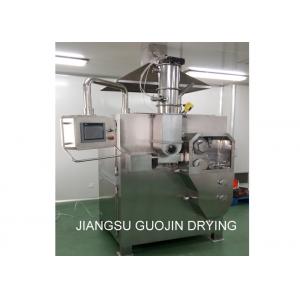

Add to Cart
DRG Series Dry Roller Granulator
The dry granulator adopts continuous feeding and discharging, integrates the functions of extrusion, crushing and granulation, and directly presses powdery materials into granules. It is especially suitable for granulating materials that are wet, hot, easy to decompose, fail or agglomerate. It has been widely used in pharmaceutical, food, chemical and other industries. In the pharmaceutical industry, granules made by dry granulator can be directly tabletted or filled into capsules.
Roller Extruding System
Mill System
According to the requirements of grain collection, the whole grain net with different apertures can be selected, and the gap between the whole grain wheel and the whole grain net can be adjusted. According to the property of the material, spiral or hob grading wheels can be selected. The whole mesh can also be equipped with woven mesh or punched mesh plate.
Discharging System
An aggregate port and a discharge port are arranged. The aggregate port collects a small amount of uncompressed raw materials in the triangle area. The discharge port is equipped with a vacuum discharge assembly with a respirator to facilitate vacuum delivery to the screener.
Product Features
The whole machine is designed into two major parts such as machine body inside part and the work part outside the operation panel. All driving parts and auxiliary facilities are designed inside the machine. The work part that contact material is set outside the operation panel. The middle part is isolated by multiple sealing. The work part works under a fully closed status, and al parts that contact materials are convenient to assemble, disassemble and clean, so as to effectively avoid dust leakage, lower pollution possibilities and reduce cleaning area, fully meeting GMP requirements for medicine production.
3.1. functions in one unit, These are compression, crushing and milling.
3.2. Simplified process to obtain highly stable granules. No water or other liquid is added and no need drying, so the loss of active ingredients due to decomposition can be eliminated.
3.3. Pressure rollers with a water cooling system;
3.4. Overall modular design, compact structure, better space utilization;
3.5. The power area is separated from the work area to prevent cross contamination;
3.6. Horizontal feeding structure, exposed installation of extrusion system, easy to clean and maintain;
3.7. Meet GMP requirements
Technical Parameters
Model | DRG-5 | DRG-15 | DRG-50 | DRG-100 | DRG-200 |
Production capacity(kg/batch) | 5 | 15 | 50 | 100 | 200 |
Feeding motor power(kw) | 0.37 | 0.55 | 0.75 | 1.5 | 4 |
Extruding motor power(kw) | 0.55 | 0.75 | 1.5 | 2.2 | 5.5 |
Granulating motor power(kw) | 0.37 | 0.37 | 0.55 | 0.55 | 1.5 |
Oil pump motor power(kw) | 0.55 | 0.55 | 0.55 | 0.55 | 0.55 |
Chilled water power(kw) | 2.2 | 2.2 | 2.2 | 2.2 | 2.2 |
Weight of main machine(kg) | 500 | 700 | 900 | 1100 | 2000 |
Overall dimensions(LxWxH)(mm) | 600*750*900 | 800*950*1200 | 1100*1350*1650 | 1200*1350*1800 | 1210*1530*1950 |
Product Show
electrical, steam, natural gas or other