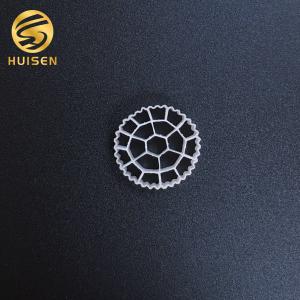

Add to Cart
Mbbr Carrier K3 Filter Media / K3 Bio Media
Product Description
The basic design idea of MBBR is to be able to operate continuously
without blocking and backwashing, with small head loss and large
specific surface area. This can be achieved by the biofilm growing
on a smaller carrier unit, and the carrier moving freely with the
flow of water in the reactor. In aerobic reactor, the carrier is
moved by aeration; in anoxic / anaerobic reactor, the carrier is
moved by mechanical agitation. In order to prevent the loss of
filler in the reactor, a porous filter screen can be set at the
outlet of the reactor. MBBR is generally rectangular or cylindrical
structure. The rectangular reactor can be divided into several or
no grids uniformly along the length of the tank with baffles.
Generally speaking, the flow in the reactor is push flow, and in
each cell, due to aeration fluidization, the flow is completely
mixed. The specific gravity of the tank is close to that of water,
polyethylene or polypropylene suspended filler with large specific
surface area. The attached surface of biofilm in the reactor can
reach 500m2 / m3, and the actual specific surface area (inner
surface of filler) can reach 350m2 / m3. The perforated aeration
pipe is aerated on one side to make the packing circulate in the
tank. The bottom of the cylindrical reactor is provided with a
microporous aeration head. In addition, some reactors are equipped
with not only aeration device but also agitation device. These
agitation devices can make the reactor easily and flexibly used in
the anoxic state.
Technology Parameter
Type | Hole number | Density | Packing numbers | Menbrane-forming time | BOD5 Oxidation efficiency | Applocable temperature |
PE05/K3 | 19 | 0.96-0.98 | >97000 | 3-15days | 2000-10000 | 5-60℃ |
Size | Effictive surface | Porosity | Dosing Rate | Nitrification efficiency | COD Oxidation efficiency | Life-span |
25*12mm | >500 | >90 | 15%-68% | 400-1200 | 2000-15000 | >15years |
Principle of process
The principle of MBBR Process is to increase the biomass and
species in the reactor by adding a certain number of suspended
carriers to the reactor, so as to improve the treatment efficiency
of the reactor. Because the density of packing is close to that of
water, it is completely mixed with water during aeration, and the
environment for microorganism growth is gas, liquid and solid. The
collision and shear of the carrier in water make the air bubble
smaller and increase the utilization of oxygen. In addition, there
are different kinds of organisms inside and outside each carrier,
some anaerobic or facultative bacteria grow inside, and the outside
is aerobic bacteria, so each carrier is a micro reactor, which
makes nitrification and denitrification exist at the same time,
thus improving the treatment effect.
MBBR Process has the advantages of both traditional fluidized bed
and biological contact oxidation process. It is a new and efficient
sewage treatment method. The carrier is in the fluidization state
by the enhancement of aeration and water flow in the aeration tank,
Then the suspended activated sludge and attached biofilm are
formed, which makes the moving bed biofilm use the whole reactor
space and give full play to the advantages of attached phase and
suspended phase, so as to enhance their advantages and avoid their
disadvantages and complement each other. Different from the
previous packing, the suspended packing can contact with sewage
frequently and many times, so it is called "moving biofilm".
Advantages
Compared with the activated sludge process and the fixed packing
biofilm process, MBBR has not only the high efficiency and
flexibility of the activated sludge process, but also the
characteristics of the traditional biofilm process, such as
resistance to impact load, long sludge age and less excess sludge.
(1) Filler characteristics
Most of the fillers are made of polyethylene, polypropylene and its
modified materials, polyurethane foam and so on. The specific
gravity is close to the water, mainly cylindrical and spherical,
easy to film, no agglomeration, no blockage, and easy to remove
film.
(2) Good denitrification capacity
The nitrification and denitrification can take place in a single
reactor, which has a good effect on the removal of ammonia
nitrogen.
(3) Good removal effect of organic matter
The sludge concentration in the reactor is higher, which is 5-10
times higher than that of the conventional activated sludge
process, and can be as high as 30-40g / L. The treatment efficiency
of organic compounds is improved, and the impact load resistance is
strong at the same time.
(4) Easy to maintain and manage
There is no need to install packing bracket in the aeration tank.
It is convenient to maintain the packing and the aeration device at
the bottom of the tank. At the same time, it can save investment
and floor space.