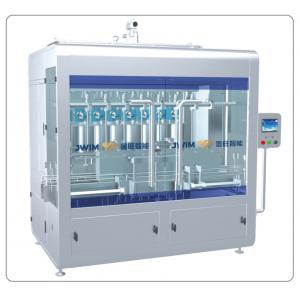

Add to Cart
High Automatic Jar Filling Machine Linear Piston Filling Machine (1L-5L) 6/8/10/12 Filling Heads
Automatic linear piston filling machine is an extremely flexible
piston filler capable of filling accurately and rapidly a wide
variety of products from low viscosity liquids to high viscosity
paste or cream with or without chunks or particulates. Widely used
in the food industry(e.g., paste filling machine, butter filling
machine, jar filling machine, ketchup filling machine, honey
filling machine, edible oil filling machine, sauce filling machine,
etc); household product industry(e.g., shampoo filling machine,
liquid soap filling machine, liquid detergent filling machine, hand
wash filling machine, etc), personal care industry(e.g., cream
filling machine, lotion filling machine, gel filling machine,
perfume filling machine, etc); Chemical industry(e.g., grease
filling machine, lubricant filling machine, etc); pharmaceutical
industry(e.,g ointment filling machine, e-liquid filling machine,
etc).
Automatic linear piston filler is designed for completely
automatic, multiple positions, inline dispensing of liquids and
pastes in volume ranging from 50ml to 1000m per cycle. Available in
6, 8, 10,12, and 16 nozzle configurations to match specific
production requirements, the Dual lane option is available to
increase production by 100% while preserving valuable line space.
Linear piston liquid filling machinery is manufactured with a 304
stainless steel frame, It comes standard with PLC control and touch
screen HMI ensuring reliable, repeatable control with minimal
operator intervention, Precision bored, heavy-walled metering
cylinders dispense product at accuracy up to +/- 0.2%,
High-precision, the servo motor is driven screw movement faster and
more precise than the pneumatic system, food-grade stainless steel,
and plastics for sanitary operations or use, anodized aluminum
components, plus many more features available with motorized
conveyor and indexing package for integrated container handling and
positioning, No container/No fill feature detects missing or
mispositioned containers to prevent waste and product spillage.
Unique variable, separate speed control, and actuator of a
dual-stage fill provide precise “no-spill” control for top-off
applications or filling difficult products.
Empty bottles are staged on the main drive conveyor prior to
entering the piston filler. Bottles enter the filler and are
counted by optical sensors to ensure the correct numbers of bottles
are in position. Once in place, bottles are locked in position by
the pneumatically operated bottle clamping mechanism. This ensures
bottles are located correctly under each filling head to minimize
under or over-fills. The filling process begins as a series of
stainless steel valves descend into the bottles for fast, accurate,
and consistent filling. After target volume is achieved, the
out-gate cylinder withdraws itself from its position and allows the
filled bottles to go further on the conveyor for the sealing
operations.
Applications
1 | Number of filling | 4/6/8/12 filling heads |
2 | Applicable Bottle | Round bottle: Φ80-140mm Height 140-340mm Flat Bottle:L 80-200mm W80-140mm H140-340mm |
3 | Filling Volume | 1000-5000mL |
4 | Filling Precision | ±5g(1000mL) ±8g(5000mL) |
5 | Inlet Height | 2550mm |
6 | Inlet Diameter | Dn40 |
7 | Filling Nozzle Dimension | Φ26mm |
8 | Minimum Bottle Neck Inner Dimension | ≥Φ30mm |
9 | Air Pressure | 0.6-0.8MPa |
10 | Power Source | ~380V 50Hz/2.7KW |
11 | External Dimension | 2365×1600×2750mm(L×W×H) |
12 | Gross Weight | ~2000Kg |
13 | Optional weighing feedback, maximum measuring range 6 kg, if the specific gravity of materials ≥1.2, then according to the actual situation custom |