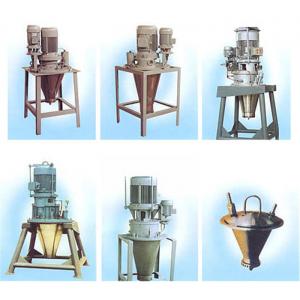

Add to Cart
Atomizer
Description
The formation of sprays having the required droplet size distribution is vital to any successful spray dryer operation so that powder specifications can be met. Atomization is a high technology area where Niro has played a central role in the development and use of nozzles and rotary atomizers in spray drying.
The formation of sprays having the required droplet size distribution is vital to any successful spray dryer operation so that powder specifications can be met. Atomization is a high technology area where Niro has played a central role in the development and use of nozzles and rotary atomizers in spray drying.
Three types of atomizers are used in industrial drying:
Rotary atomizer, atomization by centrifugal energy
Pressure nozzle, atomization by pressure energy
Two-fluid nozzle, atomization by kinetic energy
The choice of atomizer depends upon the properties of the feed and the dried product specification. In cases where more than one atomizer type is suitable, the rotary atomizer is generally preferred due to it's greater flexibility and ease of operation.
The advantages include:
Handling of high feed rates without need for atomizer duplication
Handing of abrasive feeds
No blockage problems
Low pressure feed system
Ease of droplet size control through wheel speed adjustment
Product details
Description of the three kinds of atomizers:
1. Rotary atomizer: Its function is to increase the specific surface area of the feed and quickly evaporate water. The slurry must have a certain degree of fluidity, and the atomization object is slurry, high paste fluid, suspension or solution.
2. Pressure atomizing nozzle (diaphragm pump or high pressure pump directly pressurize the liquid slurry, and then disperse and atomize the material liquid through the pressure nozzle, and spray the dispersed mist droplets into the hot air fluid with the help of pressure. Drying is carried out in the middle. Because the nozzle aperture is small, the pressure is released instantly after the high-pressure stream passes, so that the slurry obtains a dispersed atomization treatment, and rapid mass heat exchange occurs through contact with hot air).
3. Nozzle atomizer: It uses the kinetic energy stored by compressed air to release instantly at the material orifice, so that the material flow is well impacted and dispersed and cut, and the feed is atomized, and the fine mist droplets fully contact with high temperature air in the tower to produce mass-heat exchange, and finally a dry powder product is obtained.
Brief introduction of configuration of a rotary atomizer
The Rotary Atomizer is the pivotal part of the centrifugal spray drier, and its modular organization is compact, reliable and durable, in addition its maintenance is especially convenient.
1) Drive gear
The tr5ansmission method of this type of Rotary Atomizer is gear drive , the primary motor connects up the gearbox by elastic shaft coupling, and then the gearbox makes principal shaft rotate in a certain high speed range by gear speed regulation.
2) Atomizing system
Feed liquid passes through the liquid pump and enters into the feed pipe, then descends into the feed liquid distribution plate, and flows into the inner chamber of the spray disc connected with the principal shaft cone through empty eyelets evenly distributed in the chamber of the feed liquid distribution plate. Under the force of centrifugal pull, feed liquid is sprayed out as the shape of tiny atomizing liquid drop, and then forms mist.
3) Lubrication system
Large-sized Rotary Atomizer has two gear oil pumps working synchronously, medium-sized and small-sized Rotary Atomizer has one gear oil pump, and every oil pump has one motor as drive. The oil pump aspirates out oil box’s lube through the oil suction pipe and transits it into the gearbox through the condenser, lubricates high gear by the oil injection nozzle, and lubricates the rolling bearings, which are in the gearbox and on the principal shaft, by oil mist produced with the rotate of the gear.
4) Oil way safety alarm device
The Rotary Atomizer can’t work under oil shortage condition. Therefore, the safety alarm device is fixed on large-sized and medium-sized injection cup’s oil way and all generic-sized injection cups have been equipped with the electric contact pressure gauge to control and protect the safety work of oil way. When the oil mass is under the oil level line or there are some failures in the oil pump and pipeline, then it can’t normally work, and the alarm system will give an alarm automatically, cut the primary motor synchronously, and then the injection cup will stop operating.
5) Sealing device
The lube of The Rotary Atomizer is sealed by the oil retaining sleeve on the principal shaft and the oil retaining tube on the seat of direct bearing. (See figure B) In order to ensure its sealing performance, every time replace the main bearing, need to renew the oil retaining sleeve synchronously, and cannot reuse the oil retaining sleeve disassembled. When the oil retaining pipe leaves factory, it has been sealed and fastened, and has been tested whether it leaks oil. It is unnecessary to disassemble this part during normal mend and maintenance, avoiding oil leak.
This machine sealing device can satisfy normal needs, if customers have some special demands, you can add a set of air sealing device.
6) Oil cooler system
Due to drying chamber comparatively high inner temperature, in order to ensure The centrifugal spray fixed on the top of drying tower to work normally, control the temperature of lube under 70℃, therefore there is a stainless steel oil cooler system fixed in all kinds of The Rotary Atomizer Use water supply or water pump to input water into the oil cooler, the water inlet pipe should be connected with the lower pipe coupling. The water outputs from another pipe coupling automatically after cycling, and water inflow is proper for controlling the water temperature under 60℃. If customers have any demand, it can be added an air-cooling unit.