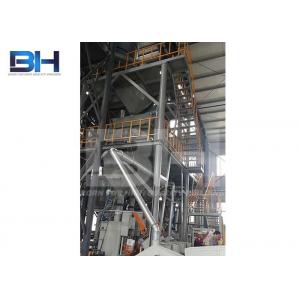

Add to Cart
Ceramic tile adhesive mix mortar machine full automatic dry mortar
plant
Description:
According to requirements of the customers, the system can be
equipped with 3-6 bulk storage bins, the material in which will,
after being processed by the metering and batching system, be
conveyed to pending-for-mixing bin, and then fed into the
high-efficiency biaxial agravic mixer for continuous mixing. The
finished product in conformity with mixing accuracy requirements
can be sent to the finished products bin shortly after mixed.
Moreover, there is design with automatic rationing and packaging
machine at the bottom of finished products bin, allowing for
synchronous auto-packaging operation. Featured with easy and
convenient operation, high efficiency, it can both obviously reduce
labor intensity and effectively reduce dust pollution. This
production line with large investment and high retribution. It is
suitable to large and medium cities with great heat preservation
foundation of walls.
Parameter:
Model | Simple dry mortar plamt | Improved Simple dry mortar plant | Semi-auto dry mortar palnt | full automatic dry mortar plant |
Output | 1-3t/h | 4-5t/h | 5-8t/h | 10-30t/h |
Occupied area | 20m² | 20m² | 50-60m² | 60-100m² |
Total power | 5.5-7.5KW | 6-11KW | 24-28KW | 60-120KW |
Equipment Hight | 3-4m | 3-4m | 6-8m | 8-13m |
Man power | 2-3 persons | 2-3 persons | 3-4 persons | 3-4 persons |
Mixer Volume | 3300*1050*2100(mm) | 2m³ | 2m³ | 2m³, 3m³, 4m³ |
Main components advantages:
Mixing system: The mixer adopts double-shaft paddle-free gravity
mixer, large-capacity mixing bin, short mixing time, high output,
high uniformity and small coefficient of variation. The uniformity
of the secondary mixing material of the finished product bin
(saturator) is maintained and the material is smoothly entered into
the packaging system.
Control system: It adopts advanced PLC programmable automatic
control system for intelligent operation control. The system
displays the weight of each material in real time and automatically
corrects the drop.
Lifting conveyor system: The conveyors of the project are
controlled by computer programs, and the timely feeding is timely
shut down. Weighing and metering is automatically measured by the
control system according to the set recipe, and each raw material
is weighed and weighed automatically.
Packaging system: The valve packing machine is used, and the
packaging speed is high and the output is high.
Dust removal system: The whole set of equipment is completely
sealed without dust leakage. The multi-point dust collector is used
to collect the dust of the feeding port and the discharge port to
optimize the working environment and ensure the health of the
employees.
Installation Site: