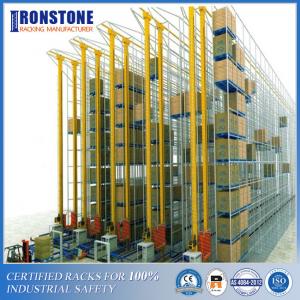

Add to Cart
ASRS Crane Racking System Smart Storage for Warehouse
The ideal system for managing boxes for picking is the automated storage retrieval system, often known as ASRS or AS/RS. The "product to man" principle is used in the ASRS system. The pinnacle of high-density, high-efficiency storage systems is the automatic pick system. A central aisle divides two rows of racks in the mini-load automated warehouse for boxes. The stacker crane moves along the center aisle and is made to automatically pick up palletized items, plastic totes, crates, or trays. Conveyors make up the picking and handling area, which is situated either at the side or one end of the racking.
The load removed from the rack is deposited by the stacker crane of the automated storage retrieval system. Once the operator has completed the operation at hand, the box is returned to the stacker crane, which then sets it back into the racking. The operator then receives the box via the conveyors.
An inventory is maintained in real-time and the position of all the materials in the warehouse is registered by the management software package that oversees the entire automated storage retrieval system. The ASRS system may be implemented into any production or storage process because of its outstanding adaptability.
More details about ASRS
Product | High-end Automatic Storage and Retrieval Racking System | ||
Color | Custom colors follow the RAL system | Material | Steel |
Usage | Warehouse storage and retrieval | Certification | RMI/CE/AS4084-2012 |
Size | Custom size according to warehouse layout | Structure | Integrated comprehensive structure |
Height | Customized ranged from1350mm to 20000mm | Capacity | Customized up to 21000kg/bay |
Width | Customized ranged from 300mm to 2000mm | Thickness | Customized ranged from1.5mm to 3.0mm, |
Feature | Automated picking and storing | Package | Customers' request |
Four Main Components
♦ Automated Stacker Crane with Racking - This equipment locates and removes boxes from the rack system, transports them to the P&D station of the warehouse, and deposits them there. Stacker cranes can move in two different directions: longitudinally (down the aisle while being guided by a rail) and vertically (while positioning the boxes at various levels and/or depths of the rack).
♦ The P&D Station (Picking & Delivery) - The P&D
station, also known as the picking and handling area, is situated
at the front of the racking and makes the mechanical movements
necessary to bring the boxes to the operator or the stacker crane
so that the latter can pick them up and return them to the
warehouse. It is composed of several conveyors that interface with
the stacker crane and the workstations, accelerating the entrance
and exit of goods from the system. Rollers or belts are the two
types of transportation.
♦Computerized Management System - The management system directs all storage activities, maximizing both the use of warehouse time and space. It is the ideal tool for integrating the client's warehouse with their ERP due to its deployment and degree of connectivity. The management of procedures and quick access to all the information is made possible by its software.
♦ Load Unit—Stocking plastic totes and bins of both standard and
non-standard sizes are possible in mini-load warehouses. You might
also use cardboard or metal boxes. The best load unit depends on
the goods being kept.
Automated Storage Retrieval System Benefits Include:
Operation Theory
The ASRS system can be constructed with either a single-deep box on each side of the aisle or two boxes on each side of the aisle (double deep). A single box location in the racking is provided by a single depth. It allows for the fastest possible entering and extraction of boxes. Single deep storage is the best option for businesses that value system performance and flexibility over total storage capacity.
Since all the boxes have direct access, they are typically utilized when the products being stored are all from the same category and are intended for the same amount of consumption. Typically, there is only one box per reference or SKU. Two box depths are available per location in double-deep storage. It is perfect for businesses that need to strike a balance between handling speed and storage capacity. You can double the amount of storage you have by using the two-deep option.
Why Choose Ironstone ASRS Racking System?
Our ASRS system has a wide range of primary advantages. Maximum accuracy and safety are provided, along with rapid execution, organizational enhancements, a contemporary programming design, and adaptability to your demands. The automatic storage and retrieval of boxes using our ASRS system is the easiest and most common method available.
In a single package, it combines the rack system, the machine, the P&D station, and the warehouse administration software. It is created using the plug-and-play principle. This is a standardized set that provides the features and capabilities needed in the majority of these types of warehouses.
Factory Production