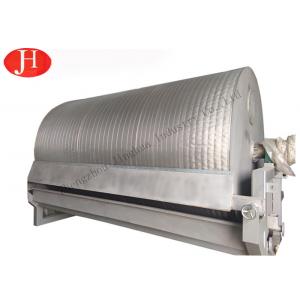

Add to Cart
Zhengzhou Jinghua Industry Vacuum filter combines the latest technology and years experience into a whole, which is widely used for starch milk dewatering in .potato starch,wheat starch,cassava starch and sweet potato sago starch project.
Model | KLG12 | KLG20 | KLG24 | KLG34 |
Vacuum degree(Mpa) | 0.04~0.07 | 0.04~0.07 | 0.04~0.07 | 0.04~0.07 |
Content of solid(%) | ≥60 | ≥60 | ≥60 | ≥60 |
Feeding density(Be°) | 16-17 | 16-17 | 16-17 | 16-17 |
Capacity(t/h) | 4 | 6 | 8 | 10 |
Power | 3 | 4 | 4 | 4 |
Drum rotary speed(r/min) | 0-7.9 | 0-7.9 | 0-7.9 | 0-7.9 |
Weight(kg) | 3000 | 4000 | 5200 | 6000 |
Dimension(mm) | 3425x2312x2213 | 4775x2312x2213 | 4785x2630x2600 | 5060x3150x3010 |
There are four steps to making potato starch
1.Cleaning:To remove the stone sand and from the raw material ,and
peel it.
2.Crushing :To destroys the fiber structure and makes the starch
particles free.
3.Separator:To removing sand ,mud from starch slurry, degreasing,
microslag separation, protein separation, washing and concentration
of all
kinds of starch and modified starch emulsion.
4.Drying and Packing:To dehydrator the wet starch, sifter and
packaged.
Pre-sale service
1.Introducing detail features and application of the products to
customer.
2.Selecting economical and practical machines for customer
3.Providing operation data of the related machine.
4.Providing means of trial performance for customer.
5.Flow chart and factory designing layout .
Sale service
1.Recommending engineering conditions required for installation of
the machine.
2.Communicating the manufacturing progress of machines with
customer in time.
3.Project planning and design services.
After-sale service
1.Training of equipment maintenance and operating personally.
2.Installation and commissioning of equipment until everything is
functional.
3.One year warranty and Providing long-term maintenance service and
spare parts.
4.Giving technical support to customer for developing new product.
5.Engineers available to service machinery overseas.
6.Provide English Version of
Installation/Operation/Service/Maintenance Manual.
FAQ
Q1:Can you provide detailed parameters and drawings of the
equipment?
A:Yes, you can contact us by email, we will provide you with the
detailed parameters and drawings of the equipment.
Q2:How long is the warranty period of the equipment?
A:After the successful installation and commissioning of the
equipment, there is a one-year warranty period.
Q3:What kind of after-sales service do you provide?
A:Provide after-sales service for customers through telephone,
video guidance, on-site maintenance, etc.
Q4:Are your products can be assured ?
A:Our machines are all have CE certificate by SGS, TUV.
Q5:If we show you our layout of factory, can you help us to design
the whole process line?
A :Yes, our experienced engineers and technical employees can help
you to arrange the layout and installation of whole process line
based on your real situation;
Q6:If we have samples of new products, can you help us to analysis
and design the machine?
A:Yes, Our technical department can help you to analysis, design
and test the new products you offered.