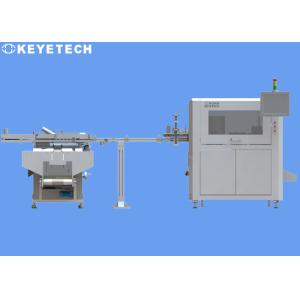

Add to Cart
Deep Learning Automatic Inspection System Neural Networks Aoi Vision Machine
Deep learning image processing is to solve image processing problems by building a "brain-like neural network" and drawing on the method of
human brain processing data. Therefore, any scene involving deep learning requires two necessary conditions: one is the support of big data— Various representative pictures; the second is a powerful computing platform - generally using a GPU computing platform. In actual industrial application scenarios, these two conditions are extremely difficult to achieve, and the implementation cost is extremely high. KEYE TECH AI is a deep learning function launched on the basis of the Kvis general development platform. It combines KEYE TECH's own powerful traditional image processing algorithms to solve most of the above two problems.
Equipmet configurations
The inspection machine adopts high-pixel industrial cameras and high-performance stroboscopic light sources to carry out omni-directional visual inspections for product appearance defects. The equipment can realize 7*24 hours of all-weather operation, and it can be online automatically. Eliminate substandard products.
Name | Automatic Inspection System | Size | 900*800*1850mm |
Computer | Industrial PC | Monitor | 19 inch |
Industrial camera | 2 -6set | Industrial lens | 2-6 set |
Glass turntable | 1 pcs | Samples | Many |
Feeding equipment | vibration plate, direct vibration, controller | Speed | According to the samples |
Application range
Advantages and Features
(1) Neural network inference is completely implemented based on
CPU: The neural network model inference trained by KEYE TECH AI is
completely implemented based on CPU, and the neural network model
training supports both CPU and GPU. Users can flexibly choose a
computing power platform according to the complexity of the model
required by the project, thereby saving unnecessary hardware
expenditures on the computing power platform;
(2) Innovative "deep learning defect filtering" algorithm: use
traditional algorithms to find all possible defect areas, and only
use deep learning to solve the OK and NG discrimination of defect
areas, thus solving the problem of training image data acquisition;
(3) Support the retraining of neural network models: According to
the complexity of the application of industrial scenarios, the
continuous training of models is supported, so that
industry-specific neural network models can be formed.
Precautions
1. The training data set must strictly focus on "quality" and "quantity"
2. Traditional algorithms should be combined with deep learning. Traditional algorithms can do it, don't rely on deep learning
3. Accurately locate specific problems, from "partial" to "whole". The ultimate goal of a machine vision project is to achieve 100% accurate detection, but there will be various issues during project development that affect this result. When an abnormal result occurs, it is necessary to accurately locate the specific link to test and find.
After-sale service
The company has a complete technical service team and rapid response mechanism, and has dedicated service specialists for each customer, who can receive technical consultation and fault reports from customers at any time. And to ensure rapid response to customer emergencies, to ensure that customers receive satisfactory service.During the epidemic or due to special reasons, when after-sales engineers are unable to reach the site, the service center can remotely adjust customer equipment for troubleshooting and technical consultation.
After the equipment arrives at the customer site, the after-sales engineer arrives in time to carry out equipment installation, commissioning, and operation training. The product quality of the whole machine is traceable, and the quality warranty period is 1 year from the date of acceptance. In the event of non-human faults during the warranty period, after-sales engineers will quickly arrive at the site or provide remote guidance for free maintenance.