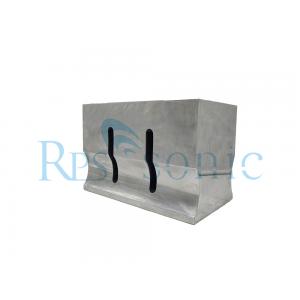

Add to Cart
Parameter:
Item | parameter |
Frequency | 15Khz |
Welding area | 127*33mm |
Material | Alumium alloy |
Connect screw | M16 |
Introduction:
The ultrasonic welding horn contains several key acoustic vibration characteristics such as
resonance length, amplification factor, strain maximum point, and
position of displacement nodes. The most simple and commonly used
ultrasonic welding horns are divided into exponential shape,
catenary shape, conical shape and stepped shape according to the
shape, and they all belong to a single horn. Welding horns should
be designed and developed separately for different welding
applications. RPS-SONIC has more than ten years of practical
experience in ultrasonic design. We can design the corresponding
horn according to the welding needs of customers. Then, the natural
frequency and modal analysis are performed by the finite element
method, and a new horn is designed to meet the functional
requirements of effective transmission and uniform distribution of
vibration energy. In the design process, combined with the
parametric modeling, full factor experimental design optimization
(DOE) and probabilistic design system (PDS) modules of ANSYS, the
parameter design and robust design are performed, and the geometric
size is adjusted so that the natural frequency of the horn matches
the ultrasonic frequency The corresponding modal amplitude is
uniform on the working surface, which reduces the problem of local
structural stress concentration, and has good adaptability to
changes in parameters of materials and the environment. The
designed tooling is completed and put into use at one time, which
avoids the waste of time and cost caused by repeated trimming of
the tooling. Through practical cases, the longitudinal vibration
theory of a single horn is compared with the actual results of the
hornand the finite element analysis. It is verified that the
theoretical method is suitable for the design of four types of
plastic welding horn with simple cavities. The prepared parameter
solution and model drawing program can be used for rapid prototype
design of ultrasonic plastic welding horns. Compared with the
current ultrasonic plastic welding horns, which rely heavily on finite element analysis and empirical
design methods, rapid prototyping methods are more accurate,
efficient, and easy to operate.
With the help of the software of the finite element analyzer, the
reject rate of the hornis greatly reduced, and the output of the
horn is evenly and effectively maximized.
The main issues for ultrasonic welding horn:
1) Uneven amplitude across the face of the horn was causing a weak weld at both ends of the seal area and
2) The horns were cracking and had to be replaced at an unacceptable rate .
Both of these problems are caused by the uneven force on the cross section of the horn. The horn received too much ultrasonic power at a point, which caused cracking. At the same time, too much energy gathers at one point, resulting in insufficient capacity of other parts, low output, and uneven welding. How to effectively avoid this problem requires us to work hard when designing. Using the FEA analyzer, finite element analysis is performed when the horn is designed, and the force on the horn section can be clearly known. The uniform and strong force on the horn section is the ideal state. as the picture shows:
Why RPS-SONIC HORN:
1. Every horn will be designed by FEA system , so that to confirm the End face of the ultrasonic horn with uniform force
2. All ultrasonic horns with three months warranty.
3. Specialized in high power ultrasonic for more than ten years
4. Every ultrasonic horn with 24hours old testing before shipment.
5. Good packing, no packing problem during the 10 years exporting business.
6. Every customer will get purchase records and there are certain rewards after accumulation
Service and shipment