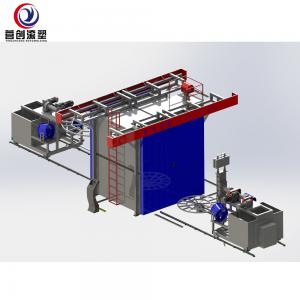

Add to Cart
Rotomolding Tables And Chairs, Rotomolding Equipment, Rotomolding Mold Factory
The rotational molding process is a high-temperature, low-pressure
plastic-forming process that uses heat and bi-axial rotation to
produce hollow, one-piece parts.
During the heating stage, the mould slowly rotates in two planes
(bi-axial rotation).
The process consists of four distinct phases:
1, according to customer demand, we determine efficient and
reliable equipment technical information (including drawings, data,
models and configurations)
2, waiting for the customer to determine the solution we provide,
sign the legal document (supply contract) if the joint discussion
plan is consistent
3, according to customer needs, we began to arrange equipment
production, cutting, welding, assembly, and factory commissioning
according to technical drawings.
4. Inform the customer to come to the factory acceptance equipment
after the commissioning of our factory equipment is completed.
5. After the equipment is qualified, the equipment will be
disassembled, packaged, and the container will be loaded and
transported to the port.
6. The customer arranges the factory personnel to arrive at the
customer's site within one week after receiving the equipment to
guide installation, commissioning, production and training.
7, complete the entire service of the device
1. The oven adopts an inner circular oven structure, which has high
space utilization and is more energy-saving.
2, the oven uses a fabricated structure, an oven is divided into 4
or 5 and 6 pieces of assembly
3, the heating method adopts the principle of hot gas going up,
heating faster, high efficiency, more energy saving
4, the burner is imported from the Italian Liya Road brand
5, the control system uses Siemens S7-1200 network cable
communication method to collect data, reduce the problem of
conventional lines, the line laying is more beautiful
6, low-voltage electrical appliances using Germany Schneider
configuration, more stable and durable
7, the whole machine is equipped with a remote maintenance module,
and the operation of all equipment far away overseas can be viewed
through the Internet at the Yingchuang Rotational Plastic Factory.
8, and all motors are equipped with Siemens variable frequency
control to improve the service life and age of the motor and
reducer, and the gearbox adopts domestic famous brand heavy-duty
gearbox
9, the operation mode is fool-like operation, simpler
10, all transmission parts are geared, more stable, efficient, and
the service life is longer.
11, Yingchuang Rotomolding accepts the personal customization and
design of all customers, and determines the final requirements of
customers according to the needs of customers, so that customers
are satisfied, we can rest assured
Specifications
|
More Details
1. How to choose suitable rotomolding machine?
---Reply: As the machine is custom-made, so we need to know which kind of product are you produced, and the largest product measurement, so we can decide the heating chamber size and recommend suitable machine for you.
2.How to choose a suitable type?
---Reply: We have different kinds of rotomolding machine, such as shuttle machine, carousel machine, rock n roll machine, Lab machine, etc. Our product detail model list can show the whole sizes which can be offered.
3. Are you a manufacturer?
---Reply: Yes, we have been in providing profession solution in rotomolding field for over 6 years. We have our own factory workshop.
4. Before make the order ,can I visit your factory?
---Reply: Yes,of course, warmly welcome. Before you come here, please send us your schedule and your arrival time, so that we can come to pick you up.
5. What is your worktime?
---Reply: All the time, any request shall be replied within 24 hours.
6.What about the delivery time?
---Reply: As machine is customized, so we need 40 to 90 days to produce new machine for delivery, it depends on machine type.