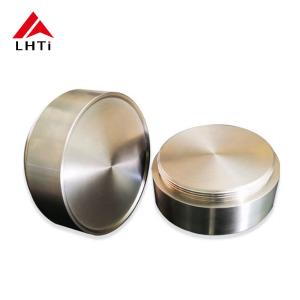

Add to Cart
In the rapidly advancing field of medical technology, the demand for high-quality materials is paramount. Among these materials, Grade 5 and Grade 7 titanium sputtering targets stand out for their exceptional properties and versatility. These high purity PVD (Physical Vapor Deposition) titanium sputtering targets are specifically designed to meet the rigorous standards required in medical applications. Their unique characteristics not only enhance the performance of medical devices but also ensure safety and reliability, which are critical in healthcare settings.
Grade 5 titanium, also known as Ti-6Al-4V, is one of the most commonly used titanium alloys due to its excellent strength-to-weight ratio and corrosion resistance. This alloy contains 90% titanium, 6% aluminum, and 4% vanadium, making it exceptionally strong yet lightweight—an essential feature for medical devices like implants and surgical instruments. The addition of aluminum and vanadium enhances its mechanical properties, allowing it to withstand the demanding conditions often found in medical environments. The ability to customize these sputtering targets ensures that manufacturers can create coatings tailored to specific medical applications, thus optimizing device performance.
Grade 7 titanium, or Ti-0.2Pd, is another alloy that provides unique advantages in medical applications. It incorporates palladium, which improves its resistance to corrosion, particularly in acidic environments. This property is particularly beneficial for devices exposed to bodily fluids or harsh sterilization processes. By utilizing high purity Grade 7 titanium sputtering targets, manufacturers can produce thin films that not only enhance the longevity of medical devices but also minimize the risk of adverse reactions when in contact with biological tissues. The customization capabilities of these targets allow for precise adjustments in composition and thickness, catering to the specific needs of various medical applications.
The high purity levels of Grade 5 and Grade 7 titanium sputtering targets—often exceeding 99.5%—play a critical role in ensuring the quality of the deposited films. Impurities can compromise the integrity and performance of coatings, leading to potential failures in medical devices. By selecting high purity materials, manufacturers can significantly reduce contamination risks, resulting in coatings that are both reliable and durable. This is particularly crucial in applications such as implants, where biocompatibility is essential for patient safety. The stringent quality control processes used in the production of these sputtering targets further guarantee that they meet the highest industry standards.
The versatility of Grade 5 and Grade 7 titanium sputtering targets extends beyond medical devices; they are also used in a variety of other applications. For instance, the semiconductor industry relies on these materials for the manufacturing of electronic components, which are vital for medical imaging systems and diagnostic tools. Additionally, their use in decorative coatings can improve the aesthetic appeal of medical equipment while also providing functional benefits, such as enhanced antimicrobial properties. This dual functionality makes high purity titanium sputtering targets an invaluable resource across multiple sectors, particularly in the quest for advanced medical technologies.
One of the standout features of these sputtering targets is their engineered microstructure. With finely controlled grain sizes, often less than 20 micrometers, these targets facilitate the production of films with superior adhesion and mechanical properties. This fine microstructure not only enhances the durability of the coatings but also improves their resistance to wear and environmental stressors. In the medical field, where devices are frequently subjected to rigorous use and sterilization procedures, this level of durability is crucial for ensuring long-term functionality and patient safety.
Moreover, the competitive pricing of Grade 5 and Grade 7 titanium sputtering targets makes them an attractive option for medical manufacturers looking to balance cost and quality. As the demand for advanced medical devices continues to rise, finding affordable yet high-quality materials becomes increasingly important. These sputtering targets provide a cost-effective solution without compromising on performance, enabling manufacturers to innovate and expand their product offerings. This financial viability encourages ongoing research and development, which is vital for keeping pace with advancements in medical technology.
Looking ahead, the future of Grade 5 and Grade 7 high purity titanium sputtering targets appears promising. Advances in material science and manufacturing processes are likely to yield even more refined and specialized sputtering targets. The integration of cutting-edge technologies, such as nanotechnology, could pave the way for coatings with enhanced properties, such as improved biocompatibility and targeted drug delivery systems. Such innovations could revolutionize the medical industry, leading to the development of safer, more effective medical devices that improve patient outcomes.
In conclusion, Grade 5 and Grade 7 high purity PVD titanium sputtering targets play a crucial role in the advancement of medical technologies. Their exceptional properties, coupled with customization options, make them ideal for a wide range of medical applications. As the industry continues to evolve, these sputtering targets will remain integral to the development of innovative solutions that enhance the safety, reliability, and effectiveness of medical devices, ultimately improving patient care and outcomes.
Detailed images
Factory
Package & Delivery:
Wrap the ti target material with pearl cotton and put it in a wooden box. Our reasonable packaging method can avoid the target materials from colliding with each other during transportation, and can also prevent the impact of external goods on the product, and ensure that the product is delivered after delivery Integrity.
---1. The sealed packaging,then put in the Carton cas or standard standard plywood case.
---2.Using exclusive custom carton with customer logo, each individual packaging, to help buyers direct sales.
---Accept customer requirment
Make sure that each package is tailor-made for you.ensure when you get the goods no damaged.