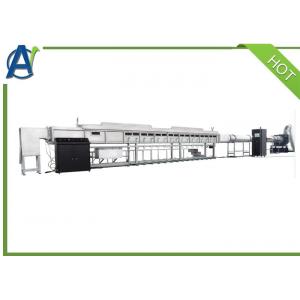

Add to Cart
1.The Steiner Tunnel Tester is made of stainless steel .The internal dimensions of the combustion chamber is 305mm x 451mm and long 7.6m with
firebricks laying which has satisfactory insulation property.
2.All internal fixtures are stainless steel which is rust resistant and
corrosion resistant.
3.A double-deck quartz glass observation window is used to observe the
position of flame spreading.
4.The height of the Steiner Tunnel Combustion Chamber is suitable for personnel to see the burning state ,sampleinstallation adjustment .
5.The overall design of the combustion chamber cover is made of stainless
steel and is equipped with heat-resistant and thermal insulation
material.
6.Steiner Tunnel Chamber is equipped with hoisting hook device.
7.The sample holder is equipped with cooling water circulation support bracket, which is resistant to high
temperature.
8.Steiner Tunnel chamber is equipped with 304 stainless steel sealed sink.
9.Dual burner distance from air inlet is 1320mm.
10.The exhaust pipe is made of stainless steel which is good looking and
corrosion resistant.
1.Two station lift at the same time. Computer control ensures
smooth lifting.
2.Suspension Hardware can be moved up and down,left and right which
is convenient for sample installation and commissioning.
3.Equipped with safety protection platform, convenient for sample
installation and commissioning.
1. The 10kV spark igniter is equipped with a safety cease-fire
device.The igniter is automatically positioned through the lever
connected to the closing mechanism.
2. The combustion heat of the burner is automatically controlled by
the gas flow system. The reading accuracy is 1%.
3. The heat output of the burner can be automatically controlled by
computer. Equipped with Japanese mass flow controller.
4. Gas flow valve control system to avoid leakage caused by
electromagnetic valve failure, resulting in explosion risk.
5. Frequency fan automatically controls wind speed inside the flue,
fan power 3KW, voltage 380V
6. Gas pressure gauge and pressure regulating valve to control gas
pressure accurately.
7. Imported gas flow control valve to control gas flow accurately
1. Smoke Density Test:smoke density is measured by incandescent
light system.Color temperature 2900±100K;The current fluctuation
range is + 0.5%;Linear output of smoke density value;With time
compensation function.
2. The lens converts light into 20mm parallel beams; d/f < 0.04.
3. Detector:The spectral distribution corresponds to CIE;The
accuracy of the chromatic standard function is + 5%;Thelinearity of
output is less than 3% of transmittance or 1% of absolute
transmittance.;The response time of system 90% is no more than 3S
4. The thermocouple is K type armored thermocouple, 0.5mm diameter;
the temperature accuracy is 0.5 degrees.
5. Pressure sensor range 0~100pa; accuracy is + 2pad;The response
time of pressure sensor 90% is 1s.
6. Environmental pressure accuracy of + 200Pa
7. System record time is at least 3S
8. System time recording accuracy 0.1s
9. Computer real-time display of smoke density generation curve
10. Option:The system is equipped with a camera system to observe
the experimental process and record the characteristics of the
burner residue after the implementation and combustion of the
sample.
1.Light source: 0.5W helium neon laser imported from the USA
2.Photoelectric receiver imported from the USA:wavelength range
350-1100nm;Peak value corresponding: 0.65A/W;Maximum output
current: 100mA;Gain control 70dB.
3.The Thorlabs filters (imported from the USA) to make smoke
density testing more accurate.
4.Steiner Tunnel Combustion Chamber is equipped with compensation
photoelectric detection system, effectively preventing light source
fluctuation interference.
Pipe exhaust capacity:
1. Delta inverter accurately controls flue gas velocity.
2. Smoke exhausting ability: Measurement of wind pressure and wind
speed with pitot tube and imported micro pressure transmitter.
3. Differential pressure transmitter:Measurement range 0~2000pa;
accuracy: + 1%FS;Hysteresis + 0.1%FS; maximum linear pressure
69Kpa;The response time of pressure sensor 90% is 1S.
4. Smoke exhaust capacity: 8000m³/H
5. The wind speed signal is automatically fed back to achieve
automatic wind speed closed-loop control, with more stable wind
speed and strong anti-interference ability.
Wind speed test of combustion chamber
1. Set the speed of the Steiner Tunnel Combustion Chamber in the
computer system, and monitor the wind speed in real time, then
output the wind speed curve.
2. The speed range of the combustion chamber is 0~8m/s, and the
wind speed measurement resolution is 0.001m/s
3. The detection range is 0 ~ 250Pa, the accuracy is ± 0.5Pa, and
the system indication pressure test accuracy is ± 2Pa.
Temperature control collection
1. Steiner Tunnel Furnace Tester is equipped with 3 OMEGA K armored
thermocouples to monitor the temperature change of the exhaust
pipe, the accuracy is 0.1 C.
2. The parameters of the thermocouple:Less than 0.25mm wire
diameter; temperature accuracy 0.1 degrees.
3. The temperature test range is 0 C ~1300 C.
Data acquisition and control system
1. Labview control system which is stable and reliable system;
2. Standard control cabinet, equipped with Dell computer, 19 "LCD
display;
3. The system has 16 bits high precision data acquisition module.
4. System time recording accuracy 0.1s
5. Achieve real-time data monitoring and accurate recording;
6. Real time display of system operation status; sound and light
alarm under fault condition;
7. Control cabinet can connect printer and print report.
8. With Sound alarm and alarm display function.
9. The control cabinet can be connected with computer.
10. PLC control system with functions of automatic ignition,
ignition failure dete
11. The software interface and control panel interact to control
the operation.
1 | Electrical | AC 380V, 50/60hz, 30A |
2 | Ambient Temperature | Operating 15°C to 35°C |
3 | Gas | Methane and air compressor |
4 | Utility | Crane |
5 | Size | 1300 mm (L) x 1100 mm (D) x 2100 mm (H) |
6 | Weight | 1700KG |
7 | Applicable standards | UL910,NFPA262,ASTM E84,UL723 |