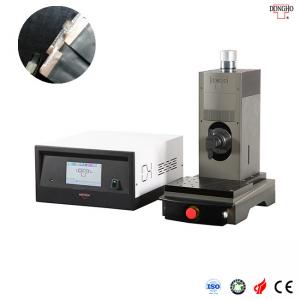

Add to Cart
Ultrasonic Metal Welding Equipment For Aluminum Copper And Nickel Welder
Ultrasonic welding of copper, aluminum, and other non-ferrous
metals is a mature bonding process, which is widely used in
automobile and consumer electronics fields. Due to the rapid
development of new energy electric vehicles and the increasing
demand for lithium-ion batteries, the application of ultrasonic
welding of copper foil and aluminum foil has increased
significantly.
The three main stages of ultrasonic metal welding to form molecular
bonds are:
1. The relative movement caused shear and plastic deformation --
initial plastic deformation -- on the rough convex features on the
connecting surface.
2. Ultrasonic vibration leads to oxidation layer (or contaminants)
dispersion and further plastic deformation of the raised features
on the connectors. This leads to increased metal-to-metal contact
areas and the formation of welding zones, also known as
microworlds.
3. Further ultrasonic vibration will cause the contact surface to
increase, which will increase the welding area.
The decisive advantage of ultrasonic metal welding is "cold" welding, where joints are formed at temperatures well below the metal's melting point. The temperature is only about 1/3-1/2 of the melting point of the metal (the recrystallization temperature during annealing), which is a solid and solid press welding process.
Technical Parameters:
Product Name | Ultrasonic Metal Welding Machine |
Model | MPL-50 |
Frequency | 20KHz |
Power | 2400W |
Welding Force | 1200 Newton Max. |
Control Voltage | 24V |
Welding Stroke | 50mm |
Welding Ranges | 30-100 mm2 |
Advantages of the ultrasonic metal welding equipment:
1, Good electrical conductivity after welding, very low or almost
zero resistivity.
2, The ultrasonic metal welding machine is close to cold
processing, the workpiece is not annealing, no oxidation trace.
3, High fusion strength.
4, Ultrasonic metal welding machine for welding metal surface
requirements are low, oxidation or electroplating can be welded.
5, Ultrasonic metal welding machine welding time is short, do not
need any flux, gas, solder.
6, The welding process does not need water cooling and gas
protection, welding parts do not deformation.
Application:
New energy vehicle industry: The pole lug welding on the lithium battery pack of electric cars
is popular now, as well as the welding of wiring harness and wiring
harness inside the car, and the welding of wiring harness and
terminal.
The medical profession. The most typical application is pin welding
on integrated circuits in medical equipment. The process does not
require glue or adhesives, just the bonding of the body material.
Such as pacemakers used to treat patients and sensors implanted in
the body. In addition, ultrasonic welding is widely used in the
manufacture of intravenous catheters, blood/gas filters, dialysis
machines, valves, and filters.
Electronics and computer industry: Used in chips, motors, capacitors, flash memory, microprocessors,
transformers, and other products. The welding process combines thin
metal, usually aluminum or copper, with thick material to
seamlessly connect wires and circuits. It can effortlessly connect
circuits on a circuit board, making it ideal for the smartphone and
computer industries.
Space industry: When making engine parts, non-ferrous metal materials such as
aluminum are welded to steel. After welding, the components have
high drawing strength, precise size, and a beautiful appearance. It
can also meet the requirements of sealing performance and impact
resistance of closed chamber after welding.
Refrigeration industry: Copper pipes have been used as refrigeration and air-conditioning
cooling system components. Because copper was expensive, aluminum
tubes were used instead. However, regardless of whether copper or
aluminum tubes are used, ultrasound can be used for sheet welding
or sealing.