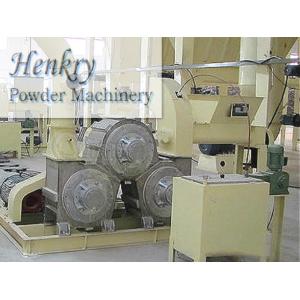

Add to Cart
Continuous Modification Production Coating Machine For Ultrafine Powder Coating
The reason why we use coating machine for non-metallic mineral powder:
Surface modification of non-metallic mineral powder by coating
machine is an inevitable trend in the development of modern high
technology and new materials. It is widely used in non-metallic
mineral fillers, such as pigments, rubber, adhesives, polymer
materials, functional materials and coating industries. After
modification of the non metallic mineral powder, it can not only
greatly improve the compatibility of the inorganic mineral filler
and the organic polymer, increase the interfacial binding force,
enhance the mechanical strength and comprehensive performance of
the material, but also greatly improve the powder filler. The
filling volume reduces the production cost and at the same time can
give the product some special physical and chemical properties. For
this reason, the surface modification of inorganic mineral powder
is particularly important.
This coating machine's unique modification cavity design and
self-heating heating mechanism meet the powder surface continuity
modification process requirements. It has the features of strong
continuity, higher coating efficiency, higher activation index and
higher processing capacity. The high-speed friction and shear
between the stator and the stator have the functions of
disaggregating and breaking up the material at the same time. Since
its introduction to the market, the equipment has been tested and
tested by many companies.
Main Components of Coating Machine:
Non-metallic mineral powder coating machine includes the following
parts: raw material silo, pharmaceutical barrel, screw feeder,
pharmaceutical metering and filling system, modification machine
host, cyclone collector, pulse dust collector, induced draft fan,
electric control system, etc. Partly composed.
The coating machine is composed of three shaped modification
cylinders. The dried powder and the precisely metered modifier
enter the modification cylinder at the same time. The main motor
drives the high-speed rotating rotor to make the material flow as a
snail, And the heat generated by relatively high-speed shearing,
collision and friction with the stator installed on the reforming
cylinder rapidly forms a film for modification.
Technical Advantages of Coating Machine:
1. Good dispersion of powder and surface modifier, uniform coating
of particle surface, less amount of modifier; especially suitable
for surface modification of ultra-fine powder.
2. The coating machine can run continuously for production with
large processing capacity, which is suitable for industrial
production of various scales.
3. The usage rate of the modified agent is high, the dosage is
small, the powder coating rate and activation index are high, and
the energy consumption is low.
Advantages of coating machine:
Calcium carbonate powder coating machine can has the following advantages: good dispersion of powder and modifier, better powder modified rate, low labor intensity, higher productivity and suitable for large-scale production. The ultrafine powder coating machine is often installed with ultrafine powder mil for producing coated ultrafine inorganic powder, especially for plastics, polymer-based composite materials such as rubber, agglomerates, painting, inks, organic fillers and pigments.
Working Principle of coating machine:
There is a combination of shear, collision, air vortex and friction in the ultrafine powder coating machine chamber, which can disperse the powder and increase collision between powder and modifier. The mixing time of powder and modifier can be increased by the air vortex. And the temperature can be kept at a suitable degree with the help of collision between powder and modifier.
Advanced artificial intelligence technology is used to adjust all process parameters and modifier&powder feeding-rate. This can help to achieve the absorption of modifier to powder surface and stabilize the modified powder quality.
Technical Data of coating machine:
Technical Data Model | Main Machine Power(KW) | Spindle Speed(R/Min) | Capacity (Kg/h) | Blower Power(KW) | Dusting Area (m²) |
300 | 55.5 | 4500 | 500-2000 | 5.5 | 60 |
600 | 111 | 2700 | 1500-3500 | 22 | 150 |
900 | 225 | 2000 | 3000-7500 | 45 | 300 |