
adjust the pressure reducing valve, so that the steam pressure into
the conditioner is 0.1-0.4mpa, and the trap can play the role of
hydrophobic. The quenching and tempering temperature can also be
increased accordingly, because the increase of temperature is
conducive to the improvement of the degree of maturation of the
material. Generally, the moisture content of the material increases
about 1% when the temperature increases 11℃.
5, particle length is different, should adjust the cutter distance
or adjust the material deflection scraping position;
6. Where the current deviation of the two motors is large, the belt
tension of the two motors should be adjusted to make the tension as
consistent as possible [1].