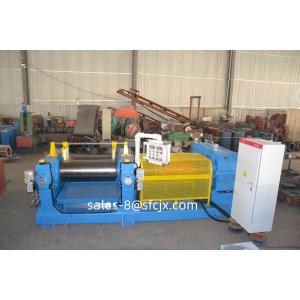

Add to Cart
Business Manager
sales-8@sfcjx.com
Drilled Rolls:The rolls can be drilled with holes to allow for
better mixing and dispersion of additives. This configuration
enhances the distribution of fillers and other ingredients within
the rubber matrix
Grooved Rolls: The rolls can be grooved with parallel or helical
patterns. Grooved rolls increase the mixing efficiency by providing
additional shear and kneading action, resulting in improved
dispersion and reduced mixing time
Automatic mixing programs can be customized to collect and log data
during the mixing process, including mixing parameters, temperature
readings, and other relevant information. Customization options may
include data analysis tools and reporting capabilities to analyze
trends, monitor process performance, and ensure quality control
Variable Roll Speeds: The machine allows for independent control of the roll speeds. This feature enables precise adjustment of the mixing process, such as the shear rate and residence time, to achieve the desired level of blending and dispersion. Different roll speeds can be employed to optimize the mixing efficiency for various types of rubber compounds.
Temperature Control: Rubber mixing machines often include provisions for temperature control. The rolls can be heated or cooled to maintain the rubber material at the desired temperature range. Heating the rolls softens the rubber compound, making it more malleable and facilitating the blending process. Cooling the rolls can be useful for heat-sensitive rubber compounds or to prevent excessive heat buildup during extended mixing sessions.
Customization Options: we often offer customization options to meet specific production requirements. This may include the choice of roll diameter, surface texture, roll material, and additional features like pneumatic or hydraulic roll adjustments, automated batch feeding systems, or discharge mechanisms.
Open Rubber Mixing Mill: The machine features a 16" open rubber
mixing mill, which refers to the size of the mill rolls. The open
mill design allows for easy access to the rolls, facilitating the
feeding of rubber materials, additives, and fillers during the
mixing process. It also enables efficient cooling and discharge of
the mixed rubber compound
Customization of Size: The machine can be customized to accommodate
different roll sizes, such as 16", 18", or other specific
dimensions, based on the production requirements. The size of the
mill rolls affects the production capacity and the amount of rubber
compound that can be processed in each batch.
The technical parameters for some models rubber Kneader Mixer:
Model | XK-400 | XK-450 | XK-560 | XK-610 | XK-660 |
Working diameter of rollers (mm) | Ф400 | Ф450 | Ф560/Ф510 | Ф610 | Ф660 |
Working length of rollers | 1000 | 1200 | 1530/1830 | 2000 | 2130 |
Linear speed of front and rear roller | 1:1.27 | 1:1.27 | 1:1.2 | 1:1.29 | 1:1.24 |
Capacity per batch | 18~35 | 25~50 | 50~100 | 90~120 | 130~165 |
Motor power (kw) | 37 | 55 | 90/110 | 160 | 185/250 |
Overall size L*W*H | 4250*1850*1870 | 5200*1800*2000 | 6500*2300*2640 | 7500*2500*2640 | 7600*3400*2500 |
Weight (kg) | 7000 | 10000 | 20000 | 28000 | 47000 |