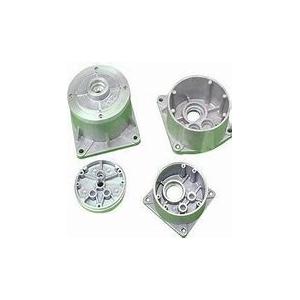

Add to Cart
ADC-10 Aluminum Alloy Die Casting Manufacturing Process Mechanical Equipments
Die Casting Manufacturing Process Description
1. Drawing: Provide by customer, or design according as the sample.
2. ODM we have the client's idea or draft first,then our
experienced engineer will build the best design and manufacturing
technology.finally our sales will supply the verified design and
solution to our client for confirming.
3. OEM that means Customer design or samples will be very
welcome,we will follow client standard to manufacturing this
product 100%.
Die Casting Manufacturing Process Range
Name | ADC-10 Aluminum Alloy Die Casting Manufacturing Process Mechanical Equipments | |||
Material: | Aluminum (6061-T6, 6063, 7075-T6,5052) etc... | |||
Machining Process: | CNC Machining, CNC turning, CNC milling, CNC lathe machining, CNC boring, grinding, | |||
CNC drilling etc... | ||||
Surface treatment: | Clear/color anodized; Hard anodized; Powder-coating; | |||
Sand-blasting; Painting; | ||||
Nickel plating; Chrome plating; Zinc plating; | ||||
Black oxide coating, Polishing,wire drawing etc... | ||||
Gerenal Tolerance: | CNC Machining: 0.015 | |||
(+/-mm) | Turning: 0.015 | |||
Grinding(Flatness/in2): 0.015 | ||||
ID/OD Grinding: 0.015 | ||||
Wire-Cutting: 0.03 | ||||
Production capacity: | depend on complicacy of different products and the quantity | |||
Experience: | 10 years of CNC machining products | |||
10 years of casting products | ||||
5 years of forging products | ||||
We have a senior design team to offer perfect modification suggestions. |
Die Casting Manufacturing Process Features
Our Advantages
1. We are the biggest lost foam mould manufacturer in China, we
focus on high challenge lost foam mould and we have large gantry
machining centers,30 sets imported high speed machining center,more
than 40 sets general machine tool equipment;
2. We have 36 senior mould designers, to ensure reasonable / safety
/ high efficiency mould design and ensure the fast mould delivery
and rational mould structure, make the process more safer and the
production efficiency more higher;
3. We using numerical control machine tool to manufacture the mould
cavities, to ensure a even thickness ;
4. We using ZL104 Aluminium to casting the mould, to manufacture a
high strength mould;
5. For the big mould, we using Ø22*1 copper tube as cooling pipe,
with water spray system, to get a nice cooling effect;
6. We Have (TEF10N) coating on the mould surface, it can reduce the
friction, anti water/static electricity/acid-base/high-temperature,
with this we can ensure the pattern has smooth surface without
distrotion, and easy to demould;
7. All the screws we using stainless steel screw, easy to
disassemble during maintenance;
8. For the big mould chest, we using 18-20mm thick wrought
aluminium plate, to offer high strenght cavity ;
9. For the complex mould which is difficult to demould, we can
manufacture the automaitc mould with take out device ;
10. We produce the pattern sample to customer after finish the
mould, when the pattern was qualified, then we do exceptance job
for the mould ;
11. We have the Hexagon coordinate measuring instrument imported
from the Switzerland to have a test make sure our mould qualified.
Company profile
Luoyang Liushi mould Co., Ltd was established on 2001, which is
National Standard Setting Unit for Lost Foam Casting Mould. The
company is located in the Millennium Emperor, peony flower city of
Luoyang City. We have 9800 office building, and 22000 workshop,
which is well equipped with research, development, design, foundry,
machining, assembly, surface treatment and other equipment. It′s a
Luoyang municipal R&D center and technology center.
Company technicians can provide on-site guide mould assembly, test production, free repair and complete technology for lost foam casting proecss according to customer demands. With the business philosophy of "careful design, lean manufacture, best service, perfect quality", we strive to provide satisfactory products and services for customers. After years of development, our company has become the preferred mould suppliers of many lost foam casting manufacturers and the exclusive supplier.