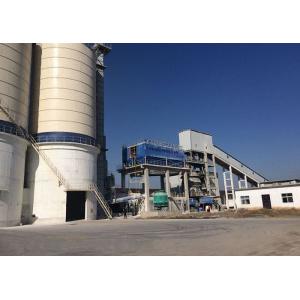

Add to Cart
Slag Powder Production Line is the equipment specializing in producing fine and superfine powder of non-inflammable, non-explosive and brittle materials with Moh's hardness under six, such as calcite, chalk, limestone, dolomite, kaolin, bentonite, talc, mica, magnesite, illite, pyrophyllite and vermiculite, sepiolite, attapulgite, rectorite, diatomite, barite, gypsum, alunite, graphite, fluorite, rockphosphate, Kalium ore, pumice, etc., totally more than 100 kinds of materials.
Features and Advantages:
1. Comprehensive service
We ZK company is the professional slag powder production line
supplier. We can provide both ball mill and vertical mill
production process, while providing 'turnkey' service from civil
engineering to commissioning.
2. Serious Quality Control
ZKCorp has a strong capacity of manufacturing and could control
product quality seriously with short delivery time. Expert
Installation and After-service Team could ensure to finish plant
installation and start running on time.
3. Low cost and proper investment.
Slag Vertical Mill Production Line from ZKCorp engages the
advantages of simple process flow, high-efficiency of grinding,
great drying capacity, efficient Powder-classifying,
easily-adjustable outputting size, low noise and
electricity-consumption, small mill consumption, high degree of
automation, low running expense, which make it suitable for small
and middle plant owner.
Working Principle:
After crushed by hammer crusher, the large materials become small
ones and are sent to storage hopper by elevator, edge of then
evenly sent to the upper distribution plate of the turnplate by
vibrating feeder and sloping feeding pipe. When the grinding mill
is at work, all the grinding rollers are rolling in the ring, and
the materials are driven to the edge of the turnplate by the
centrifugal force and fall down into the grinding chambers where
the materials are repeatedly pressed, crushed and grinded by the
rollers. The high-pressure air blower constantly inhales air within
the grinding mill and, in turn, the air flow with crushed materials
are brought to the classifier whose high-speed impeller will screen
the airflow: the unqualified particle size will fall and return to
the mill for being reground while the qualified particle size mixed
with air will go into the cyclone powder collector. Most of the
qualified powders will fall an exit from the discharging valve at
the bottom; a small proportion of the fine powders, with airflow,
moves to the dust cleaner, and clings to the surface of the filter
bags. At the same time, the fine powders clinging to the surface
fall down by the sudden vibration of the filter bags, which is
caused by the instantly ejected high-pressure gas controlled by the
pulse valve. The materials from the above two lots are sent by the
conveyor at the bottom to get finished powders packed. In addition,
filtered clean air will be emitted from the air outlet of muffler
in the end.